Paul.
Moderator
- Messages
- 7,051
- Location
- Northampton. UK
A bit more sheet metalwork this week, a feed hopper for a piece of food processing machinery, material is 1.5mm stainless steel.
First lay out the pattern, I could have easily developed this out straight on to the sheet, but the jobs likely to come up again so used autocad and printed a paper template, then just used a dot punch to mark through, really could do with a bigger printer though.
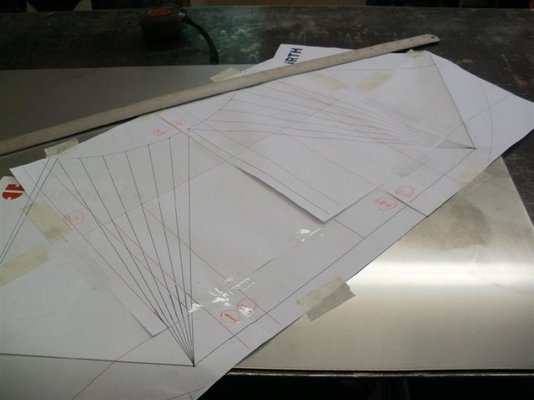
Then cut it out and mark the bend lines in pencil, its also had a rub over with a dual action sander with scotchbrite before I start bending
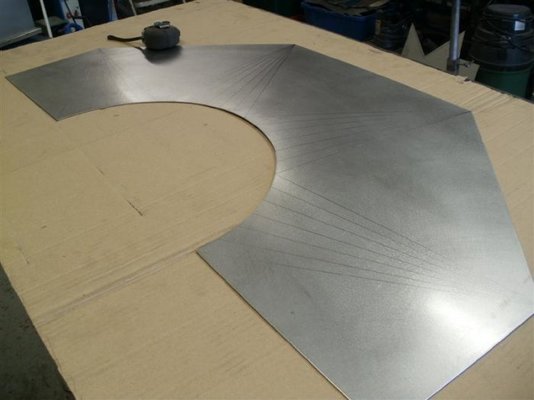
Before bending nick the corners, this will help to make a nice square corner, I'll weld it up later.
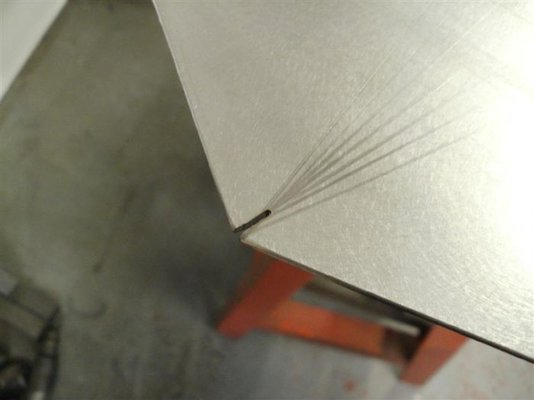
I'm bending this on my self made folder rather than a box and pan or a press, made specially for this type of work, it has a small top beam which means the job will wrap around it therefore only one welded joint is needed.
