last year I decided that I wanted to build a small scale steam plant for a model boat, and the boat in question will be approximately 18" long and look something like this :-
and is is designed to be just a static model for sitting on a shelf, so I think it would be nice to make one with a working steam engine and have it working by radio control, I've dabbled with small steam engines in this thread
https://www.mig-welding.co.uk/forum/threads/jenny-wren-a-tiny-steam-steam-engine.82984/
and adapting a model for radio control in this thread
https://www.mig-welding.co.uk/forum/threads/radio-controlled-matchbox-lorry.95276/
and after watching videos by leslie proper on youtube I decided a working steam model would be nice and he has made tiny piston valved steam engines
and after a bit of light reading about model steam engines and boilers
so that's the introduction to this project, and I'll only be dealing with the steam plant in this thread as the machining and metal working might be of interest to others.
For the design of the steam plant Im starting off with a blank sheet of paper, and I keep changing my mind as to what I need to make, these are my main parts
1) a boiler to convert water to steam
2) a twin cylinder oscillating steam engine (with reversing regulator)
3) an electric boiler feed pump and control electrics
4) heating for the boiler
5)lubricator for the steam engine
6)oil/condensate separator and feed water heater
and these are my current ideas (that can change at any time)
1) Boiler
originally I was planing on making a vertical firetube boiler from 35mm dia copper pipe and 3/16" brake pipes to make the fire tubes like this. (its called a firetube boiler because the fire goes though the smaller tubes in the boiler)
but for various reasons decided not to do this and to make a horizonal watertube boiler like the boiler show below. its called a water tube boiler as the water to be heated is in the smaller tubes.
my boiler will made from 28mm copper tube and will only be 45mm long so the water tubes will go across the boiler rather than along is length. the steam will leave the engine in a tube under the boiler in the fire so that it will heat the steam up, dry it out and give the steam more power that the wet (saturated) steam that leaves a boiler.
2) Twin Cylinder Oscillating engine
I decided to do an oscillating engine as they dont have many moving parts and are easy to reverse, just by changing which port the steam goes into the engine. In thinking of having a bore of about 6mm dia and a stroke of 8mm and was originally thinking or making a "V" engine like the one show below as I thought the crankshaft would have been easier to make.
so it would have been similar to this but smaller (this is supplied with a regulator for reversing and lubricator)
but a simpler engine (and possibly lighter) would be a twin vertical engine similar to the one below, it has a regulator but the steam is delivered though the body of the engine so the plumbing is much easier to do.
3) Electric boiler feed pump.
Im thinking of using a minature 3v 100 rpm motor like the one below
to power a water pump with aprox 3mm bore by 3mm stroke using a scotch yoke to convert the rotary motion of the motor to the linear motion the pump will need
I'll use an electric level sensor to operate the motor.
4) Heating for the boiler.
I'm thinking of making it butane fired, which will involve making a gas tank, control valve and burner as I think for long running it should give a cleaner burn than methylated spirit firing, but the spirit firing would be easier to do.
5) If I was using wet steam I could get away without a lubricator for the engine but as the steam will be hot, lubrication of the cylinders will be required, the easiest option is to use a displacement lubricator like the one below. the lubricator of basically a sealed reservoir that is filled with oil and a small amount of steam is allowed into the reservoir. this will then condense into water. the water will sink to the bottom of the oil. the oil with then overflow into the steam pipe and will then go into the engine to lubricate it.
6) oil/condensate separator and water feed heater.
as the exhaust steam has oil in it, you have to separate the oil from the water in model boats so that you're not poluting ponds, the easiest way to do this is to have the exhaust steam from the engine into closed container like a cyclonic vacuum cleaner. the oil will stick to the wall of the container and then sink to the bottom and the steam can then exhaust from the container into the air as it will no be clean. if the feed water tube goes though this container it will pick up heat from the steam so should improve the thermal efficiency of the steam plant, as cold water being feed into the boiler will cause the steam pressure to drop.
so thats about it, with a bit of luck it will work, and at this stage I have no idea what it will end up like. I'll try to post the work Ive done on the boiler tomorrow.
