I recently posted in the "today I made thread", having gotten back to that project - adding removable cable tidy hooks to my platform trolley - I've decided to share a few photos I took today. As a bit of a cautionary tale to others I'll also share an accident I had today.
Here you can see how the frame I constructed looks in relation to the platform trolley with the welder in position. Once finished, I'll be bolting on large hooks to the front of this frame to hang my power cable up out of the way for my welding machine and maybe my return lead. The hooks are to be removable so I can still fold the trolley flat when I need to transport it.
Some close up pictures of the welds. I've only every ran a coupe of lines of flux core on a flat piece of metal before, so this is really my first attempt. I had a few problems keeping the "bead" where I wanted and occasionally had too much stick out, I'm sure I'll improve with more practice.
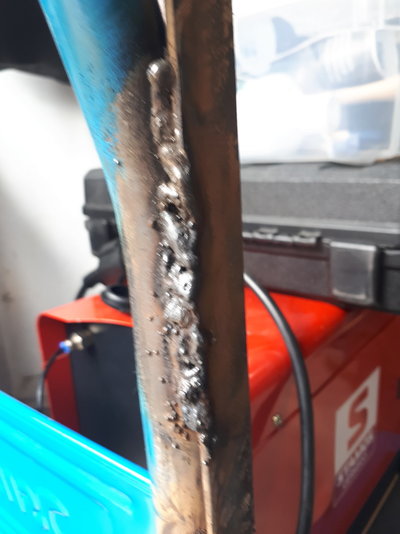
I was given the small disposable gas bottle; not sure if there is anything in it. I've hooked it up, but won't be using it, until I purchase a cylinder in addition as I didn't want to change out the wire just for a very small amount of gas.
The settings I used are reflected in the photo below; I got guidance from this websites calculator and also the Miller welding calculator, and dialed back every so slightly from what was suggested as this wire from Machine Mart seems to "run hot".
Now for the bad news.
I decided to try out one of my new flap discs - having never used one before - on smoothing out the welds and removing a bit more paint, so I can then place some welds on the front of the frame before drilling out some holes and applying some primer.
Despite the heat; having already damaged clothes with sparks the last time I didn't bother, I put on my FR overalls, hearing protection, googles and face shield... and perhaps because a press stud was broken on one of my sleeves - forcing me to roll it up some - I opted to not wear my cut resistant gloves, which I usually wear when grinding or handling materials.
Having never used a flap disc before, and having seen many videos on YouTube of them being used without a guard, that is the option I went for; so I removed the grinding guard on my Clarke angle grinder, fitted the flap disc and got started on cleaning up the previous welds.
Very soon into that process I cut myself from the flap disc in my left hand (I'm right handed) and realised; being used to using an angle grinder with the guard, my supporting left hand must have crept up the handle and allowed part of my hand to come into contact with the fast moving flap disc.
I adjusted my grip and got back to work, soon after, it happened... my new flap disc tore into my hand causing a significant cut, I straight away put the tool down and got dropped off at A&E.
Lessons learned: 1. Having been cut, I should have taken that as a warning and changed more of what I was doing, not just adjusted my hand position. 2. If I replaced then side handle after I removed it when working in a confined space, this probably wouldn't have happened. 3. If I worked with the guard on this probably wouldn't have happened.
How do people feel about wearing gloves with handheld angle grinders? I normally do, but wasn't sure it was appropriate, as I've heard you shouldn't wear gloves with spinning equipment.
Here you can see how the frame I constructed looks in relation to the platform trolley with the welder in position. Once finished, I'll be bolting on large hooks to the front of this frame to hang my power cable up out of the way for my welding machine and maybe my return lead. The hooks are to be removable so I can still fold the trolley flat when I need to transport it.
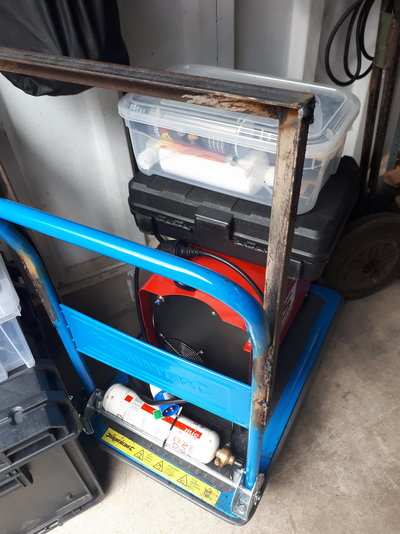
Some close up pictures of the welds. I've only every ran a coupe of lines of flux core on a flat piece of metal before, so this is really my first attempt. I had a few problems keeping the "bead" where I wanted and occasionally had too much stick out, I'm sure I'll improve with more practice.