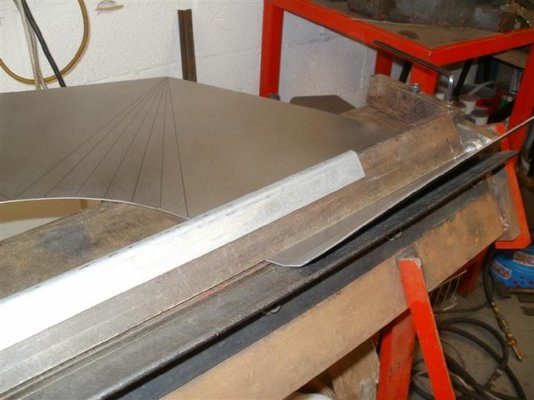
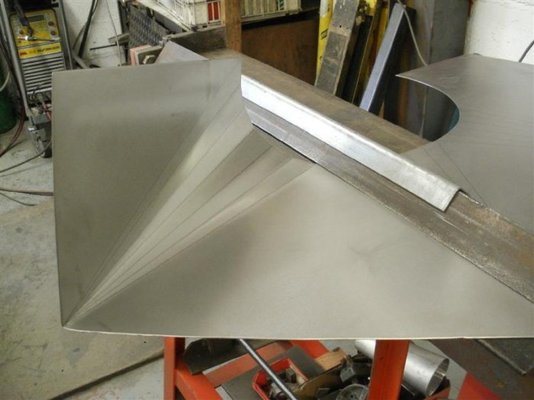
Halfway, time for a check of the radius and a bit of dressing to keep things on track
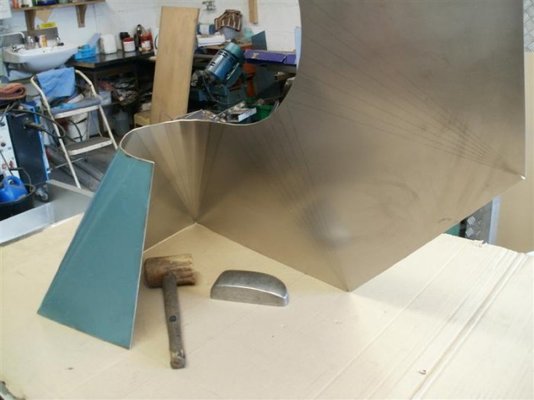
Nearly there, now you can see the benefit of the small folder beam
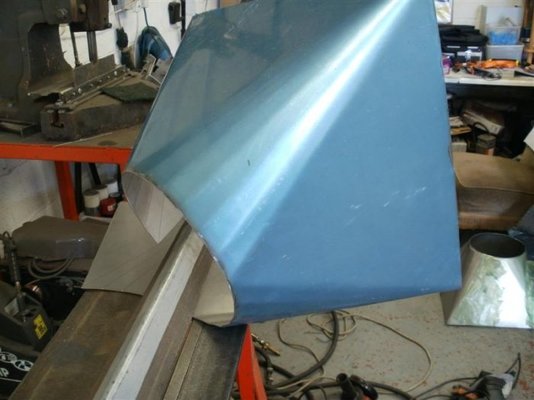
Tacked up
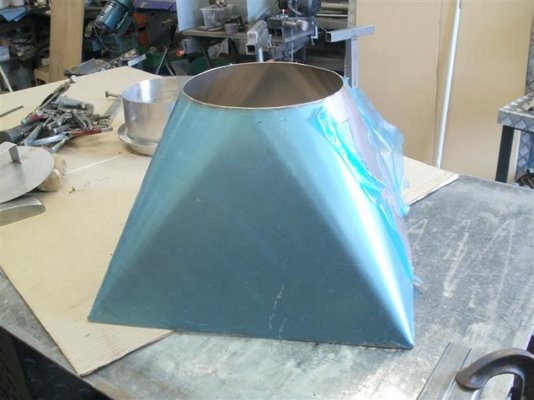
Next fit the spigot, the flange is where it locates into the blending drum that its to be fitted on, the flange is 4mm, I had that laser cut.
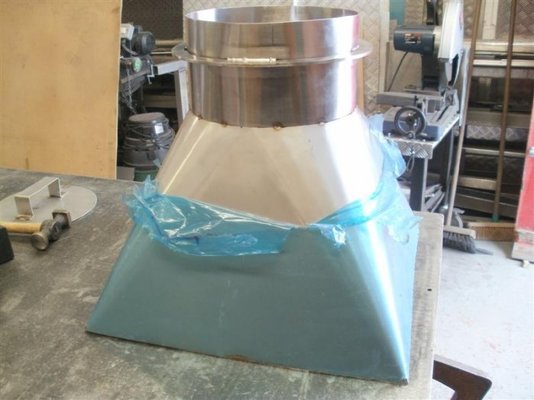
A flange round the top, this is 5mm thick, and has to be welded both sides for hygiene purposes, the pulse tig is really useful here to prevent burn through, and reduce distortion, Its backstep welded as well, and compressed air quenched between runs, I'll round off the corners later.
