Sometime ago I took ownership of a very large ~9' long welding/fabrication table. Due to the size and weight of it, it lived outside. I had planned to learn to weld on this table, and go onto using it to fabricate things for myself, friends and family. Best laid plans and all that; I spent much of my time renovating it, removing loads of weld building up from the previous owners, treating the rust and painting it. By the time I got around to cleaning the surface of the table up my tarp failed and the wouldn't protect my table anymore.
A combination of factors have meant that I've probably used the table more to rest things on and cut firewood on rather than learn to weld with it. Normally when I'm free the weather is awful or the dog and family are busy so I can't use the table where it was located, on the drive.
To get more use out of it, I decided to cut it down and relocate the smaller table into the garage. This Saturday I was planning on cutting the table down to about 1/3 of its original size from the leftward end, in such a manner that I would then have a clean edge and two existing legs already in place.
Removing the tarps and my wood and metal I had stored underneath today, I was reminded that the frame of the table lends itself to being cut in half, which would be around 4.5' square rather than down to 1/3 of its original size. As there is no longer a car in the garage at the moment, and this being only a temporary table until I build one from scratch, I felt I'd take advantage of the frame and more space and "just cut it in half".
TLDR; my fab table is now square, half its original size and is relocated inside the garage.
The starting off point. This photo was taken on a much warmer day, earlier in the year.
Inpatient as ever, I made a start today, rather than waiting for Saturdays better weather. Got sick of waiting for the rain to stop long enough to flap disc the frame to weld on leg extensions in the middle... with a degree of difficulty, we used my platform trolley and got the full table inside the garage out of the rain.
I was just about to begin welding some leg extensions on the center legs, which as designed don't touch the ground, when a friend suggested it might be easier to cut the table down first, so the welding can be done in a more comfortable position.
So out came my Clarke Contractor and the new 115mm diamond cut off wheel from Lenox. I used a piece of old bed frame clamped to the table to help keep the cut as straight as possible.
The 115mm cut of wheel seemed to be working fine; sadly my grinder wasn't... first smoke and then flames coming out of the casing meant a more suitable tool was needed. Luckily a friend borrowed me one of these. Go big or go home :-)
It was still hard going, and it wasn't easy handling such a heavy tool all the way across the cut.
Here is where things had to be left for one day, the table is cut in half and left on end ready for new leg extensions welding into place. The legs from the remainder of the table were cut down leaving the rest of the 5mm plate on the floor of the garage in the background.
A combination of factors have meant that I've probably used the table more to rest things on and cut firewood on rather than learn to weld with it. Normally when I'm free the weather is awful or the dog and family are busy so I can't use the table where it was located, on the drive.
To get more use out of it, I decided to cut it down and relocate the smaller table into the garage. This Saturday I was planning on cutting the table down to about 1/3 of its original size from the leftward end, in such a manner that I would then have a clean edge and two existing legs already in place.
Removing the tarps and my wood and metal I had stored underneath today, I was reminded that the frame of the table lends itself to being cut in half, which would be around 4.5' square rather than down to 1/3 of its original size. As there is no longer a car in the garage at the moment, and this being only a temporary table until I build one from scratch, I felt I'd take advantage of the frame and more space and "just cut it in half".
TLDR; my fab table is now square, half its original size and is relocated inside the garage.
The starting off point. This photo was taken on a much warmer day, earlier in the year.
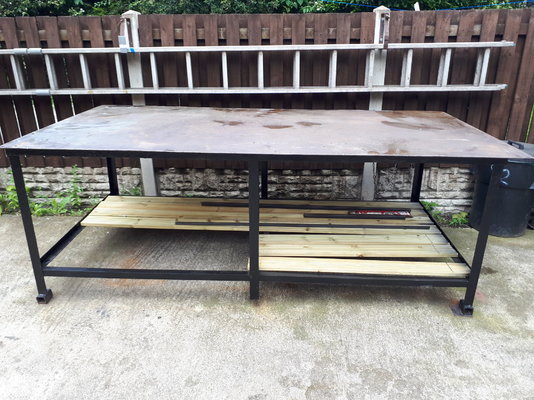
Inpatient as ever, I made a start today, rather than waiting for Saturdays better weather. Got sick of waiting for the rain to stop long enough to flap disc the frame to weld on leg extensions in the middle... with a degree of difficulty, we used my platform trolley and got the full table inside the garage out of the rain.
