After much deliberating, i finally decided to go for the Esab Caddy. The flexibility of being able to take it anywhere eventually swung it, opens up a lot of possibilities for where it could be used.
The last and only other time I've used a mig was about 14 years ago and I only did about a dozen tac welds using a friends machine so for the past wee while I've been reading through various tutorials and watching videos on youtube so had half an idea what I was supposed to do with it lol
One thing I did notice from the outset, the tip seems to be quite short, read on few things which suggested the tip should be just below or flush with the shroud to maintain a short stickout? (I'd already had a quick go before I took this pic)
With it in Qset mode, 0.8mm wire, set for 3mm plate, wire feed 8.5m/min initially these are the first beads I did on a bit of 3mm mild steel.
From right to left in both pictures i experimented a little with wire feed and adjusting the temperature but doesnt really appear to have made a great deal of difference? Suspect most of it is to do with my travel speed
They look not too bad in my eyes but suspect they are possibly a little cold? Not really any signs of penetration on the reverse side but should I get that with 3mm plate and 0.8mm wire?
I did a few more runs on some 3mm plate then had a go at a corner, box section and the plate are 3mm, machine set to 3mm with wire speed at 8.9 iirc and the temp adjust at +6 or 7 out of 9.
(I tacked the two bits together at the right hand side first hence the bad bit)
I just welded one side then did a destructive test
Appears to have achieved sufficent penetration barr the first bit where the tac was.
Any comments very much appreciated
Kenny

The last and only other time I've used a mig was about 14 years ago and I only did about a dozen tac welds using a friends machine so for the past wee while I've been reading through various tutorials and watching videos on youtube so had half an idea what I was supposed to do with it lol
One thing I did notice from the outset, the tip seems to be quite short, read on few things which suggested the tip should be just below or flush with the shroud to maintain a short stickout? (I'd already had a quick go before I took this pic)
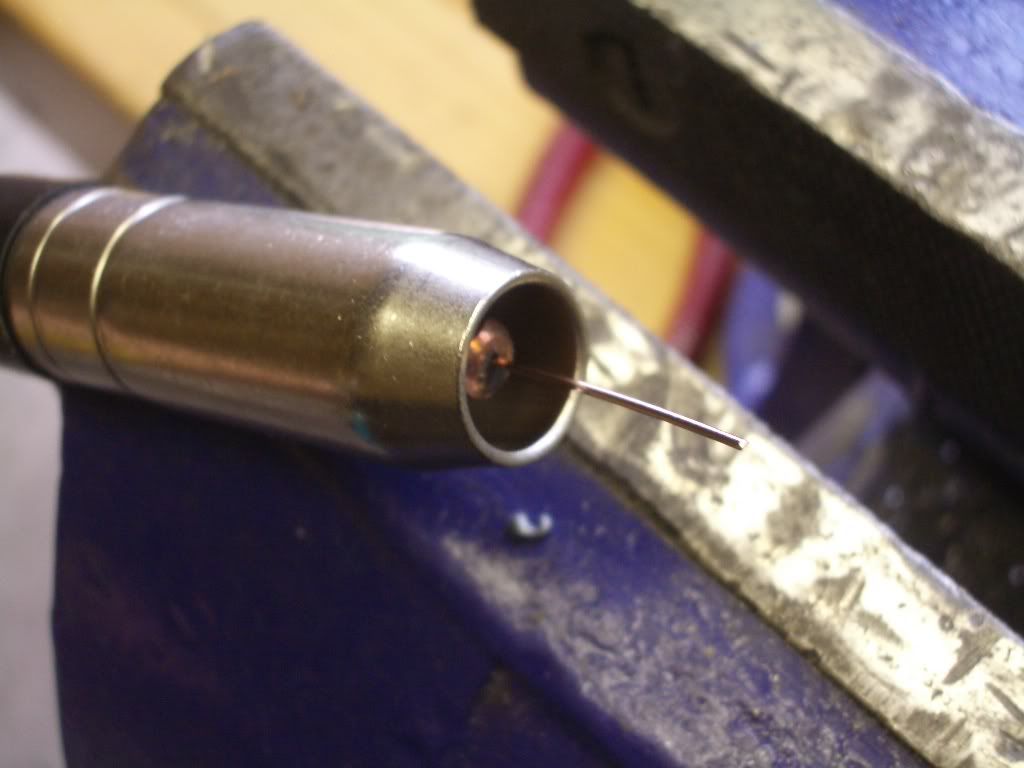
With it in Qset mode, 0.8mm wire, set for 3mm plate, wire feed 8.5m/min initially these are the first beads I did on a bit of 3mm mild steel.