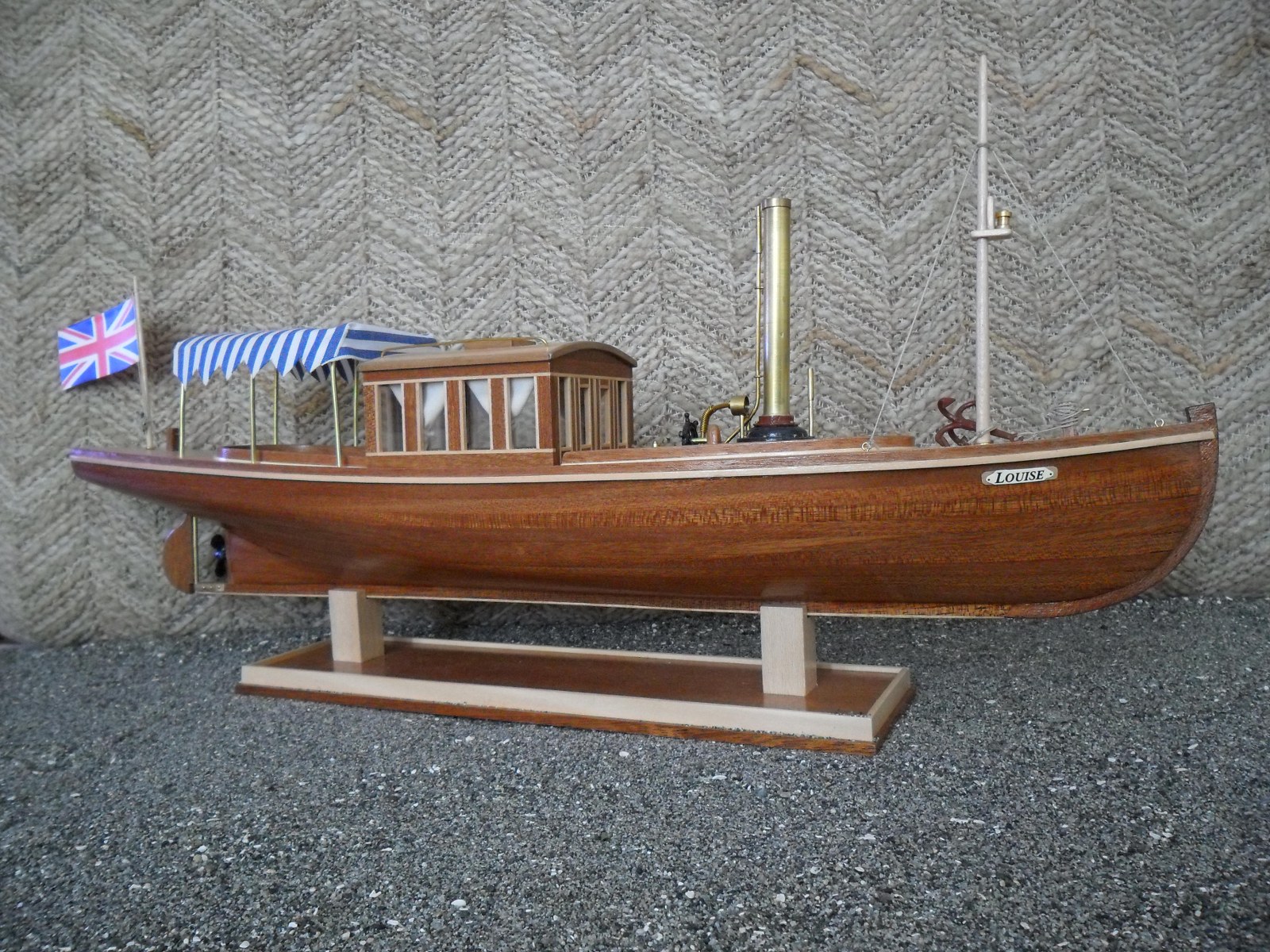
and is is designed to be just a static model for sitting on a shelf, so I think it would be nice to make one with a working steam engine and have it working by radio control, I've dabbled with small steam engines in this thread
https://www.mig-welding.co.uk/forum/threads/jenny-wren-a-tiny-steam-steam-engine.82984/
and adapting a model for radio control in this thread
https://www.mig-welding.co.uk/forum/threads/radio-controlled-matchbox-lorry.95276/
and after watching videos by leslie proper on youtube I decided a working steam model would be nice and he has made tiny piston valved steam engines
and after a bit of light reading about model steam engines and boilers
so that's the introduction to this project, and I'll only be dealing with the steam plant in this thread as the machining and metal working might be of interest to others.