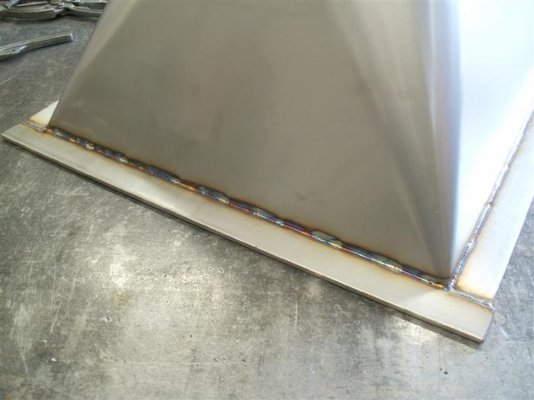
Finished, its just a piece of commercial food equipment, so as long as its clean and presentable on delivery the customer will be happy, the way this stuff gets treated, within a few days it will look like its been in a train crash.
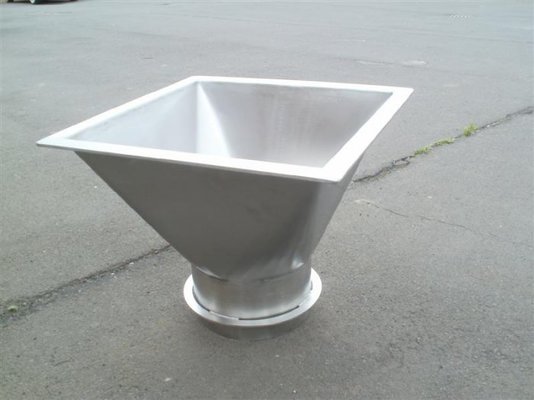
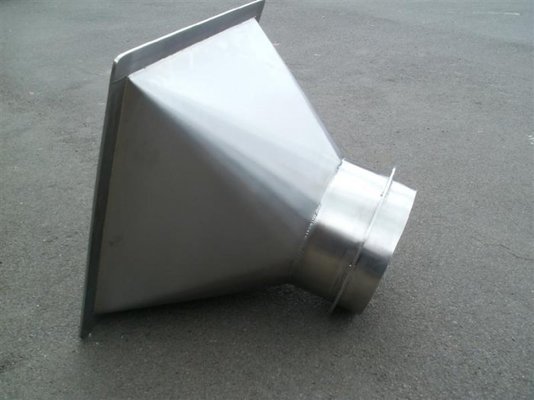
First lay out the pattern, I could have easily developed this out straight on to the sheet, but the jobs likely to come up again so used autocad and printed a paper template, then just used a dot punch to mark through, really could do with a bigger printer though.
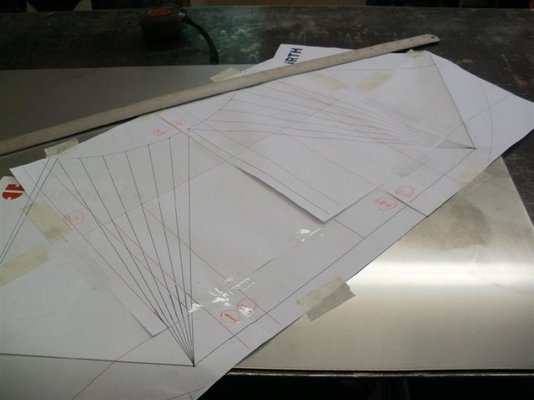
Then cut it out and mark the bend lines in pencil, its also had a rub over with a dual action sander with scotchbrite before I start bending
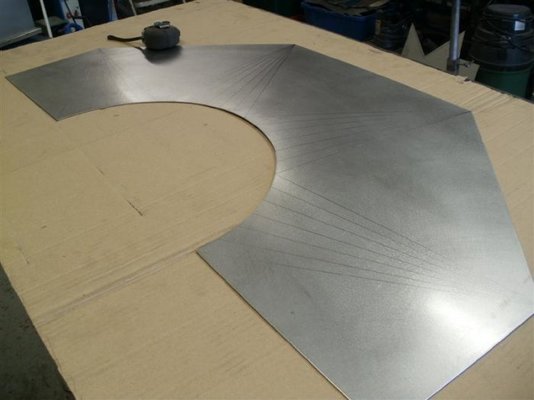
Before bending nick the corners, this will help to make a nice square corner, I'll weld it up later.
