langy
langys rodshop
- Messages
- 6,095
- Location
- London
It was like summer at the weekend so some progress was made, I ordered some tube for the bedsides and it arrived in time, I knew right from the start welding the tube to the top of the sides was gonna be a pain and also a 2 man job, so I got my mate Gary (chevy2) to help out, I like working with Gary as he knows what he's doing and dn't keep asking "why are you doing it that way "
First job was to get the tube tacked in place, it was cut longer than needed to allow for somewhere to clamp the ends. Welding 16swg sheet to 16swg tube is always a challenge as the tube tends to bow, Tig was out of the question due to the heat involved so we both decided to Mig and quench each weld as we danced around the joint.
We tacked it every 10" while checking with a straightedge first
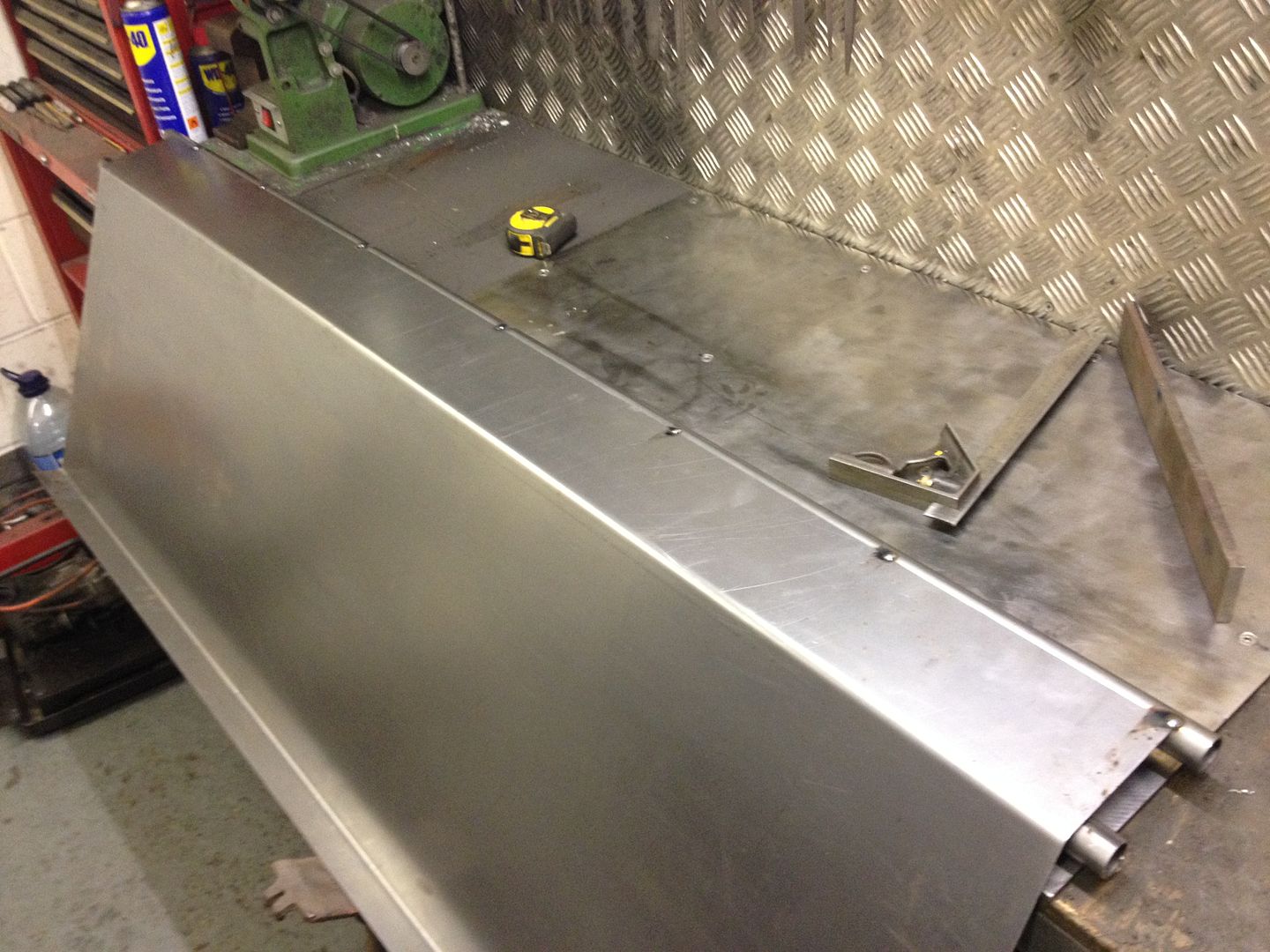
Then clamped it to a piece of 2" x "2 box section, we were both convinced if we laid down 1/4" welds by dancing around in lots of different places and quenching with a damp cloth as quickly as possible every thing would be fine
Here it is unclamped after cooling but when we checked it for straightness it had bowed very slightly, I can correct this with a touch of heat and a damp cloth later as it isn't too bad at all.
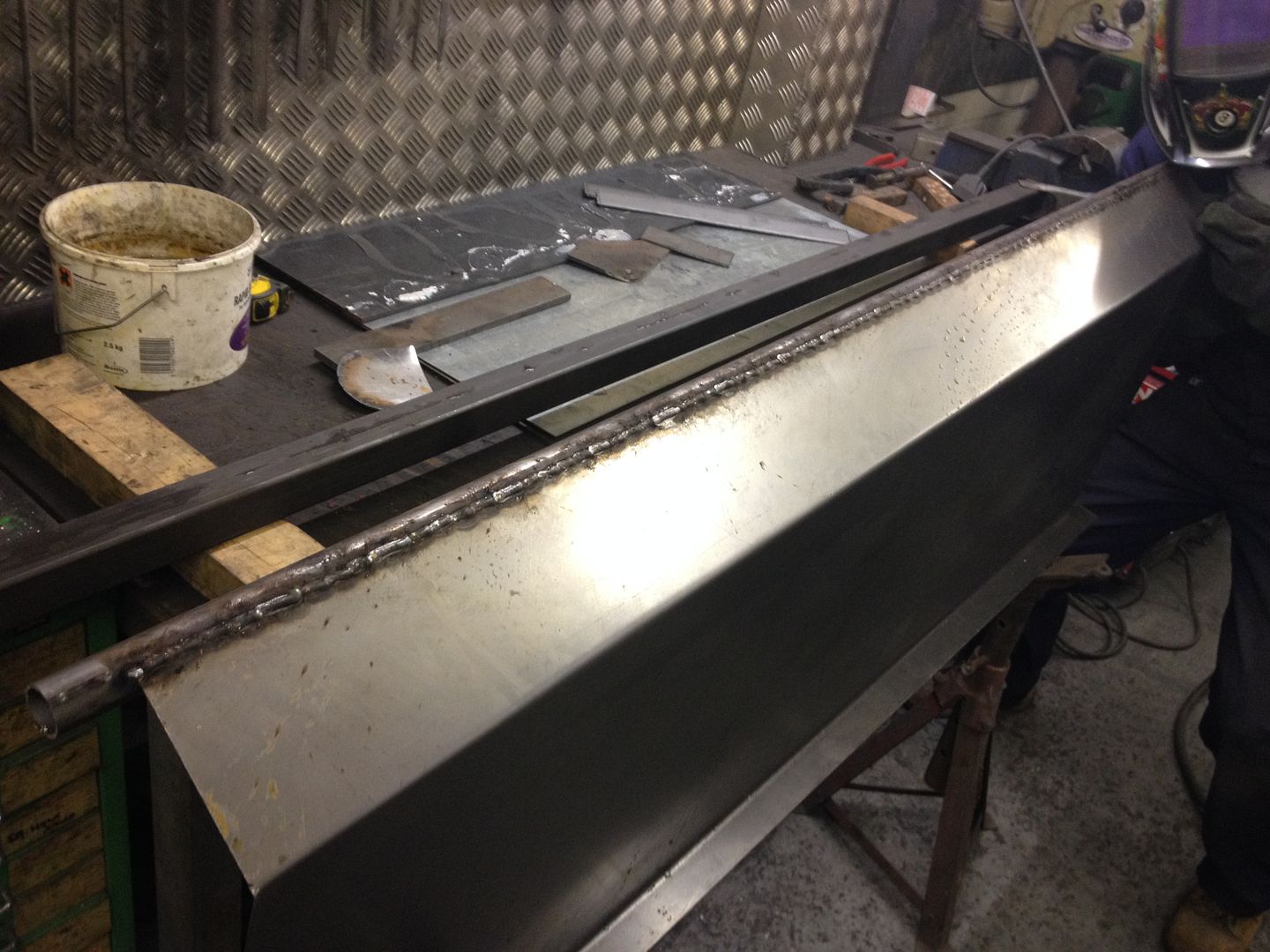
We decided on the other side to try and predict the bow by using a 1/4" packer in the centre and 1/8" outers and only clamp at the middle & ends, we used the same welding & quenching procedure, result was it came out perfectly straight when unclamped
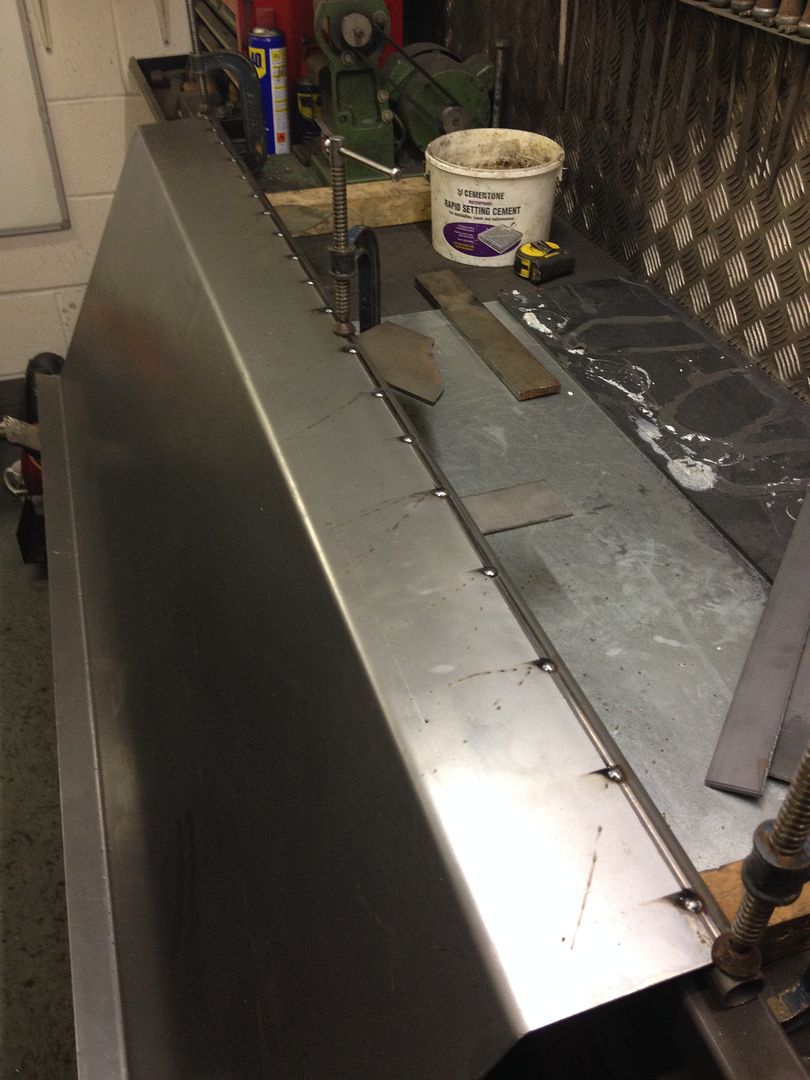
Next job was to sand down the welds and metal finish it all.