For the design of the steam plant Im starting off with a blank sheet of paper, and I keep changing my mind as to what I need to make, these are my main parts
1) a boiler to convert water to steam
2) a twin cylinder oscillating steam engine (with reversing regulator)
3) an electric boiler feed pump and control electrics
4) heating for the boiler
5)lubricator for the steam engine
6)oil/condensate separator and feed water heater
and these are my current ideas (that can change at any time)
1) Boiler
originally I was planing on making a vertical firetube boiler from 35mm dia copper pipe and 3/16" brake pipes to make the fire tubes like this. (its called a firetube boiler because the fire goes though the smaller tubes in the boiler)
but for various reasons decided not to do this and to make a horizonal watertube boiler like the boiler show below. its called a water tube boiler as the water to be heated is in the smaller tubes.

my boiler will made from 28mm copper tube and will only be 45mm long so the water tubes will go across the boiler rather than along is length. the steam will leave the engine in a tube under the boiler in the fire so that it will heat the steam up, dry it out and give the steam more power that the wet (saturated) steam that leaves a boiler.
2) Twin Cylinder Oscillating engine
I decided to do an oscillating engine as they dont have many moving parts and are easy to reverse, just by changing which port the steam goes into the engine. In thinking of having a bore of about 6mm dia and a stroke of 8mm and was originally thinking or making a "V" engine like the one show below as I thought the crankshaft would have been easier to make.
so it would have been similar to this but smaller (this is supplied with a regulator for reversing and lubricator)
but a simpler engine (and possibly lighter) would be a twin vertical engine similar to the one below, it has a regulator but the steam is delivered though the body of the engine so the plumbing is much easier to do.
3) Electric boiler feed pump.
Im thinking of using a minature 3v 100 rpm motor like the one below
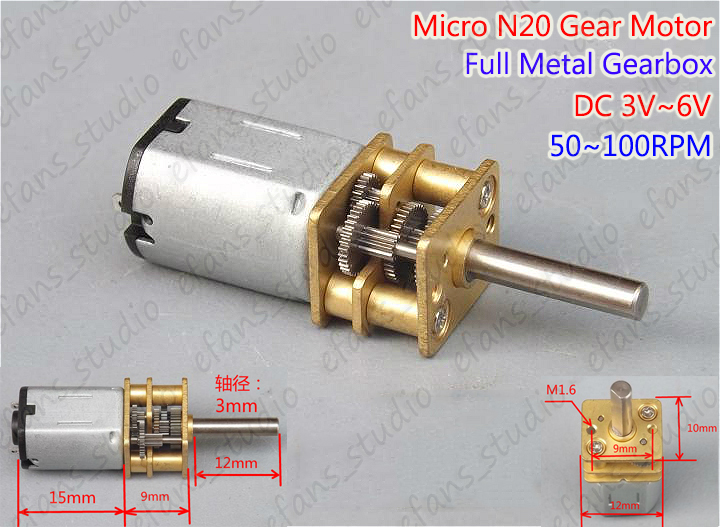
to power a water pump with aprox 3mm bore by 3mm stroke using a scotch yoke to convert the rotary motion of the motor to the linear motion the pump will need
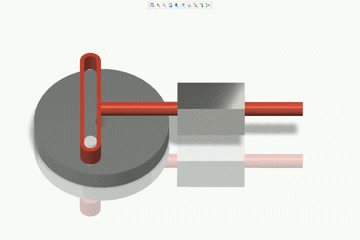
I'll use an electric level sensor to operate the motor.
4) Heating for the boiler.
I'm thinking of making it butane fired, which will involve making a gas tank, control valve and burner as I think for long running it should give a cleaner burn than methylated spirit firing, but the spirit firing would be easier to do.
5) If I was using wet steam I could get away without a lubricator for the engine but as the steam will be hot, lubrication of the cylinders will be required, the easiest option is to use a displacement lubricator like the one below. the lubricator of basically a sealed reservoir that is filled with oil and a small amount of steam is allowed into the reservoir. this will then condense into water. the water will sink to the bottom of the oil. the oil with then overflow into the steam pipe and will then go into the engine to lubricate it.

6) oil/condensate separator and water feed heater.
as the exhaust steam has oil in it, you have to separate the oil from the water in model boats so that you're not poluting ponds, the easiest way to do this is to have the exhaust steam from the engine into closed container like a cyclonic vacuum cleaner. the oil will stick to the wall of the container and then sink to the bottom and the steam can then exhaust from the container into the air as it will no be clean. if the feed water tube goes though this container it will pick up heat from the steam so should improve the thermal efficiency of the steam plant, as cold water being feed into the boiler will cause the steam pressure to drop.
so thats about it, with a bit of luck it will work, and at this stage I have no idea what it will end up like. I'll try to post the work Ive done on the boiler tomorrow.