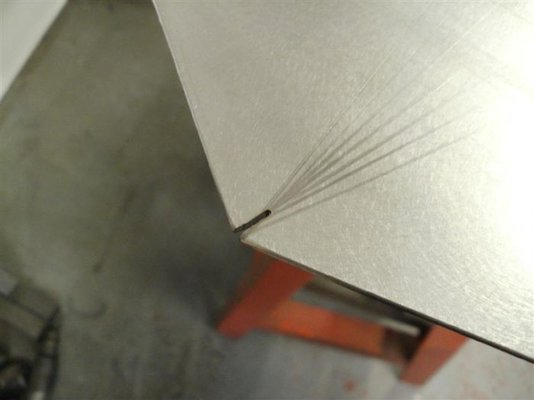
I'm bending this on my self made folder rather than a box and pan or a press, made specially for this type of work, it has a small top beam which means the job will wrap around it therefore only one welded joint is needed.
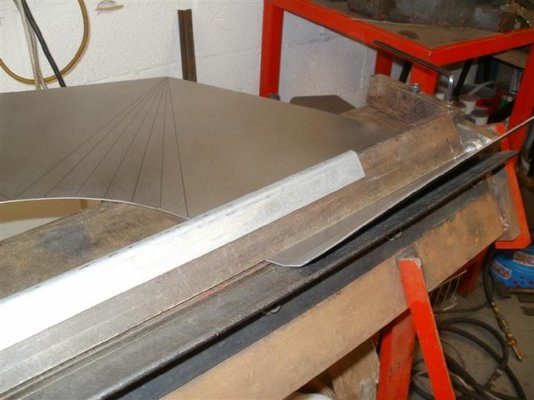
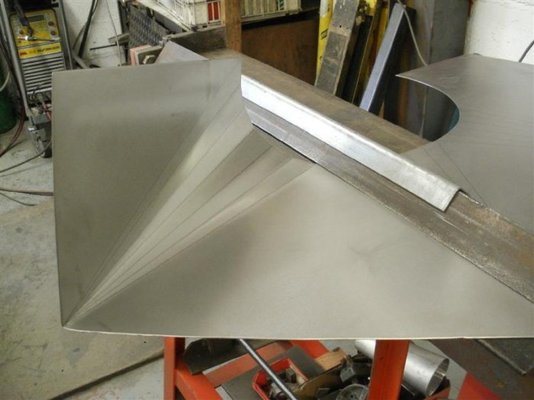
Halfway, time for a check of the radius and a bit of dressing to keep things on track
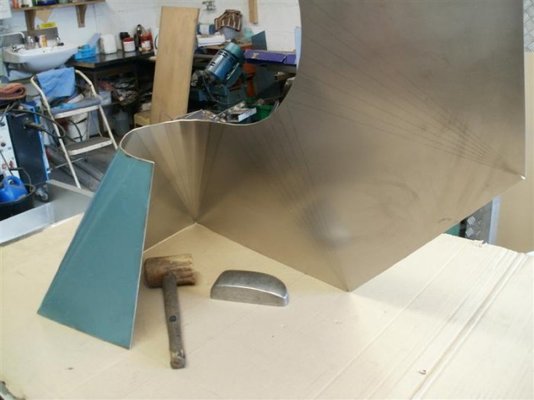
Nearly there, now you can see the benefit of the small folder beam
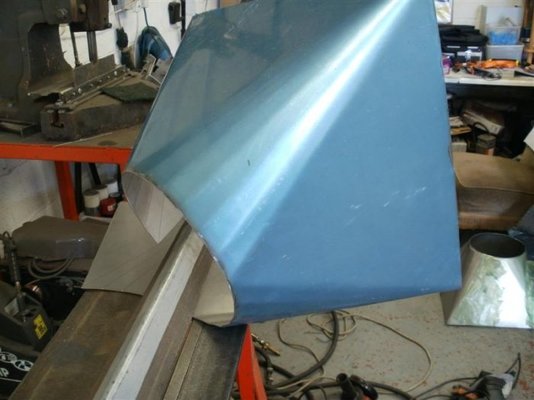
Tacked up
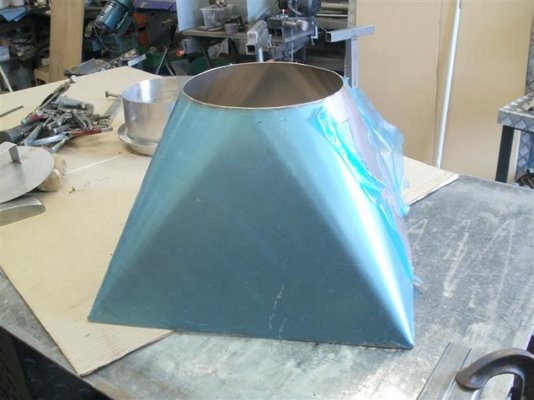
Next fit the spigot, the flange is where it locates into the blending drum that its to be fitted on, the flange is 4mm, I had that laser cut.