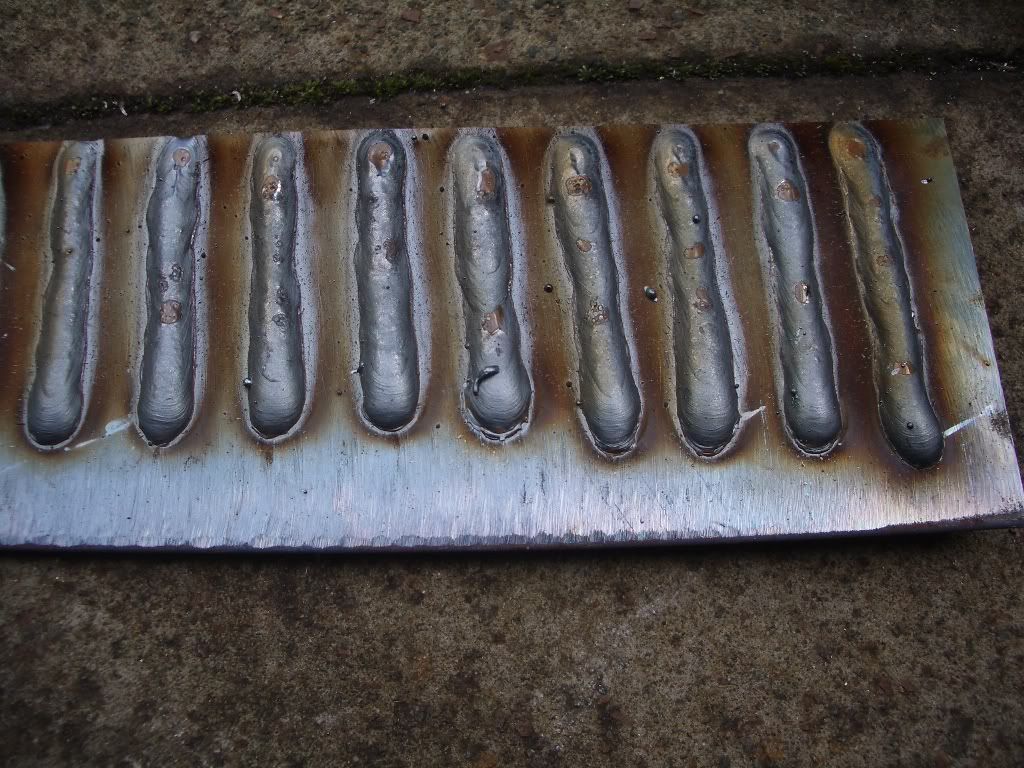
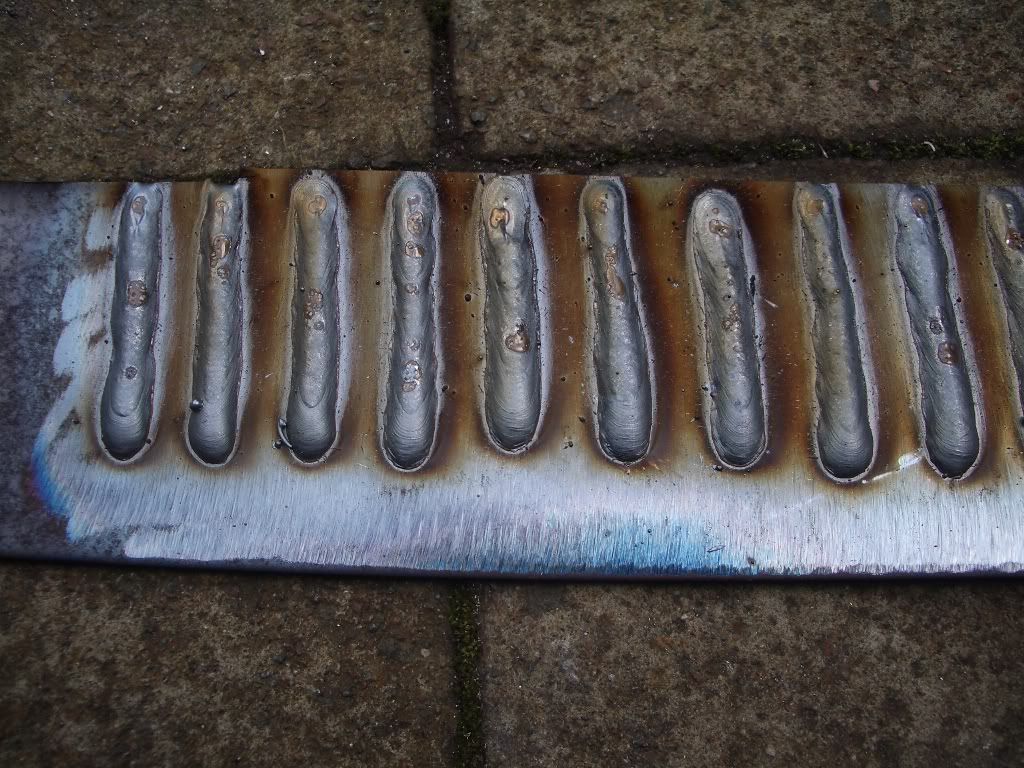
From right to left in both pictures i experimented a little with wire feed and adjusting the temperature but doesnt really appear to have made a great deal of difference? Suspect most of it is to do with my travel speed
