mylesdw
Member
- Messages
- 794
Getting towards the end of the first side-locker.
I doubled up the top front rail to add stiffness and to lower the hinge-line to clear the body
and added door shuts
It's all 25x25x1.6 Duragal SHS with this primer on the welds
It matches the tubing quite nicely and goes on nice and smoothly
Floor is 25mm treated ply.
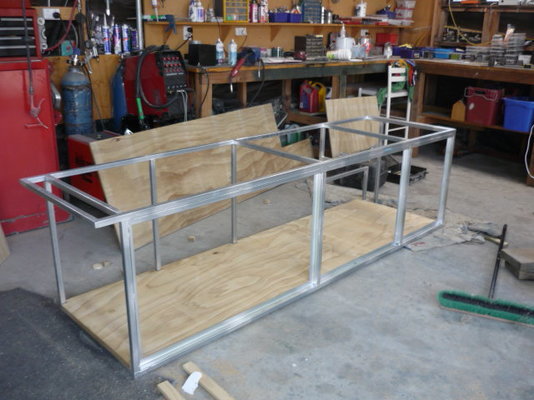
I doubled up the top front rail to add stiffness and to lower the hinge-line to clear the body
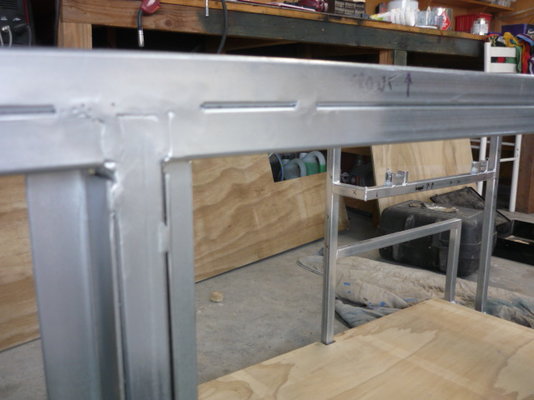
and added door shuts
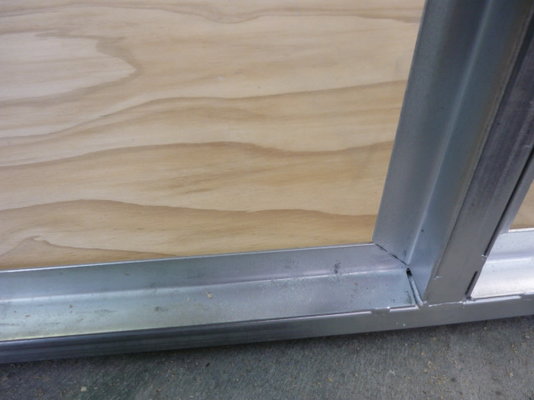
It's all 25x25x1.6 Duragal SHS with this primer on the welds
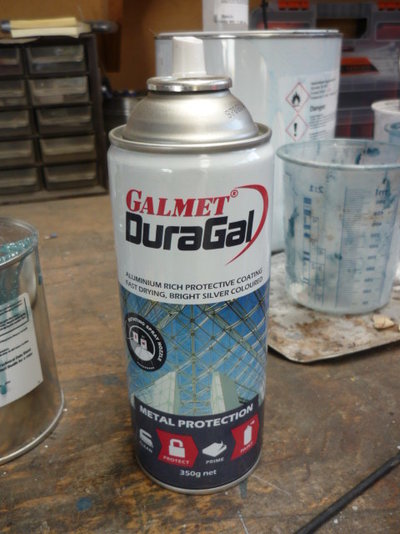
It matches the tubing quite nicely and goes on nice and smoothly
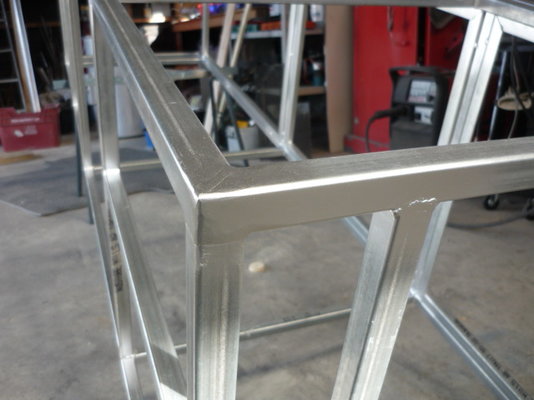
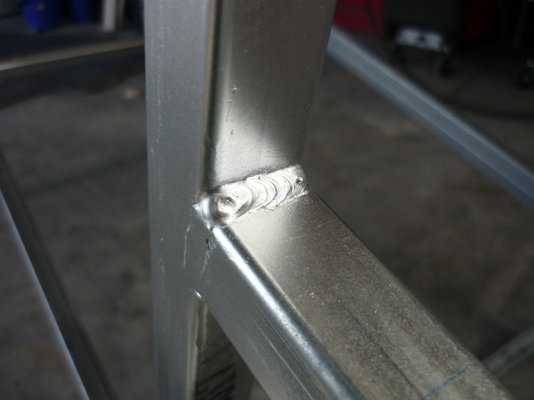
Floor is 25mm treated ply.