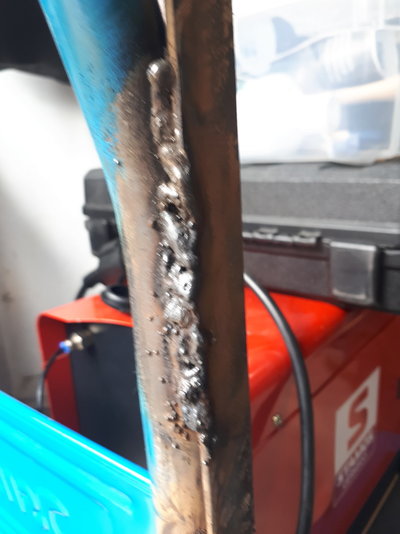
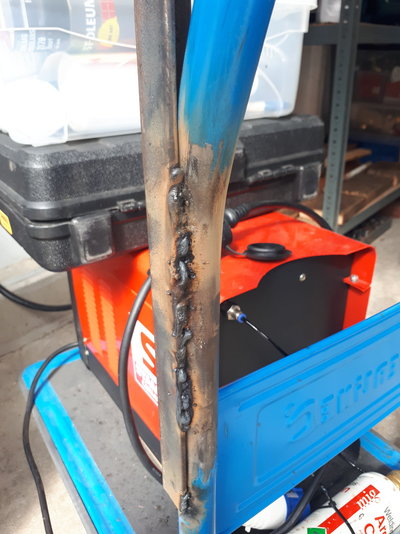
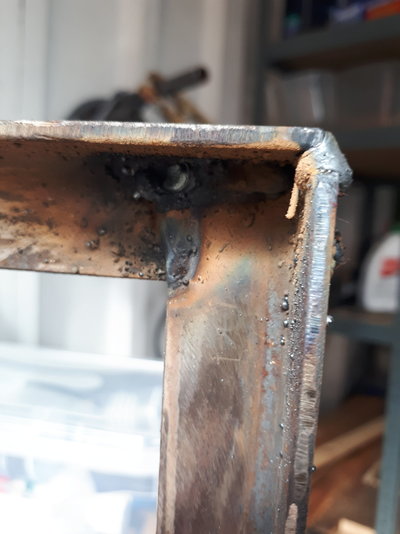
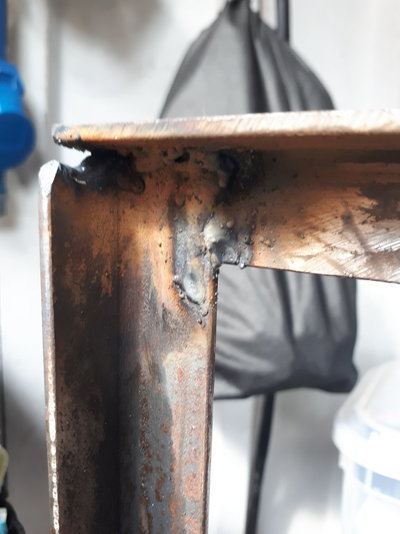
I was given the small disposable gas bottle; not sure if there is anything in it. I've hooked it up, but won't be using it, until I purchase a cylinder in addition as I didn't want to change out the wire just for a very small amount of gas.
The settings I used are reflected in the photo below; I got guidance from this websites calculator and also the Miller welding calculator, and dialed back every so slightly from what was suggested as this wire from Machine Mart seems to "run hot".
Now for the bad news.
I decided to try out one of my new flap discs - having never used one before - on smoothing out the welds and removing a bit more paint, so I can then place some welds on the front of the frame before drilling out some holes and applying some primer.
Despite the heat; having already damaged clothes with sparks the last time I didn't bother, I put on my FR overalls, hearing protection, googles and face shield... and perhaps because a press stud was broken on one of my sleeves - forcing me to roll it up some - I opted to not wear my cut resistant gloves, which I usually wear when grinding or handling materials.
Having never used a flap disc before, and having seen many videos on YouTube of them being used without a guard, that is the option I went for; so I removed the grinding guard on my Clarke angle grinder, fitted the flap disc and got started on cleaning up the previous welds.
Very soon into that process I cut myself from the flap disc in my left hand (I'm right handed) and realised; being used to using an angle grinder with the guard, my supporting left hand must have crept up the handle and allowed part of my hand to come into contact with the fast moving flap disc.
I adjusted my grip and got back to work, soon after, it happened... my new flap disc tore into my hand causing a significant cut, I straight away put the tool down and got dropped off at A&E.
Lessons learned: 1. Having been cut, I should have taken that as a warning and changed more of what I was doing, not just adjusted my hand position. 2. If I replaced then side handle after I removed it when working in a confined space, this probably wouldn't have happened. 3. If I worked with the guard on this probably wouldn't have happened.
How do people feel about wearing gloves with handheld angle grinders? I normally do, but wasn't sure it was appropriate, as I've heard you shouldn't wear gloves with spinning equipment.