They look not too bad in my eyes but suspect they are possibly a little cold? Not really any signs of penetration on the reverse side but should I get that with 3mm plate and 0.8mm wire?
I did a few more runs on some 3mm plate then had a go at a corner, box section and the plate are 3mm, machine set to 3mm with wire speed at 8.9 iirc and the temp adjust at +6 or 7 out of 9.

(I tacked the two bits together at the right hand side first hence the bad bit)
I just welded one side then did a destructive test
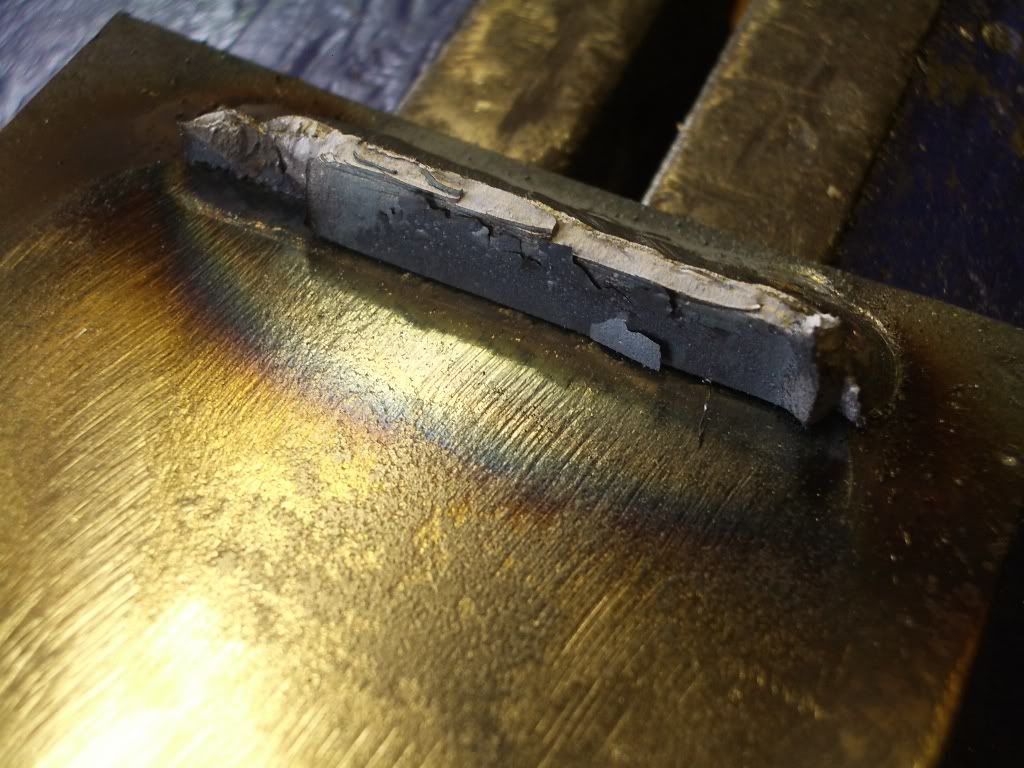
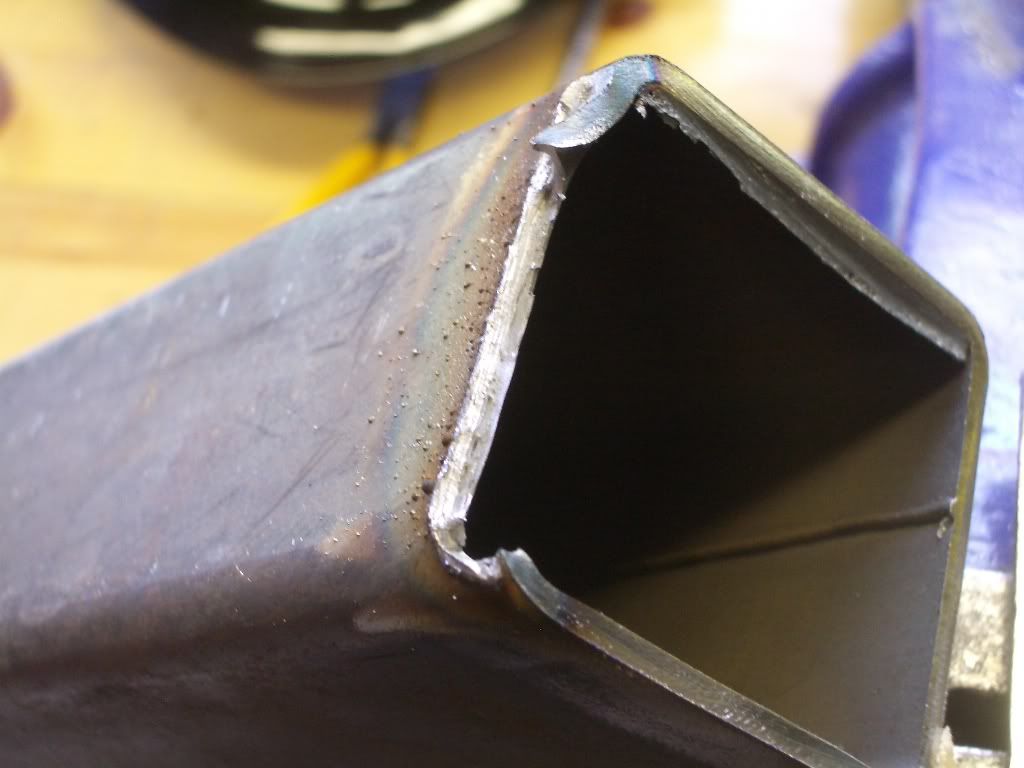
Appears to have achieved sufficent penetration barr the first bit where the tac was.
Any comments very much appreciated
Kenny