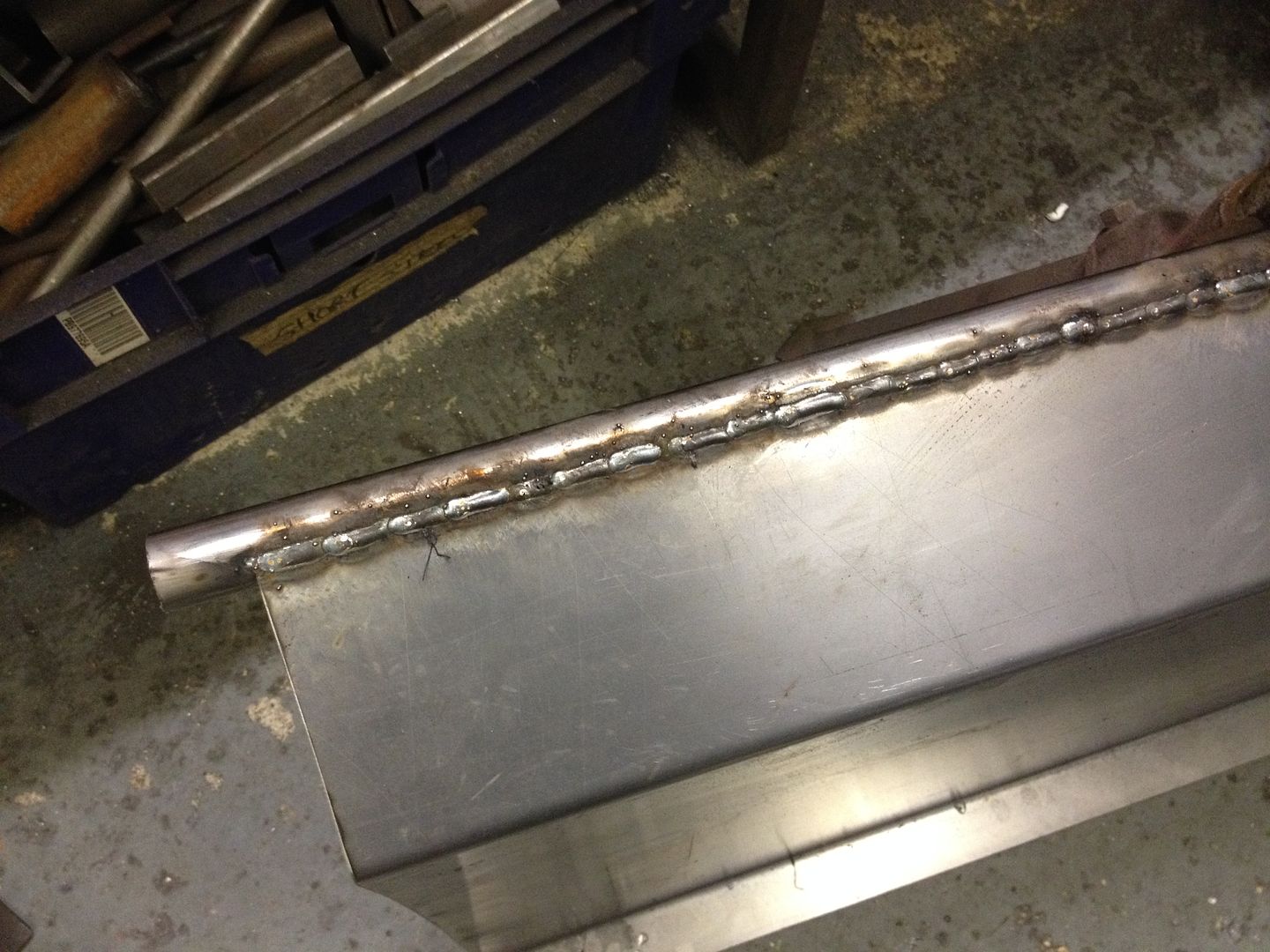
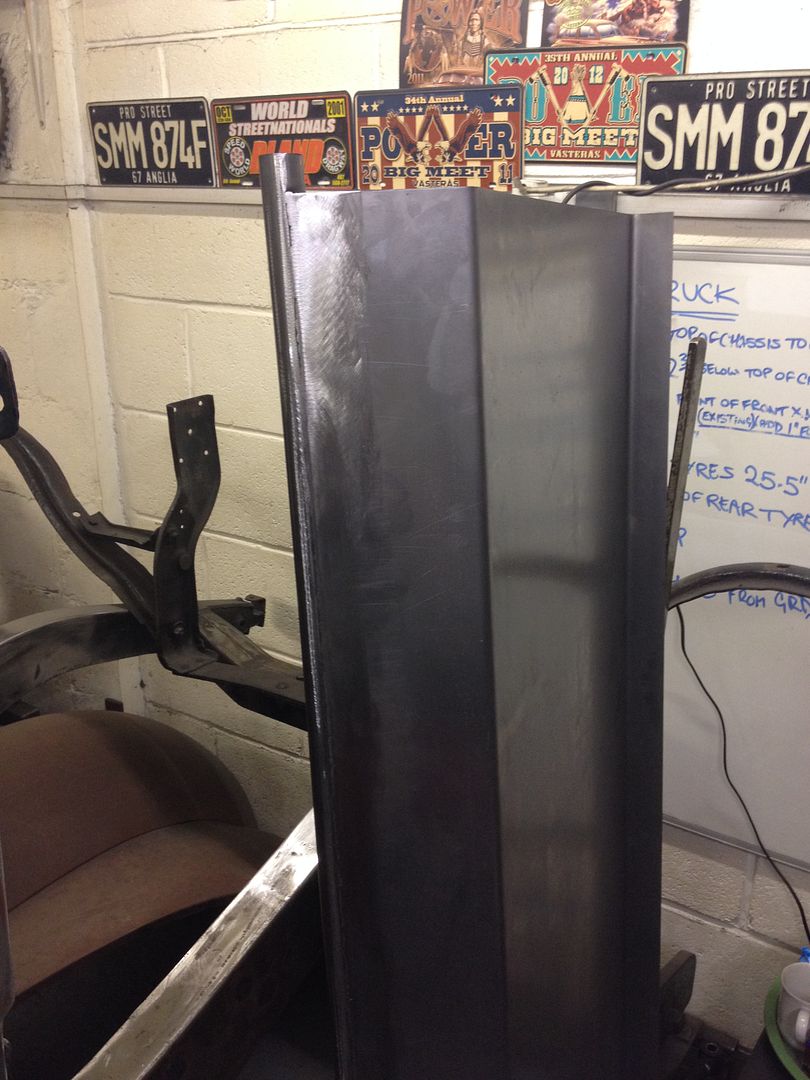
Heres the bowed side and below the straight side
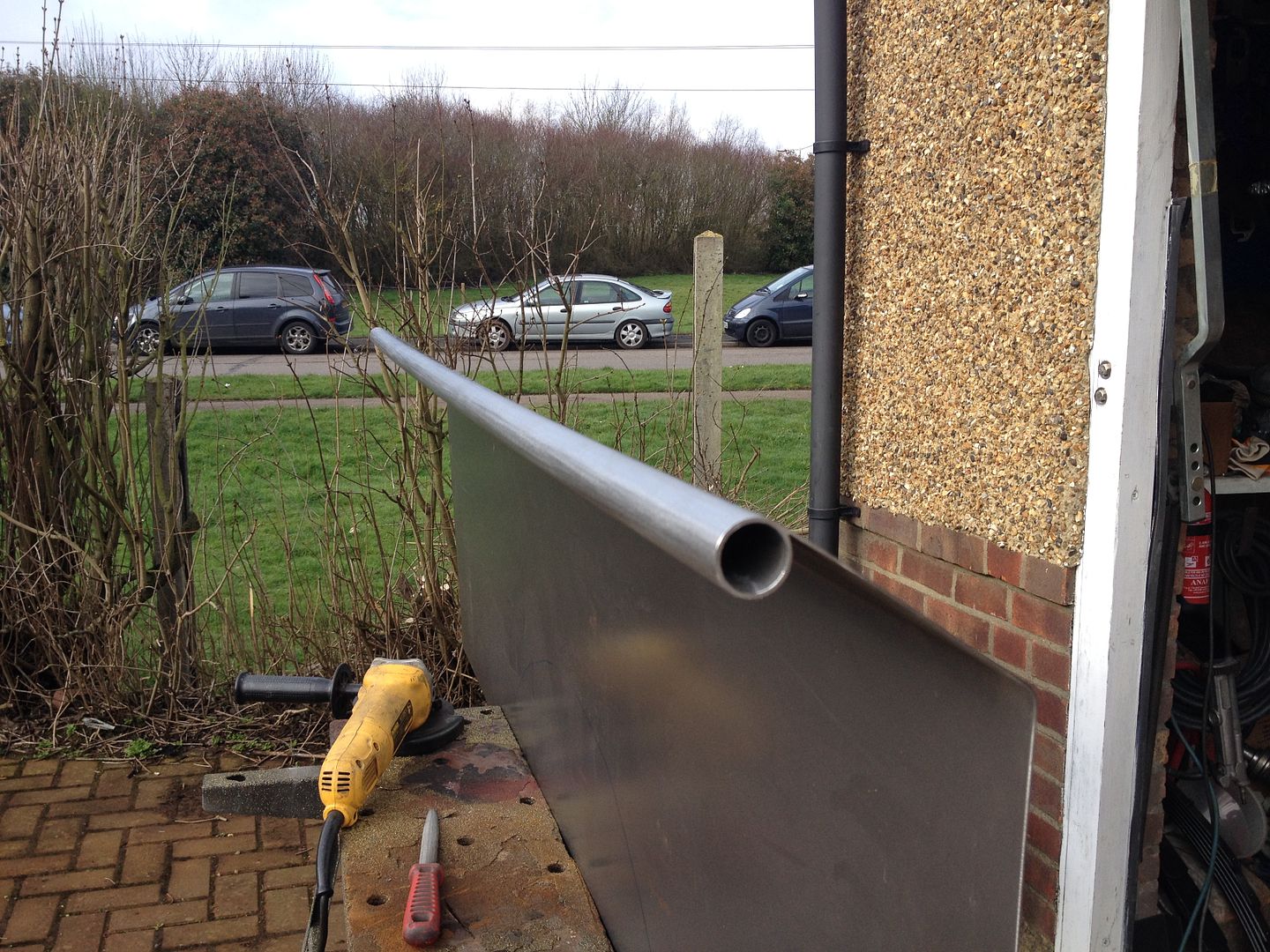
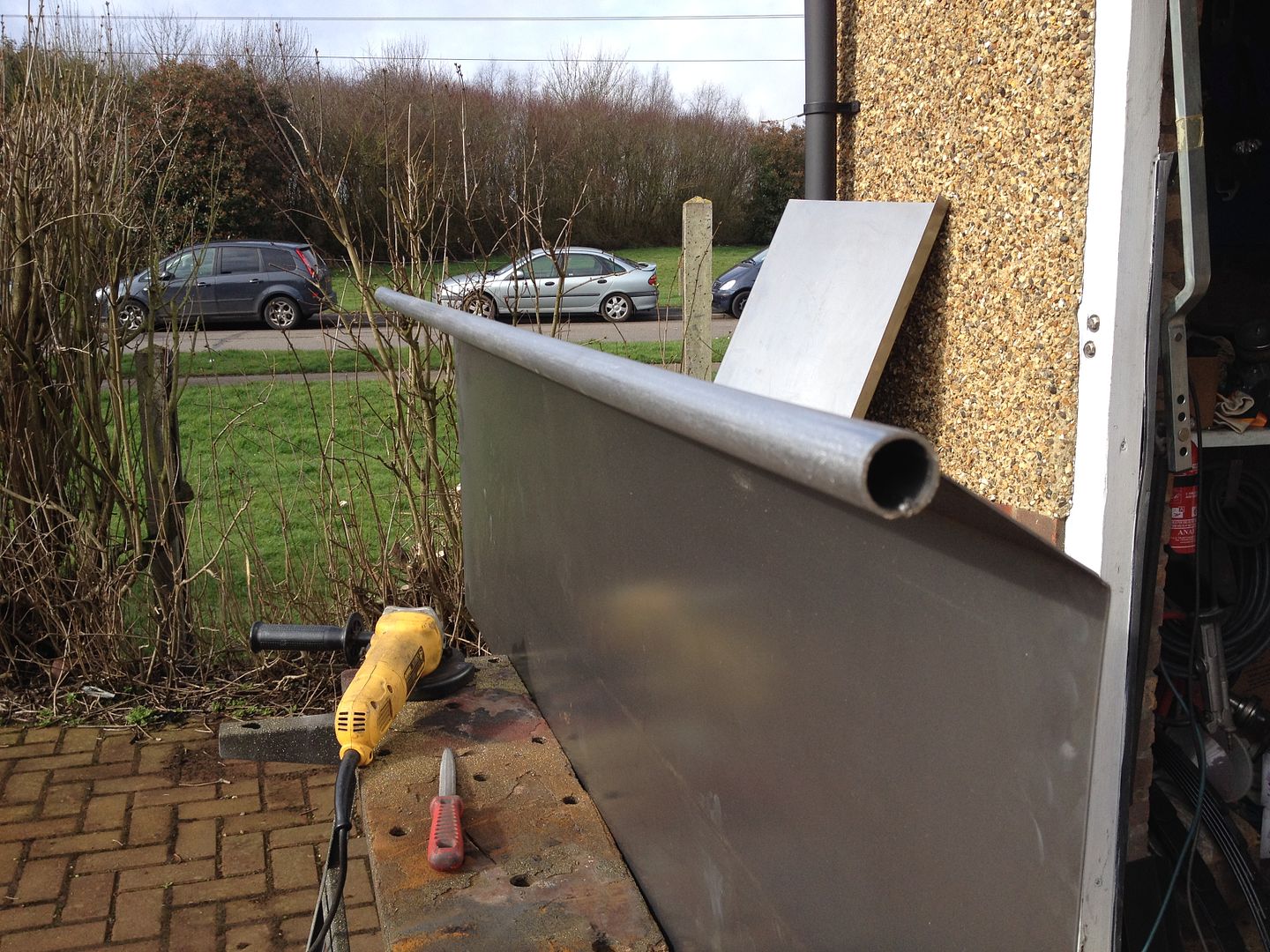
