Paul in Wiltshire
Member
- Messages
- 64
- Location
- UK Wiltshire
(also posted on Harrison Lathes group)
I have ordered a Multifix QCTP and holders for my M300. I have ordered size E from CreateTool in China, it should arrive in early July.
I have decided that I’d like to install the new tool post on to a fixed post to replace the top-slide. It’s not my idea, or a new idea, but I thought some of you might be interested. Robin Renzetti has a very detailed explanation on his YouTube channel, although I won't be going to his extremes.
As I see it there are three main benefits to removing the top slide:
The downsides seem to be:
I intend to fix my post using four t-nuts and the central pin. I have decided to make my own t-nuts with curved sides to fit the slot. As I want my post to have a fixed angular position, I am also adding a location dowel to register the post. Drilling/reaming this hole for the registration pin is the only modification I will be making to the original lathe parts. I have sketched up all the parts that I am going to make in Fusion 360. Here is a view of the fixing hardware for the fixed post.
The post itself will be cast iron (meehanite). It will have the features needed to fix it to the cross slide, the bottom surface will have some relief cut so that it isn’t bearing over the whole surface. On its top surface will be a hole for the stud to fix the QCTP, and a hole to register the QCTP. The QCTP isn’t mounted centrally, so that the tool is presented in front of the cross slide to give more clearance when facing large diameters. Don’t want to extend it forward too far or it will compromise rigidity.
The front of the post will have a flat machined to allow it to be indicated in square and to aid machining. I plan to turn a taper on it so that chips don’t build up.
I will machine a stud to fix the QCTP, this has a 20mm feature to locate the QCTP, and two threads to fix it in the post and for the nut. Here is the sketch of the post and fixing stud+nut.
Here is the sketch showing it all together.
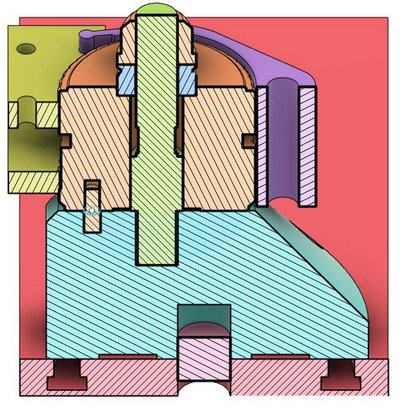
I’ll make some additional posts showing the manufacture of the bits.
I have ordered a Multifix QCTP and holders for my M300. I have ordered size E from CreateTool in China, it should arrive in early July.
I have decided that I’d like to install the new tool post on to a fixed post to replace the top-slide. It’s not my idea, or a new idea, but I thought some of you might be interested. Robin Renzetti has a very detailed explanation on his YouTube channel, although I won't be going to his extremes.
As I see it there are three main benefits to removing the top slide:
- Rigidity: parting and heavy cuts with the top slide gib clamped show much less chatter. Having a fixed tool post should be even better;
- Repeatability: I have a DRO fitted to X and Z, the top slide can mean that tool offsets aren’t repeatable;
- Optimum tool post height: The fixed tool post can be designed to be at the optimum position to allow all your tools to be adjusted to centre height without resorting to spacers/machining tool holders.
The downsides seem to be:
- Harder to cut long tapers: I don’t have a taper attachment, I do have a hydraulic copier, but it isn’t fitted yet. I can cut small tapers with a form tool;
- Inability to offset top slide for thread cutting: I have cut threads without offsetting the top slide and with it set at 29.5 degrees (for metric / UN). To be honest I can’t see much benefit from spinning it around and make cuts just using the cross slide. I think this use of the "compound" is popular in the US, but in Europe it only seems to be practised by those that learnt from YouTube;
- Modifications to the lathe: No one wants to turn their lathe into Swiss cheese with lots of new machining to fit parts. I intend to fit the fixed post with the minimum amount of non-reversible changes. I will keep my top slide and its Dickson QCTP for those occasions when I really need it, and my design should allow me to swap between fixed post and top slide in minutes;
- Clearance for large/odd parts: Sometimes extending out the top slide can be useful to give clearance/access when turning parts that won’t swing over the cross slide.
