jpmillermatic
Member
- Messages
- 1,094
So a bit more done on the inner fender lip. I learned a lot about what I can get away with reasonably with the shrinker/stretcher......
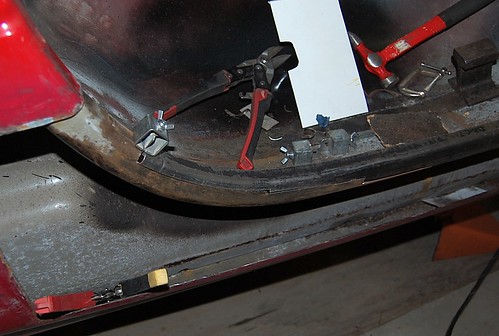
I know I could do this a faster way, but really want to experience actually shaping metal as opposed to patchworking things together. I probably found a somewhat happy medium this time around....there will be small patches to fill in some gaps....
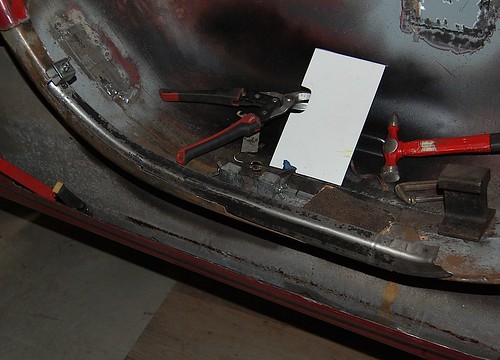
Its coming together and fits nicely. I will have to do a little light tapping here and there once its welded in!

I made a template from thin aluminum. (which you can see in the photos above) It is really hard to know where the outer fender will fit once this is all in place. measuring works okay, but I have to keep going back and forth a million times with the outer panel...it was getting tiring!....so I found that this template locates the flange along the inner profile...my repair piece fits (is shaped) inside the the outer patch panel, so I should be in good shape. (as long as my indexing marks dont disappear!)
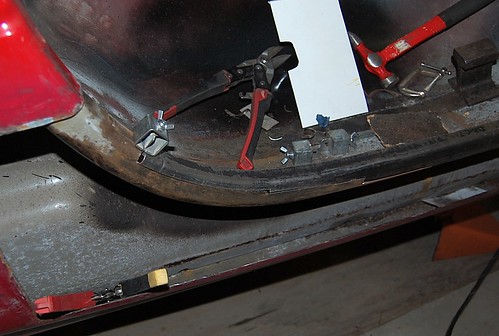
I know I could do this a faster way, but really want to experience actually shaping metal as opposed to patchworking things together. I probably found a somewhat happy medium this time around....there will be small patches to fill in some gaps....
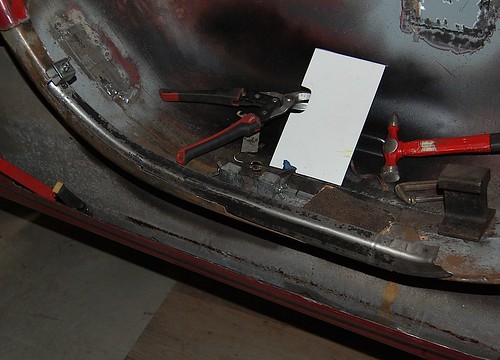
Its coming together and fits nicely. I will have to do a little light tapping here and there once its welded in!

I made a template from thin aluminum. (which you can see in the photos above) It is really hard to know where the outer fender will fit once this is all in place. measuring works okay, but I have to keep going back and forth a million times with the outer panel...it was getting tiring!....so I found that this template locates the flange along the inner profile...my repair piece fits (is shaped) inside the the outer patch panel, so I should be in good shape. (as long as my indexing marks dont disappear!)