Here they are all metal finished and ready for the stake pockets to be welded on.
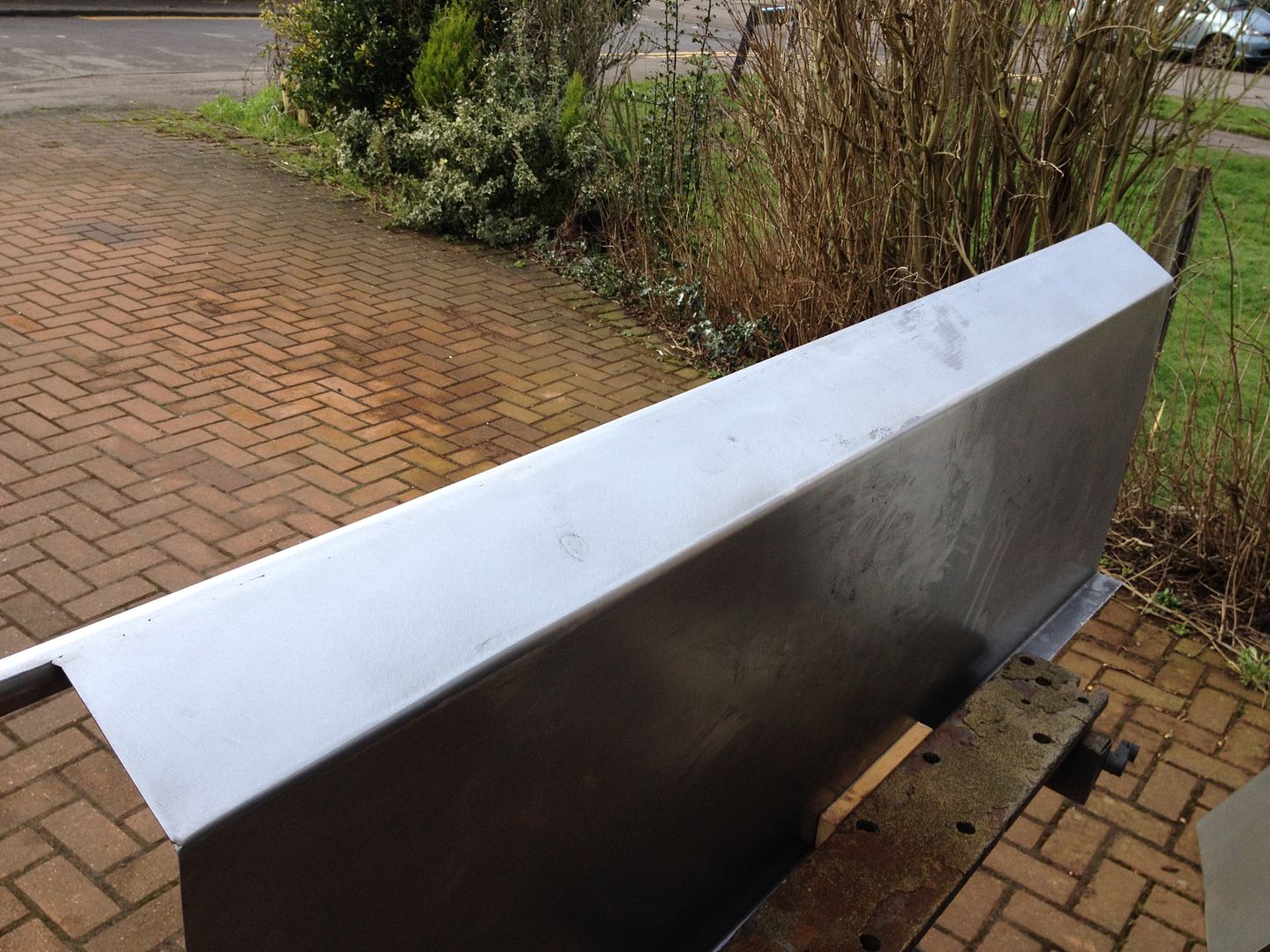
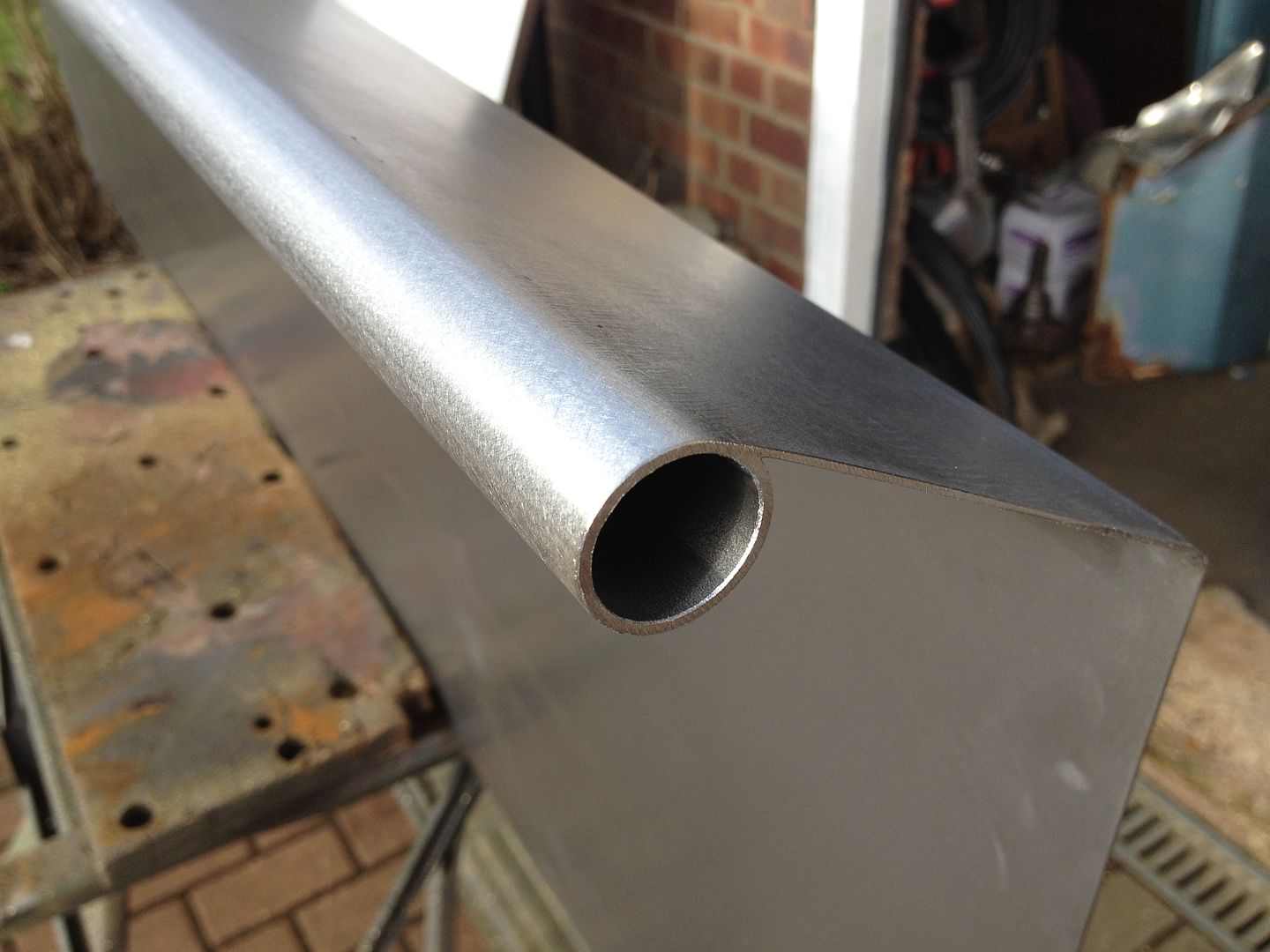
Next job was to mark out and drill the holes so the pockets could be plug welded in place

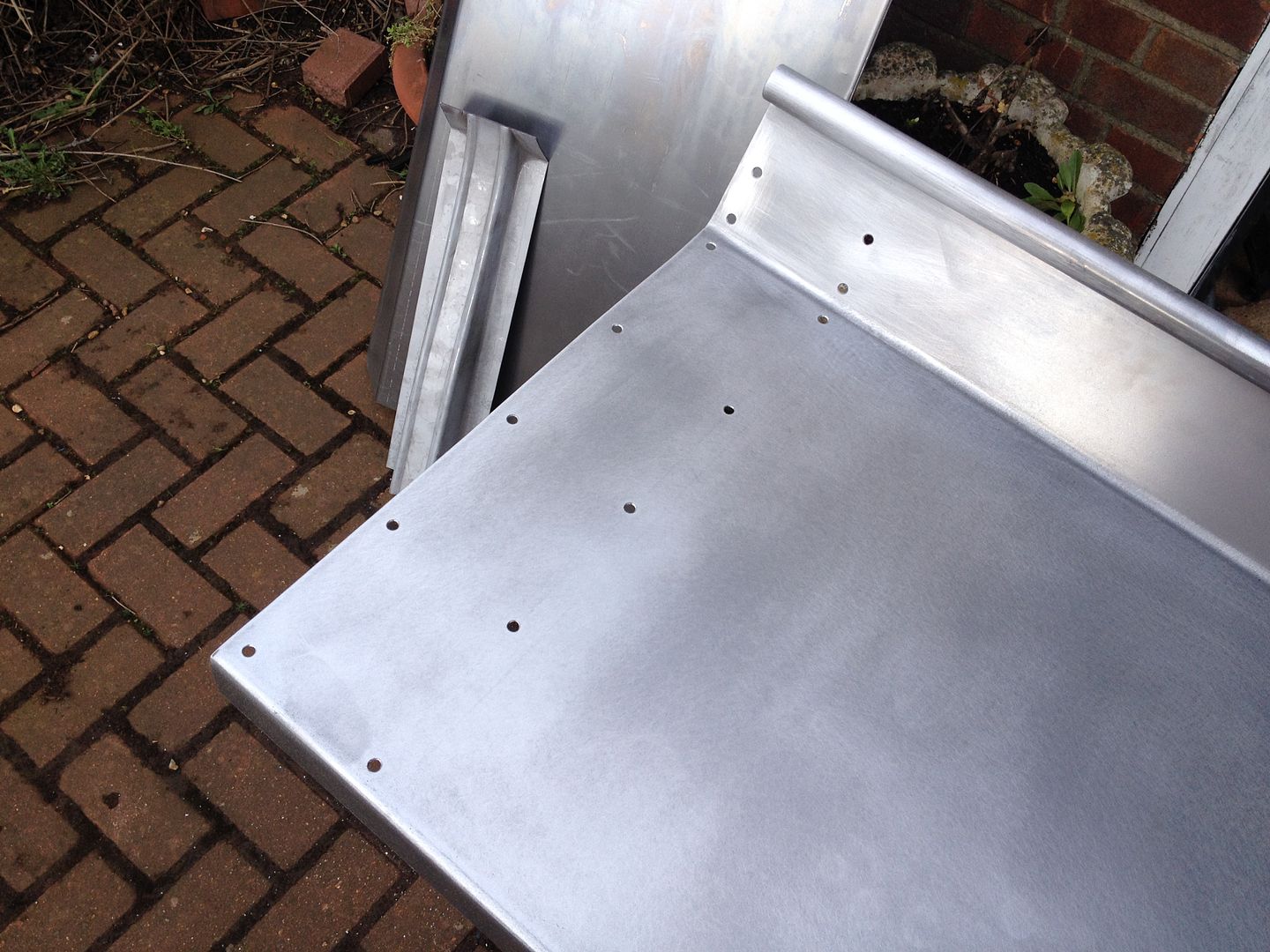