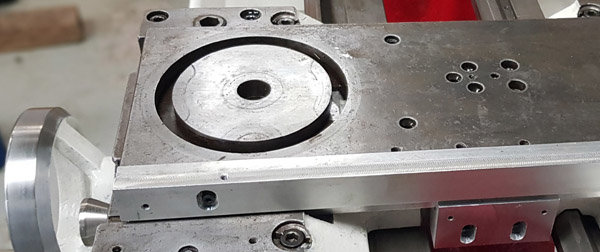
I intend to fix my post using four t-nuts and the central pin. I have decided to make my own t-nuts with curved sides to fit the slot. As I want my post to have a fixed angular position, I am also adding a location dowel to register the post. Drilling/reaming this hole for the registration pin is the only modification I will be making to the original lathe parts. I have sketched up all the parts that I am going to make in Fusion 360. Here is a view of the fixing hardware for the fixed post.
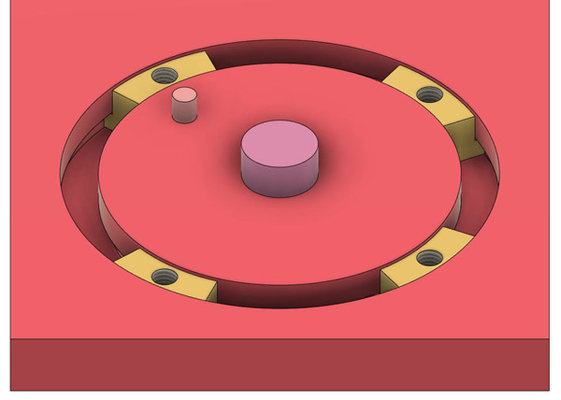
The post itself will be cast iron (meehanite). It will have the features needed to fix it to the cross slide, the bottom surface will have some relief cut so that it isn’t bearing over the whole surface. On its top surface will be a hole for the stud to fix the QCTP, and a hole to register the QCTP. The QCTP isn’t mounted centrally, so that the tool is presented in front of the cross slide to give more clearance when facing large diameters. Don’t want to extend it forward too far or it will compromise rigidity.
The front of the post will have a flat machined to allow it to be indicated in square and to aid machining. I plan to turn a taper on it so that chips don’t build up.
I will machine a stud to fix the QCTP, this has a 20mm feature to locate the QCTP, and two threads to fix it in the post and for the nut. Here is the sketch of the post and fixing stud+nut.
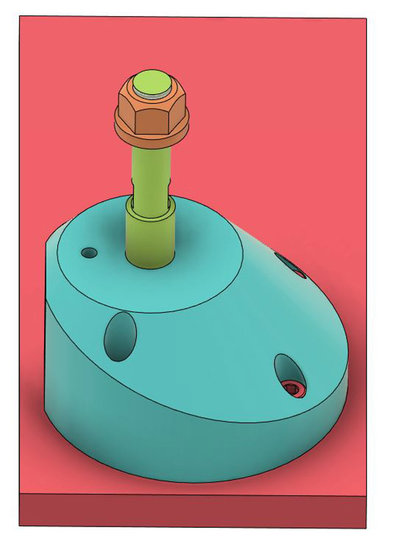
Here is the sketch showing it all together.
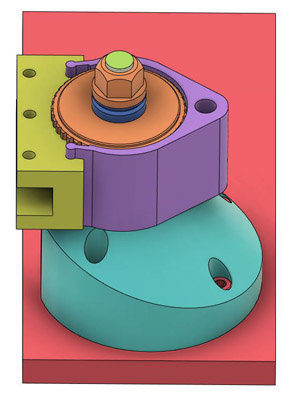
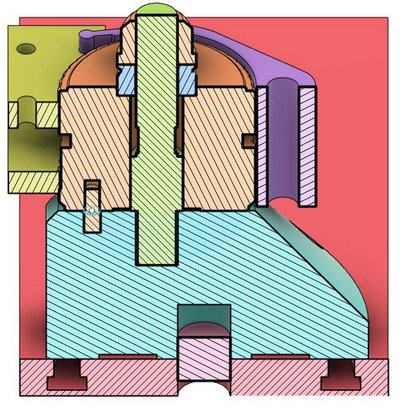
I’ll make some additional posts showing the manufacture of the bits.