Munkul
Jack of some trades, Master of none
- Messages
- 7,371
- Location
- Cumbria
We've been busy over the BH weekend! Our new workshop, that is, myself, brother and cousin's, has went from this:
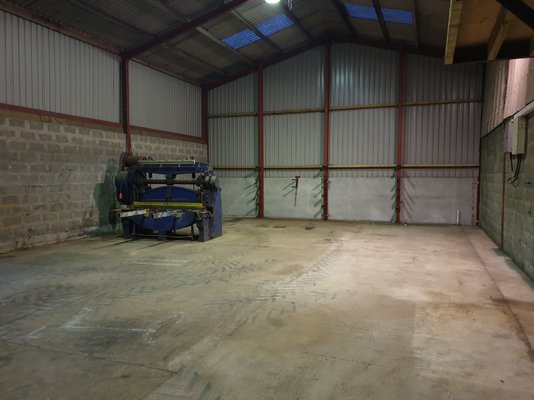
...To this:
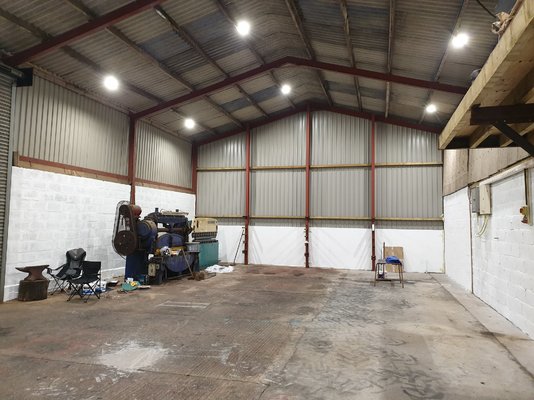
The lighting went from 4 off 80W conventional floods with about half a candlepower, to 12 off 50w LED floods, they are actually almost TOO bright, the single centre row is enough for most work! The pictures don't really do it justice, it's literally night and day.
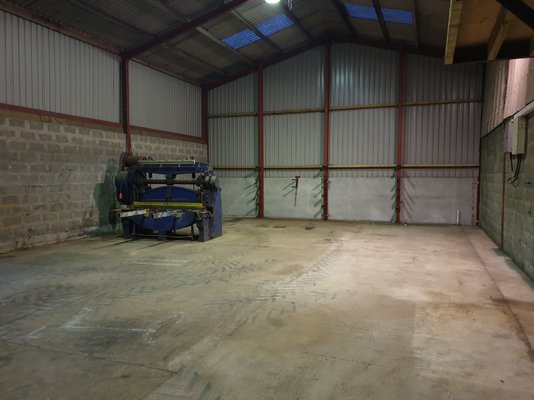
...To this:
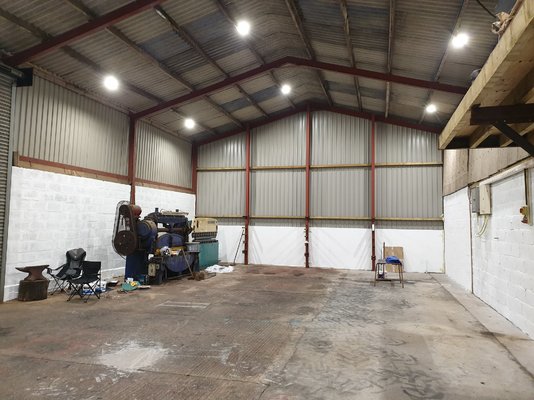
The lighting went from 4 off 80W conventional floods with about half a candlepower, to 12 off 50w LED floods, they are actually almost TOO bright, the single centre row is enough for most work! The pictures don't really do it justice, it's literally night and day.