To protect in between the seams 3 coats of Epoxy primer were applied. then the pockets were clamped in place, and thats as far as it got until next time.
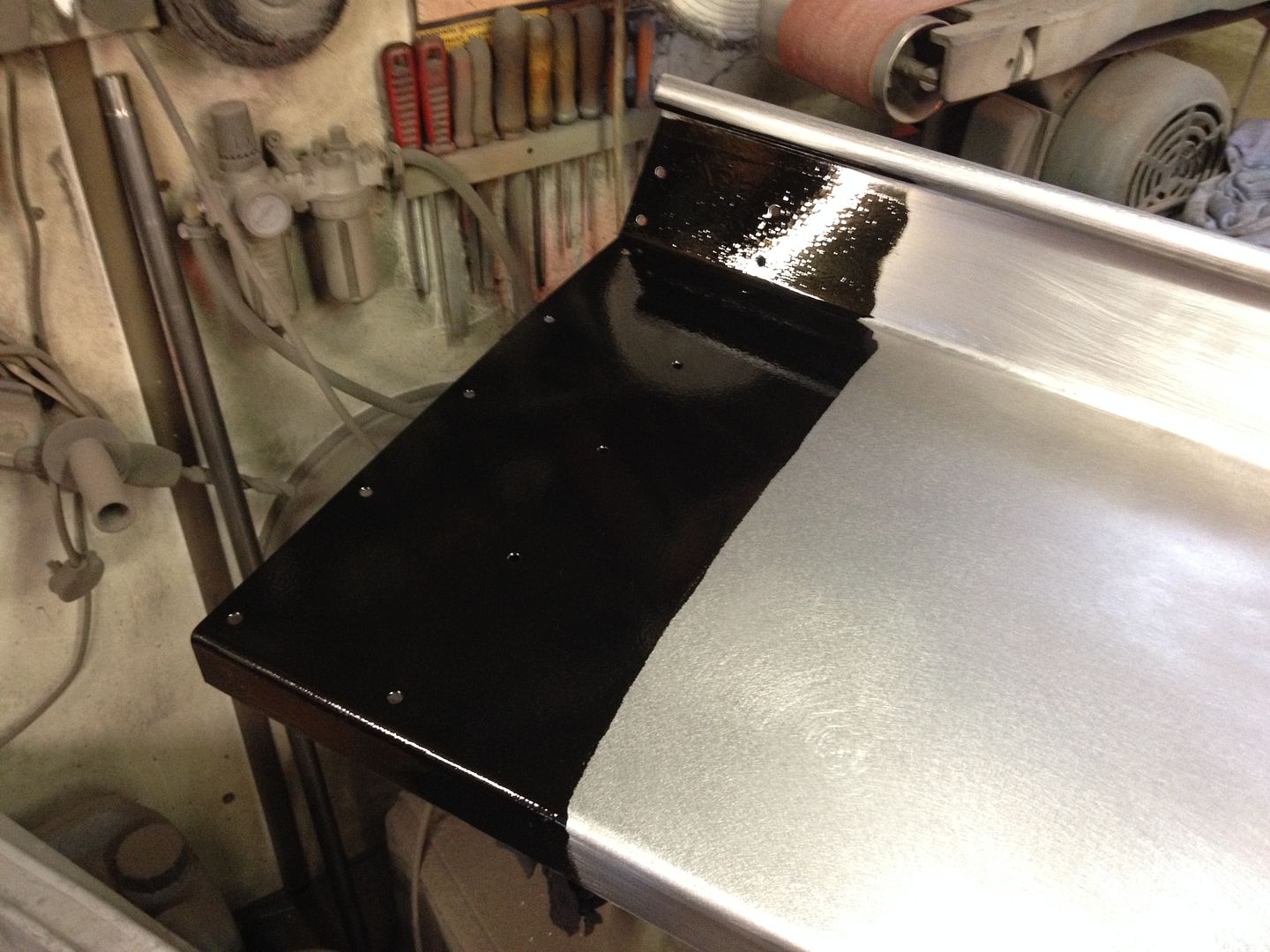
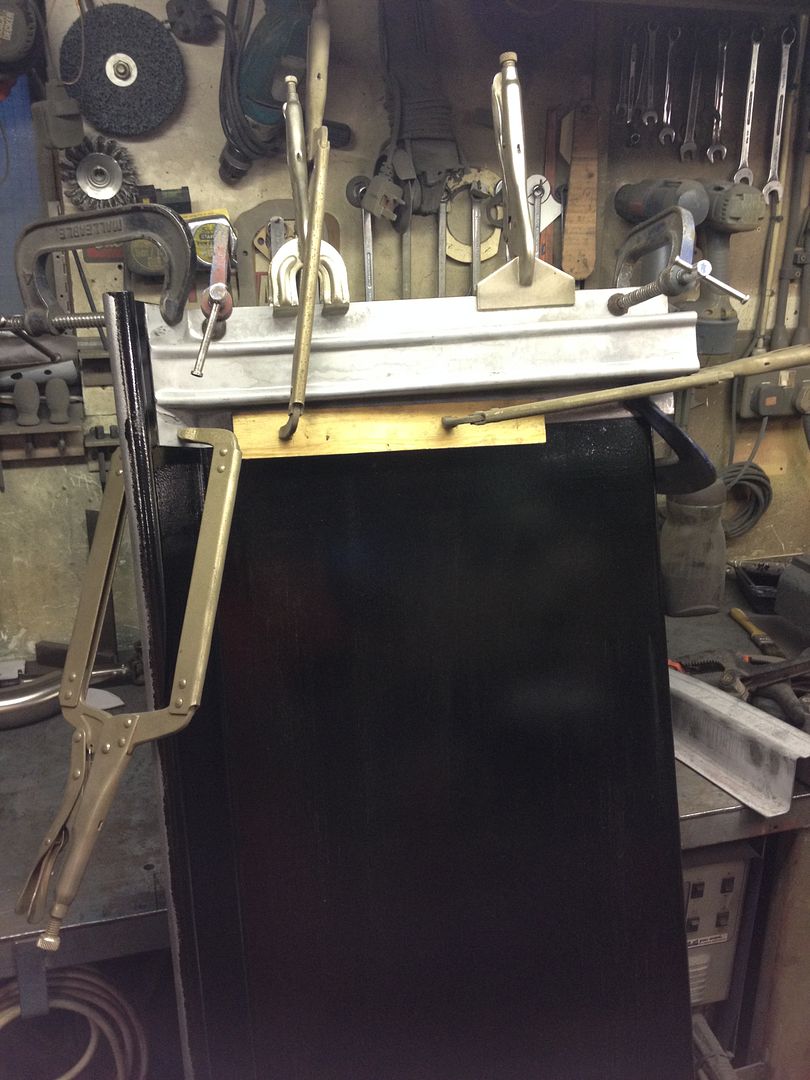
.