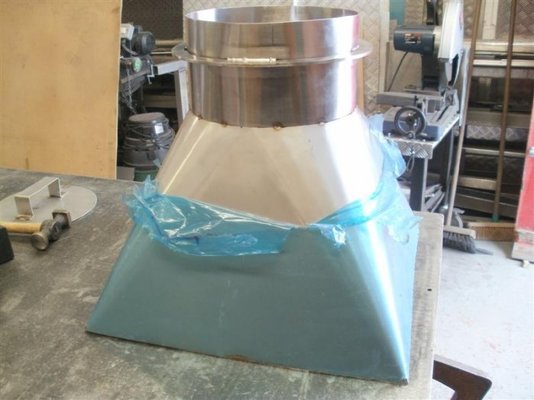
A flange round the top, this is 5mm thick, and has to be welded both sides for hygiene purposes, the pulse tig is really useful here to prevent burn through, and reduce distortion, Its backstep welded as well, and compressed air quenched between runs, I'll round off the corners later.
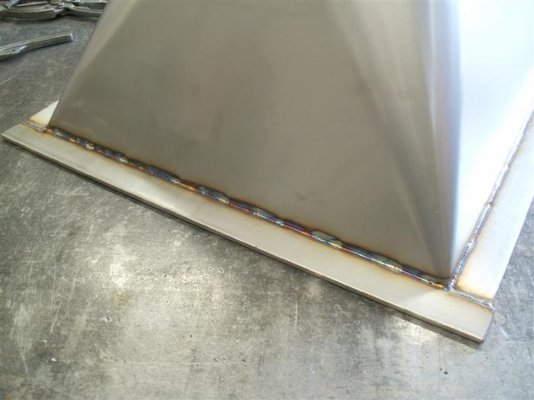
Finished, its just a piece of commercial food equipment, so as long as its clean and presentable on delivery the customer will be happy, the way this stuff gets treated, within a few days it will look like its been in a train crash.
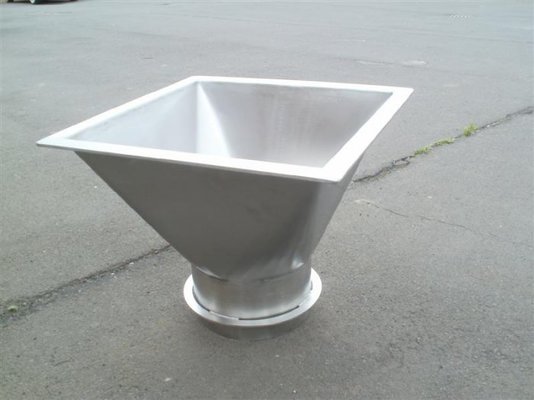
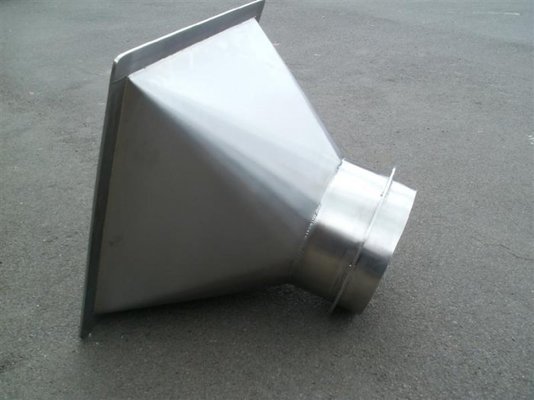