Kram
Member
- Messages
- 7,993
- Location
- Sussex
60 degree tool will remove more material than needed, thread will be weaker, but I am using high tensile Im sure it will be fine, I was just very unsure about the numbers above!
Thread depth I was expecting 2.34 on my diamter dials (1.17).
I calculated 21.03mm for a one wire using .98mm drill bit.
Last cut got it to 21.01mm at 2.2mm depth on the dials, test fit screws on perfectly.
Took me all bloody day to make this adaptor, but for 5th threading attempt Im happy.
Thread depth I was expecting 2.34 on my diamter dials (1.17).
I calculated 21.03mm for a one wire using .98mm drill bit.
Last cut got it to 21.01mm at 2.2mm depth on the dials, test fit screws on perfectly.
Took me all bloody day to make this adaptor, but for 5th threading attempt Im happy.
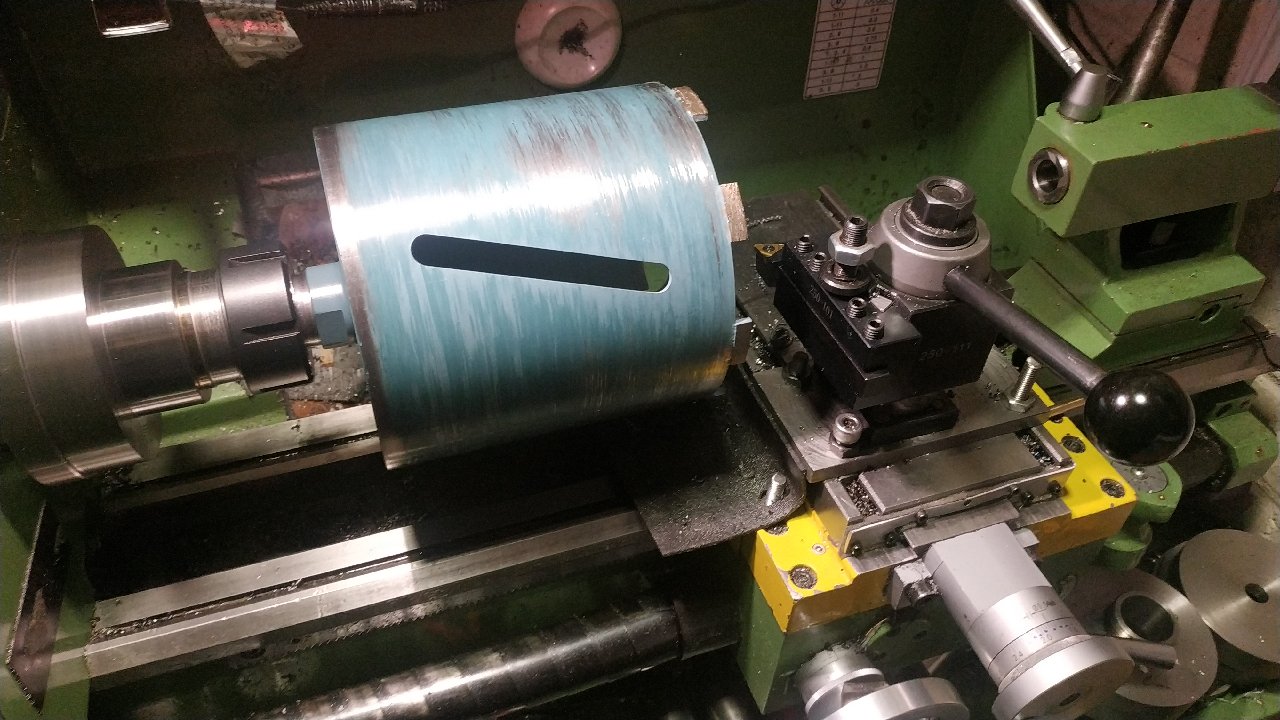