First job was to get the tube tacked in place, it was cut longer than needed to allow for somewhere to clamp the ends. Welding 16swg sheet to 16swg tube is always a challenge as the tube tends to bow, Tig was out of the question due to the heat involved so we both decided to Mig and quench each weld as we danced around the joint.
We tacked it every 10" while checking with a straightedge first
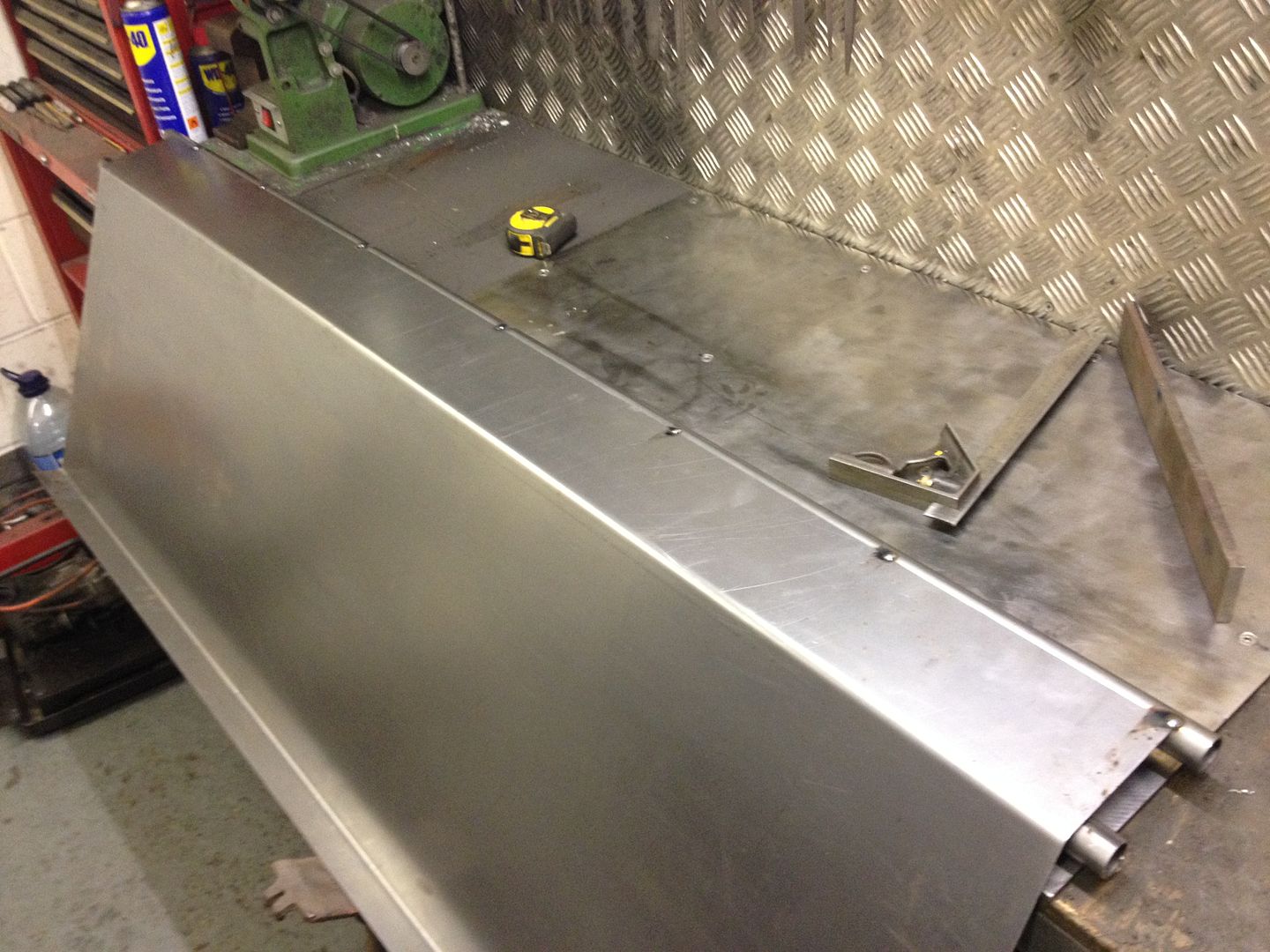
Then clamped it to a piece of 2" x "2 box section, we were both convinced if we laid down 1/4" welds by dancing around in lots of different places and quenching with a damp cloth as quickly as possible every thing would be fine

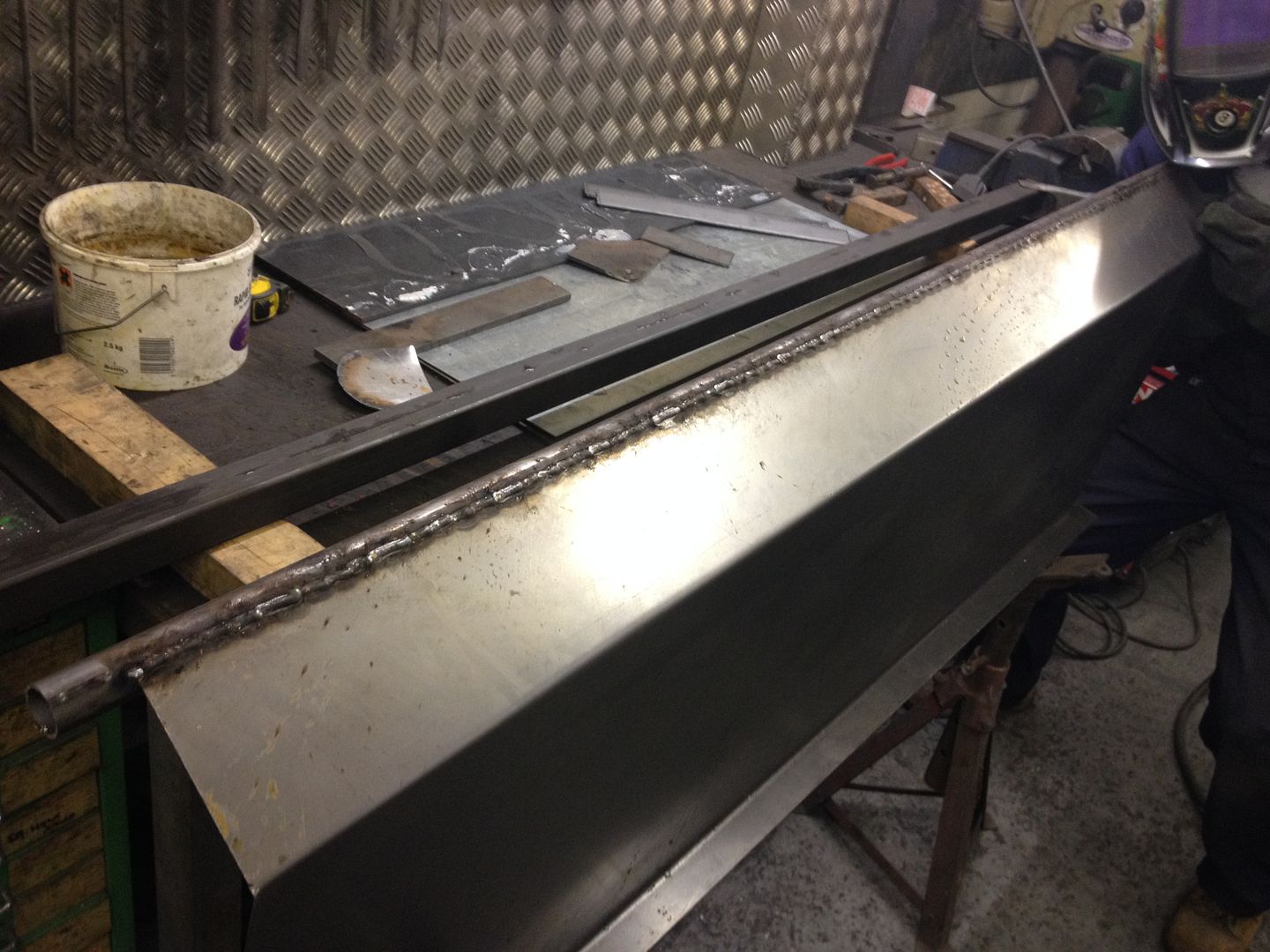
We decided on the other side to try and predict the bow by using a 1/4" packer in the centre and 1/8" outers and only clamp at the middle & ends, we used the same welding & quenching procedure, result was it came out perfectly straight when unclamped

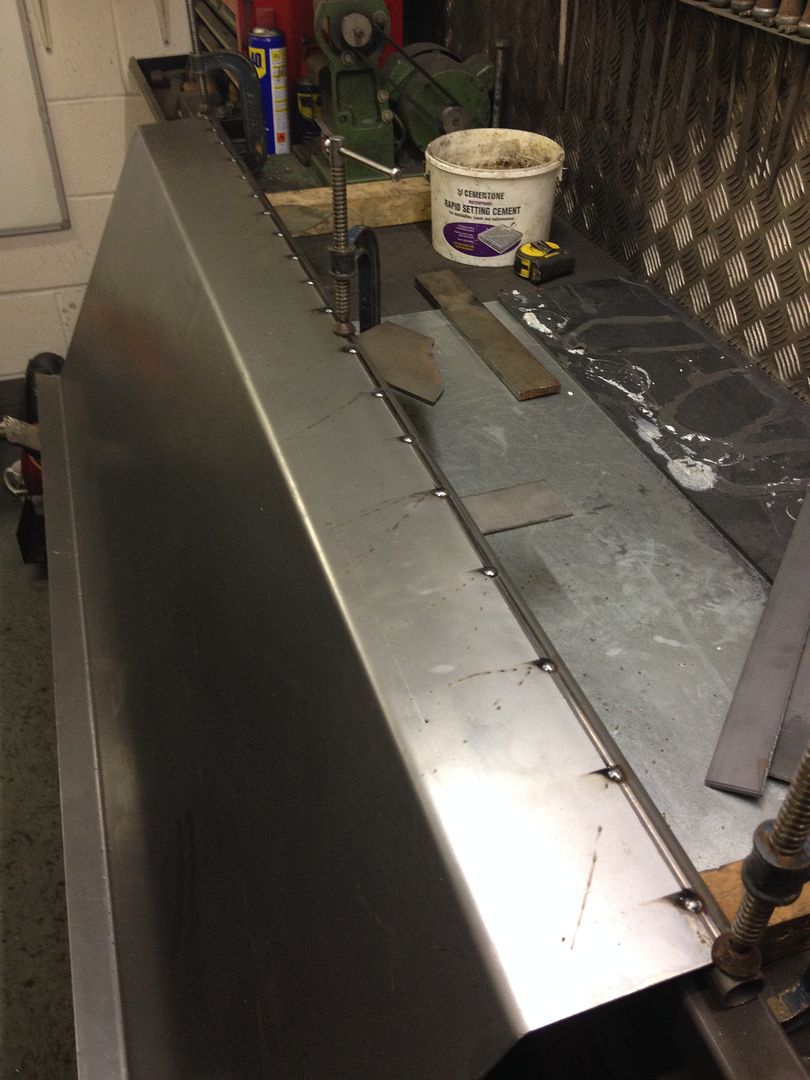
Next job was to sand down the welds and metal finish it all.
