smoggyrich
Member
- Messages
- 144
I've been out there again this morning . I had a poke about and decided to bite the bullet and cut out a bit more rot.
I cut a new plate to fit then tacked it in place.
Then i went round doing 4 or 5 tacks in a row allowing them to melt into each other then moving to a different area and doing the same until there was a full weld all the way around.
Here goes.......
I feel that i'm starting to get some where with it now and i'm much happier with the penetration i'm achieving now without blowing through.
What do you think?
(still using gasless by the way)
I cut a new plate to fit then tacked it in place.
Then i went round doing 4 or 5 tacks in a row allowing them to melt into each other then moving to a different area and doing the same until there was a full weld all the way around.
Here goes.......
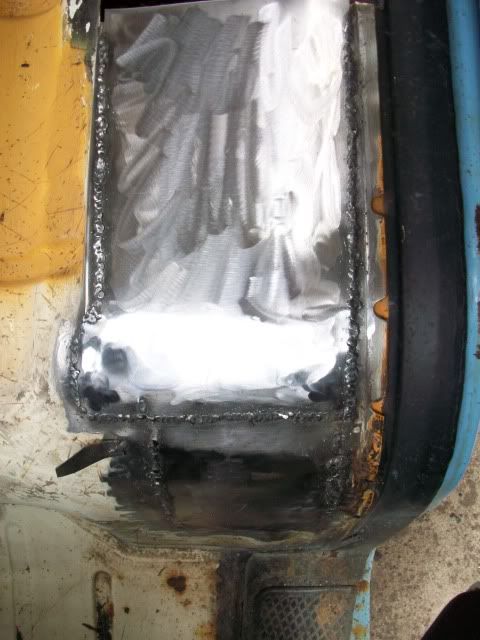
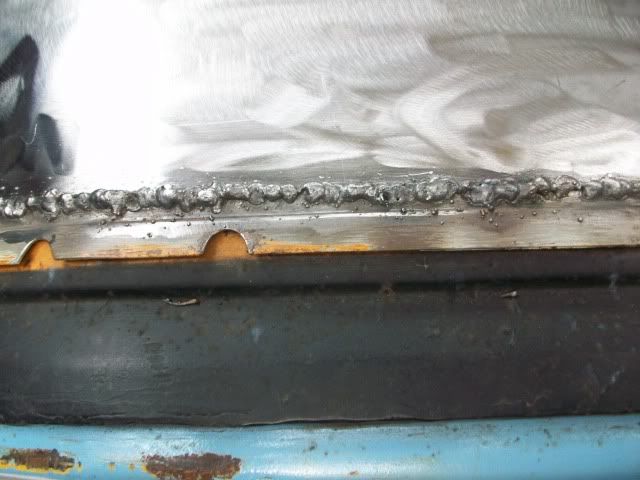
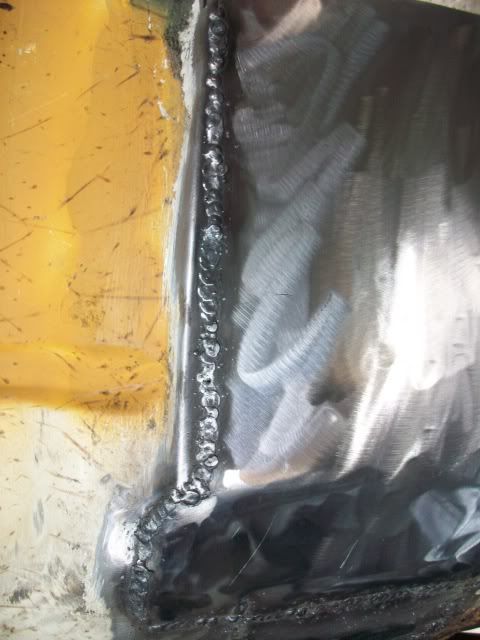
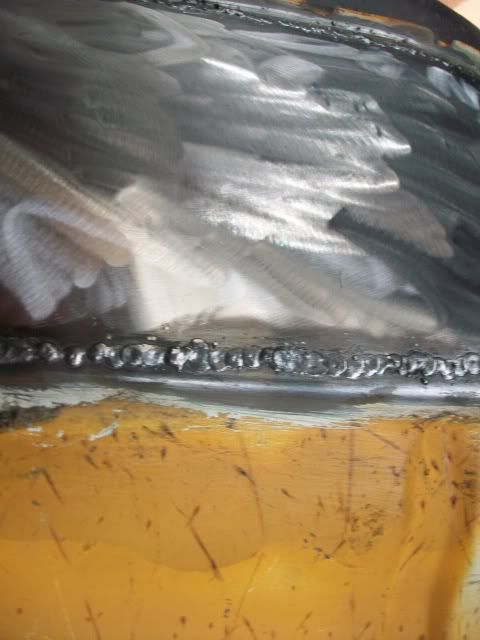
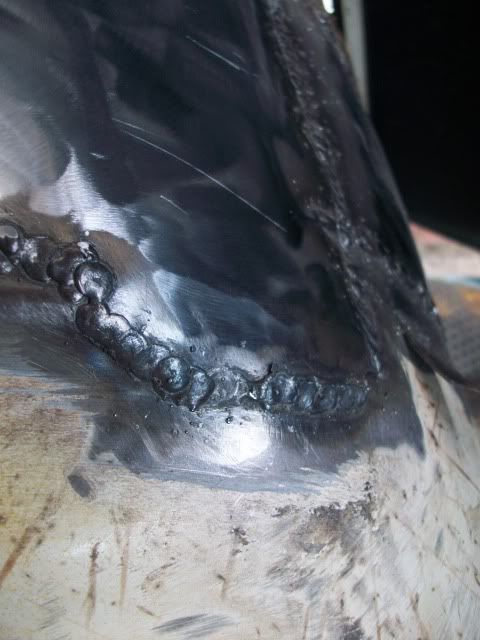
I feel that i'm starting to get some where with it now and i'm much happier with the penetration i'm achieving now without blowing through.
What do you think?
(still using gasless by the way)