Myles1970
Member
- Messages
- 929
- Location
- Monaghan, Ireland
So, €250 lighter....a guy nearby who breaks these cars had an ad on fbook for this:
Straight and rust free, no signs of any repairs.
Test fitted the doors after measuring the openings which were slightly out. The passenger door is 100%, a combination of worn hinge and possible movement on the driver's side means it bangs off the striker but can be lifted closed.
Worth noting that there is still a large hole in the driver's footwell and outrigger not fitted.
When closed the roof is slightly proud of the door (I'll have to recheck that it's the roof that's proud )
Conclusion: the shell needs to be fixed down straight and true so that my repairs from here on don't leave it twisted
Set the wing on for inspiration lol
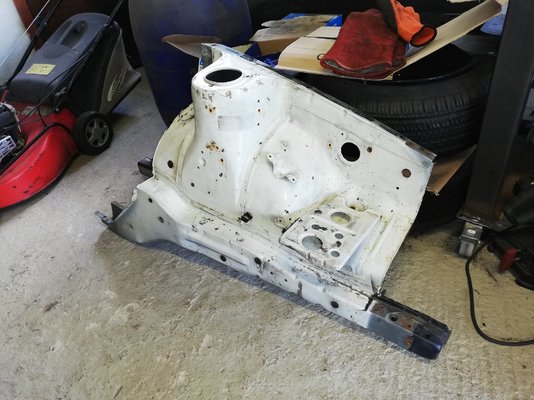
Straight and rust free, no signs of any repairs.
Test fitted the doors after measuring the openings which were slightly out. The passenger door is 100%, a combination of worn hinge and possible movement on the driver's side means it bangs off the striker but can be lifted closed.
Worth noting that there is still a large hole in the driver's footwell and outrigger not fitted.
When closed the roof is slightly proud of the door (I'll have to recheck that it's the roof that's proud )
Conclusion: the shell needs to be fixed down straight and true so that my repairs from here on don't leave it twisted
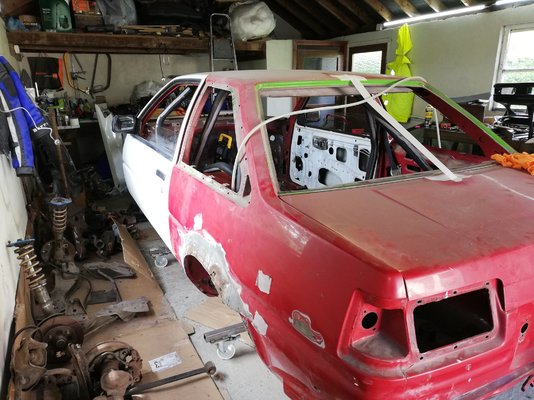
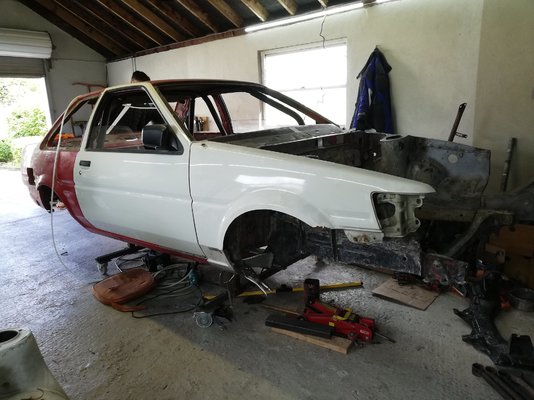
Set the wing on for inspiration lol