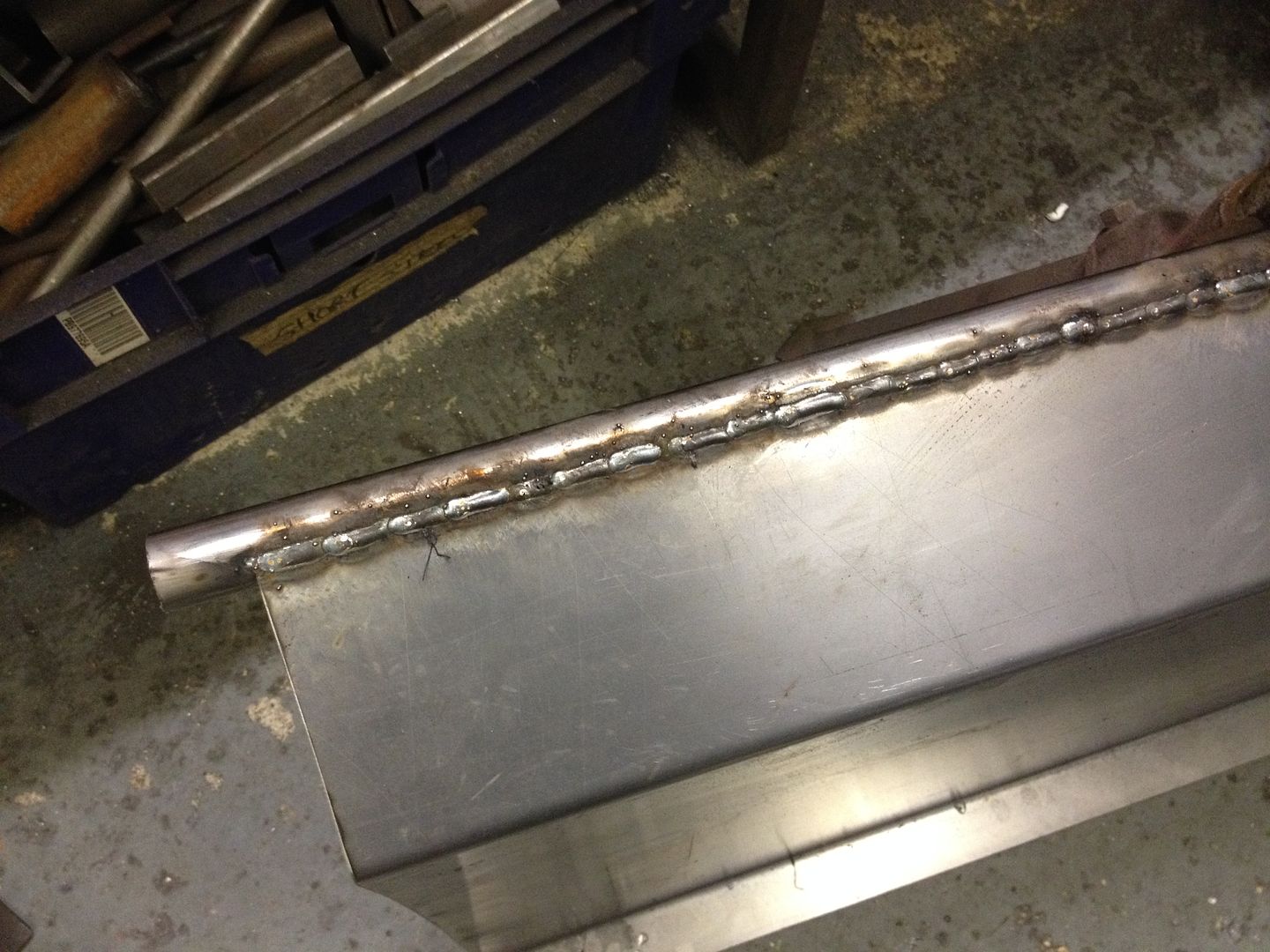
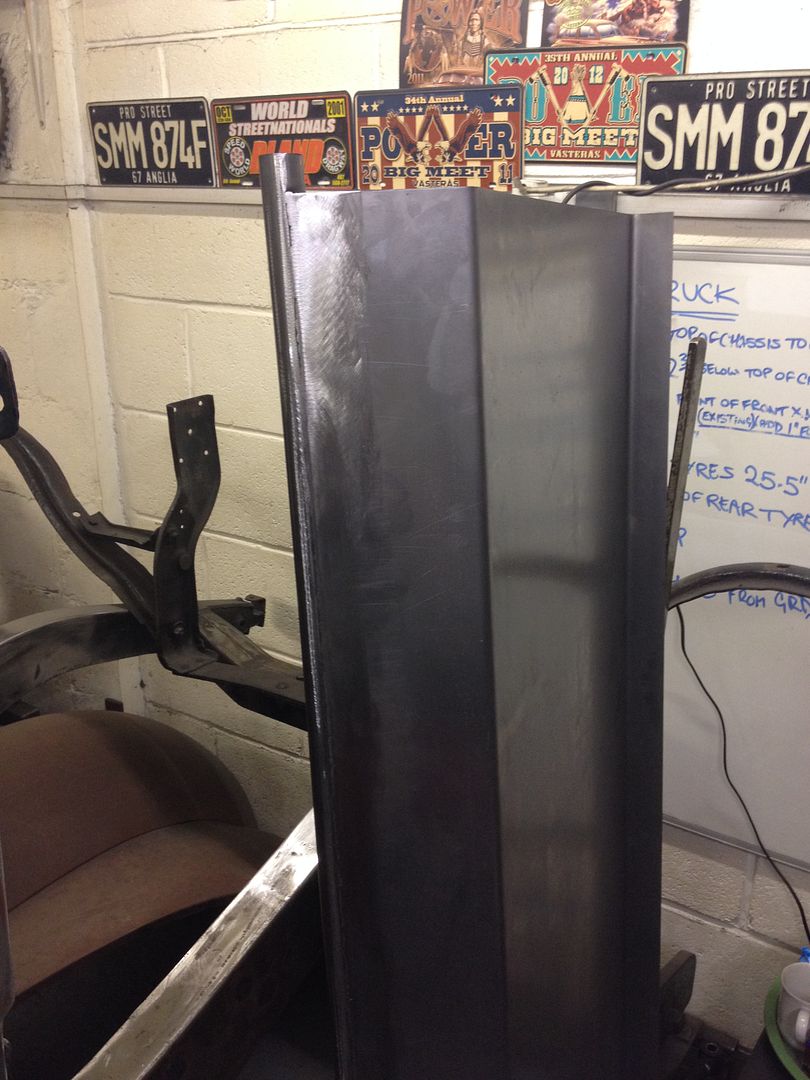
Heres the bowed side and below the straight side
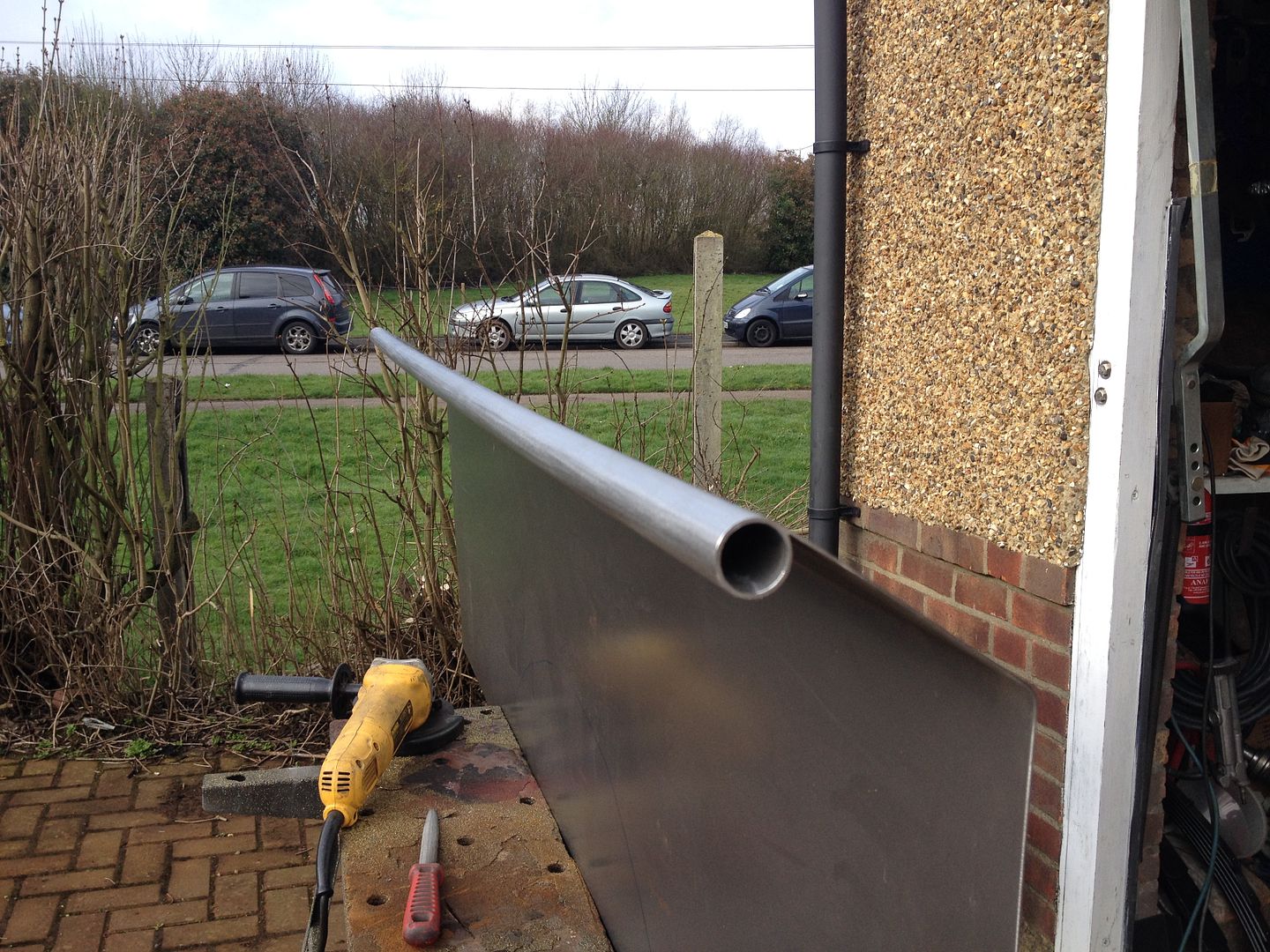
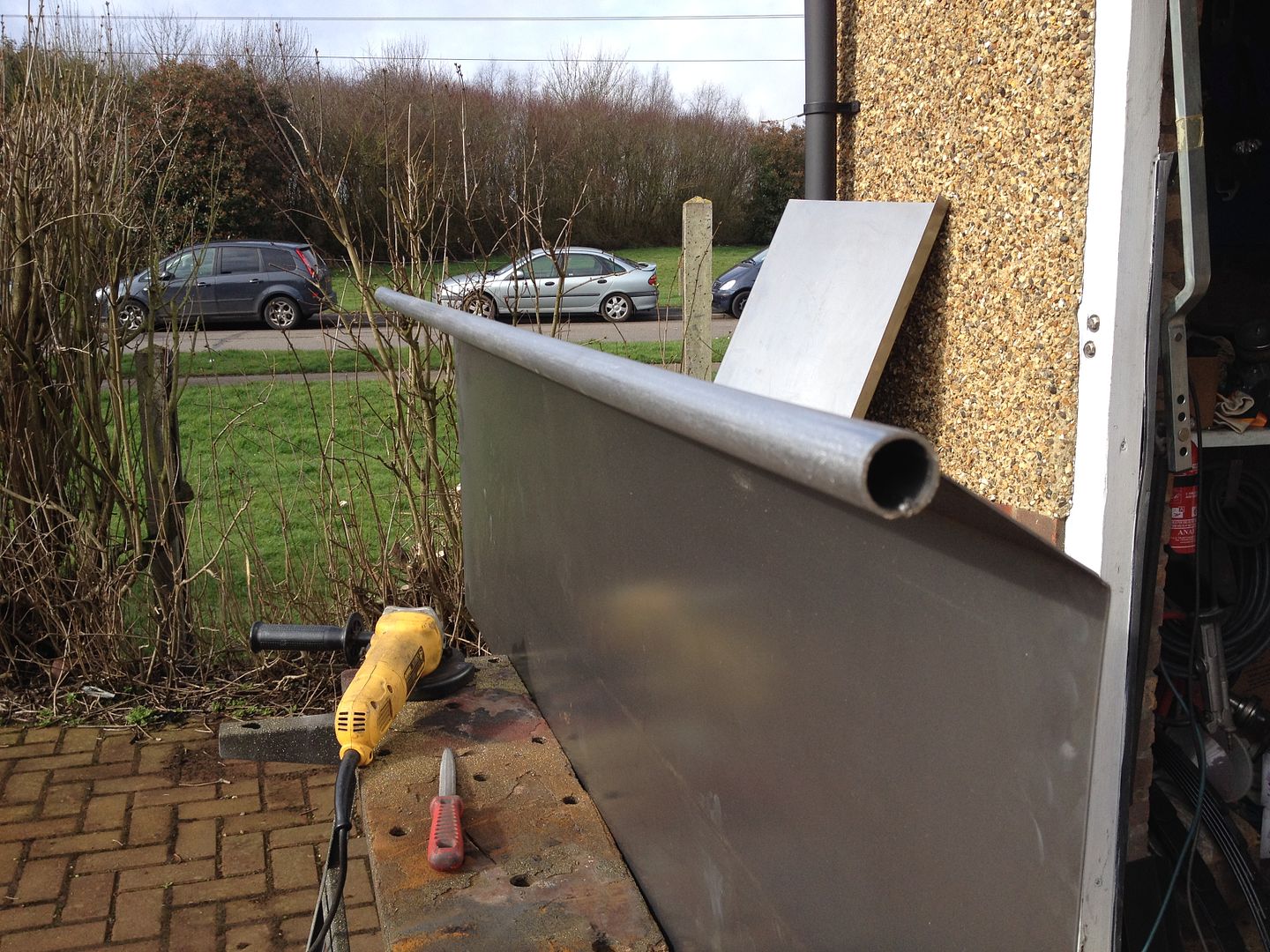
Here they are all metal finished and ready for the stake pockets to be welded on.
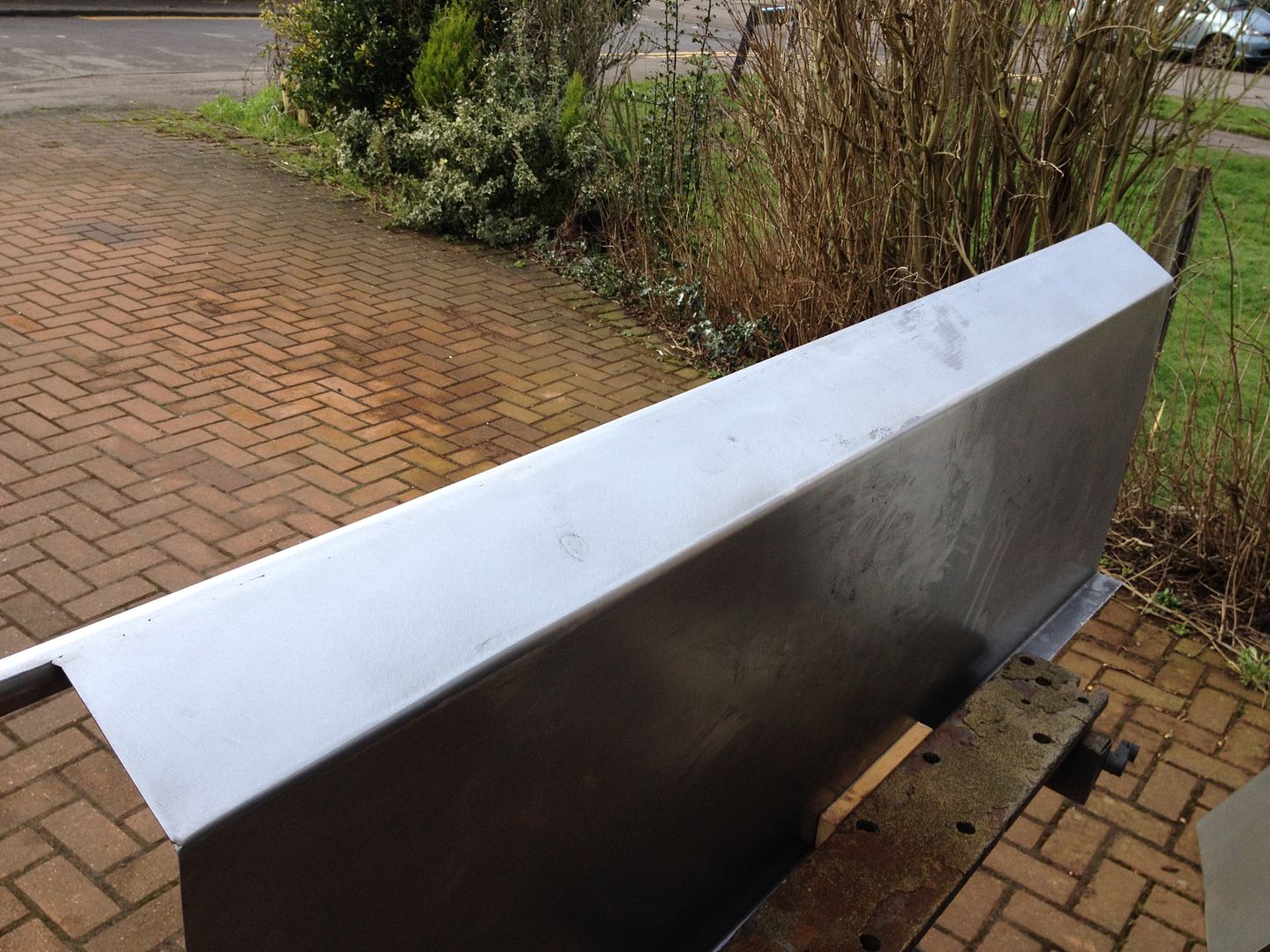
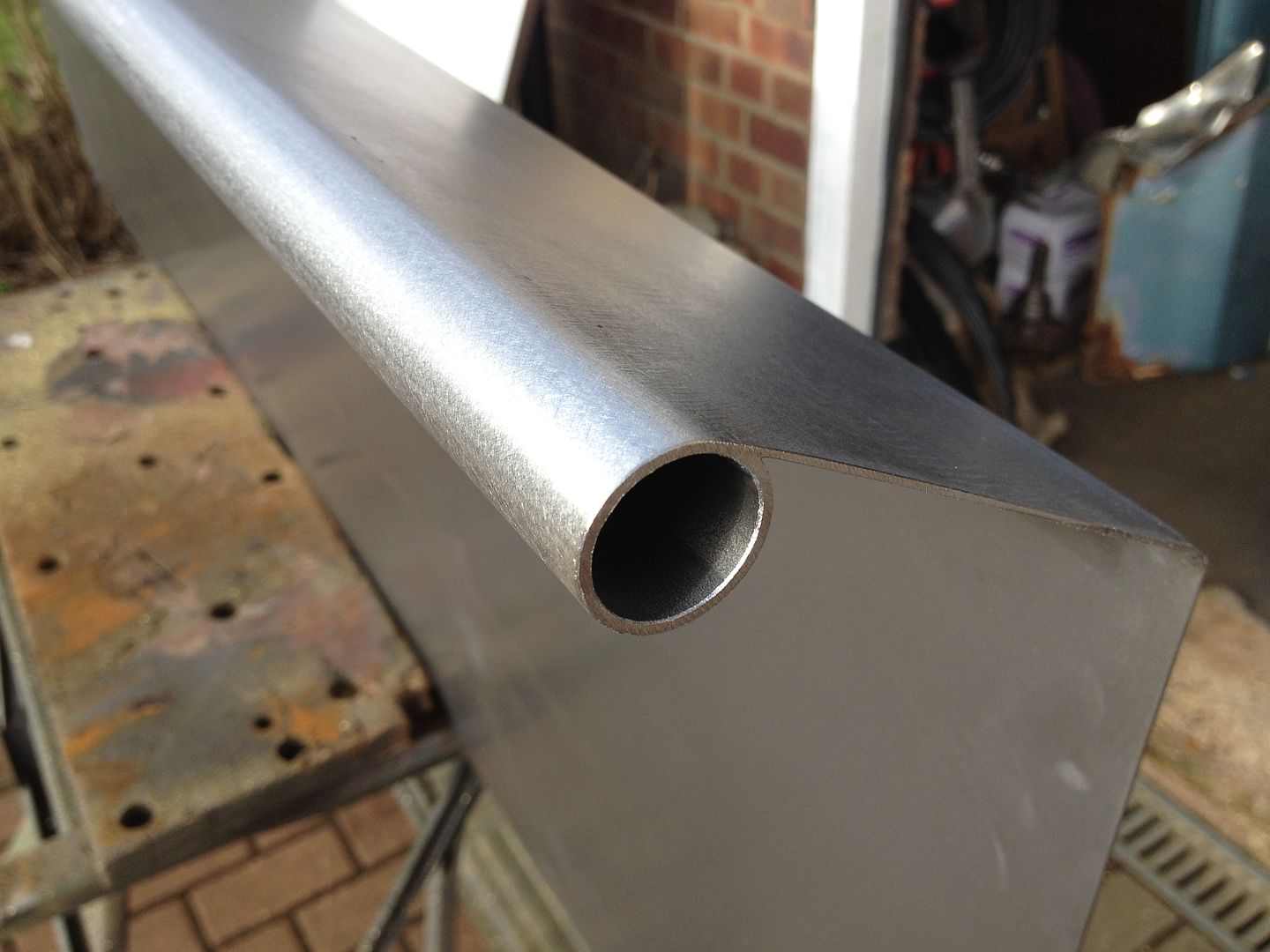
Next job was to mark out and drill the holes so the pockets could be plug welded in place

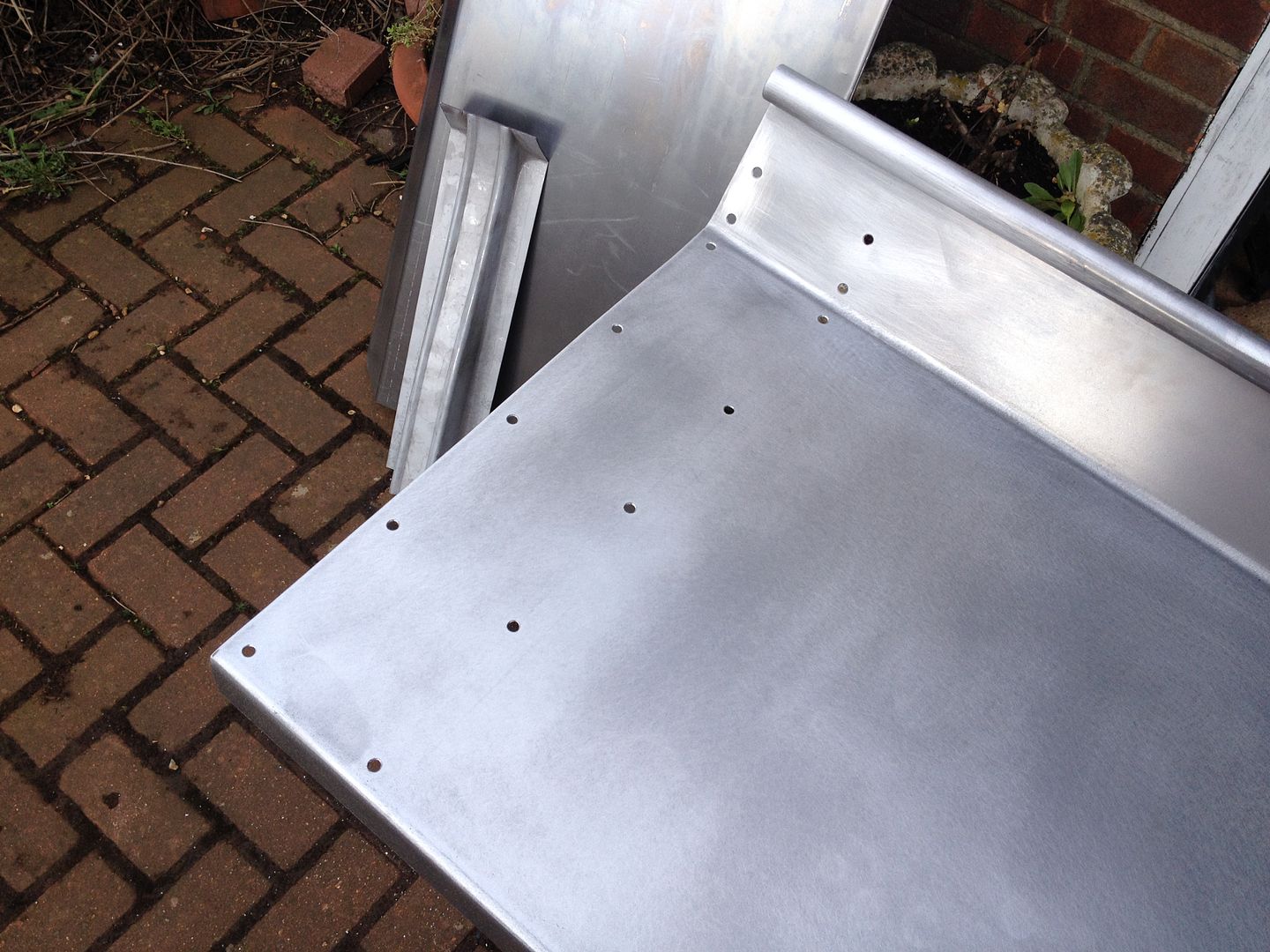
To protect in between the seams 3 coats of Epoxy primer were applied. then the pockets were clamped in place, and thats as far as it got until next time.
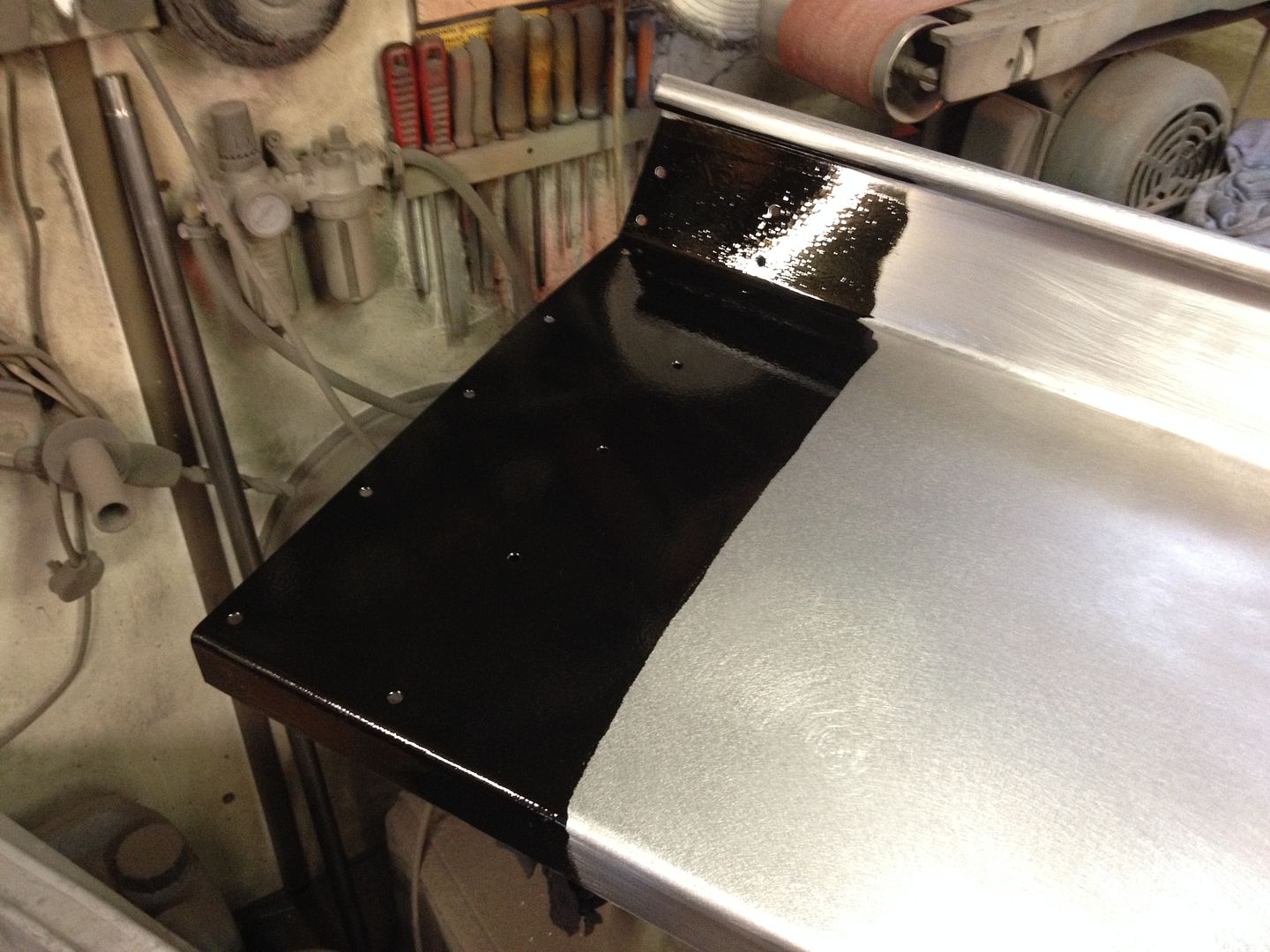
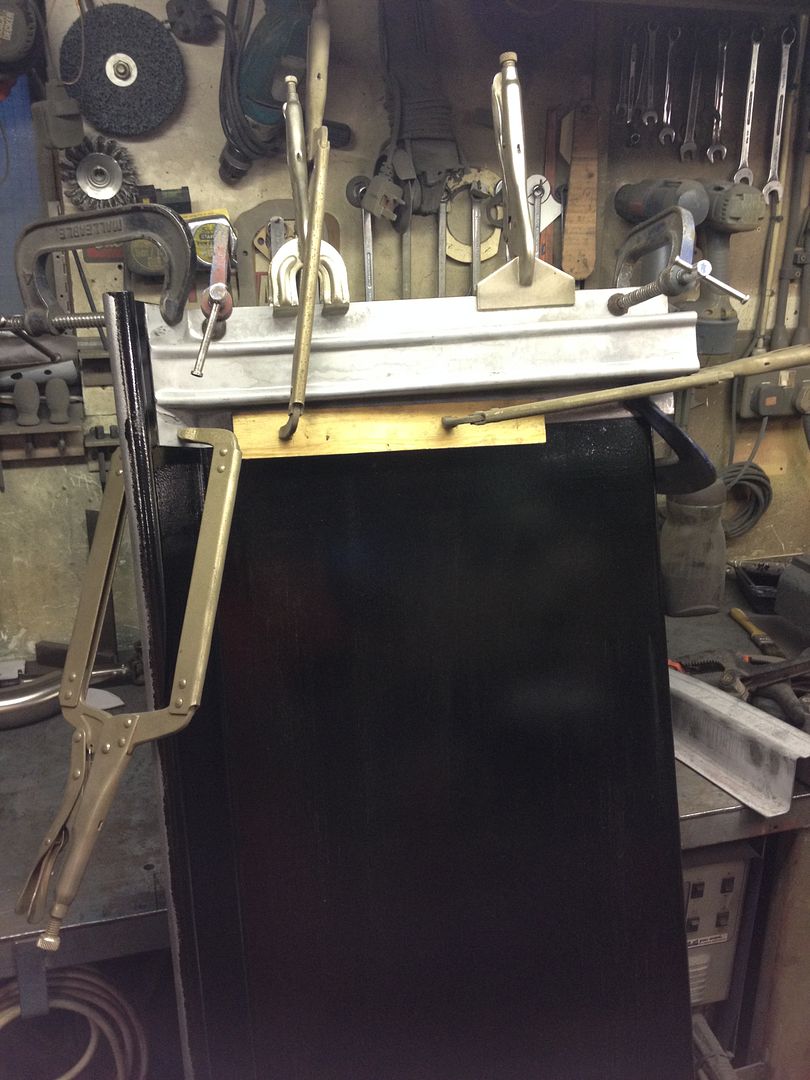
.