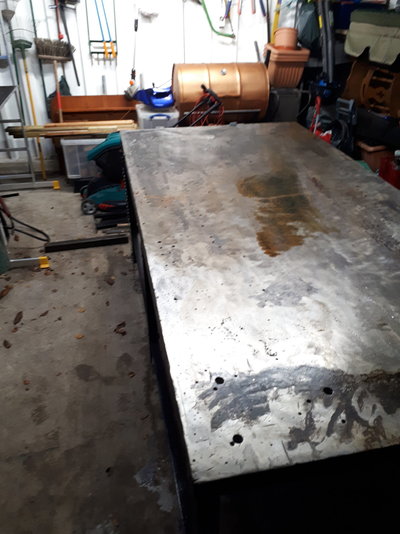
I was just about to begin welding some leg extensions on the center legs, which as designed don't touch the ground, when a friend suggested it might be easier to cut the table down first, so the welding can be done in a more comfortable position.
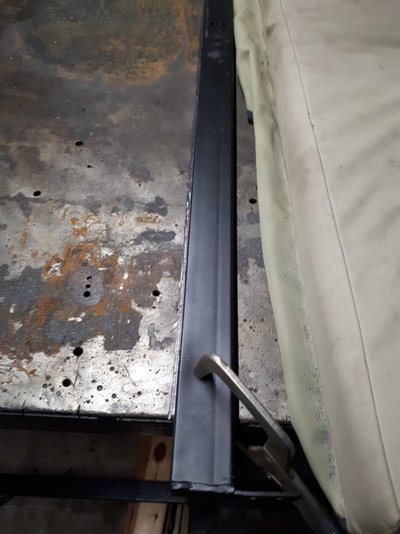
So out came my Clarke Contractor and the new 115mm diamond cut off wheel from Lenox. I used a piece of old bed frame clamped to the table to help keep the cut as straight as possible.
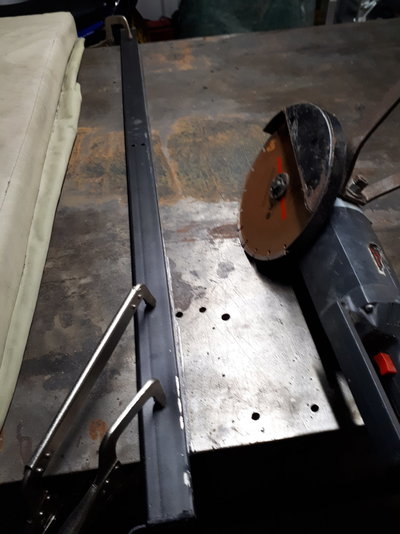
The 115mm cut of wheel seemed to be working fine; sadly my grinder wasn't... first smoke and then flames coming out of the casing meant a more suitable tool was needed. Luckily a friend borrowed me one of these. Go big or go home :-)
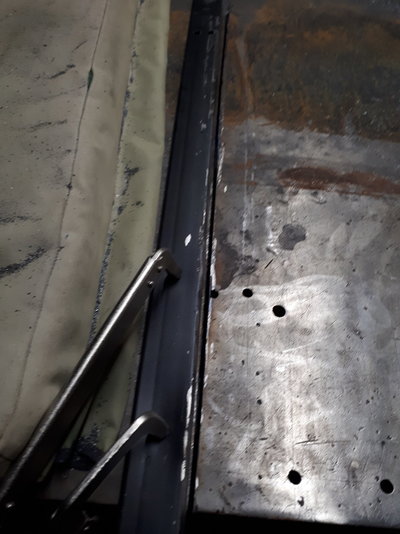
It was still hard going, and it wasn't easy handling such a heavy tool all the way across the cut.
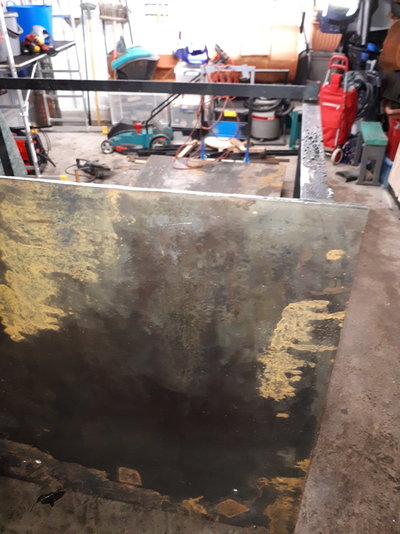
Here is where things had to be left for one day, the table is cut in half and left on end ready for new leg extensions welding into place. The legs from the remainder of the table were cut down leaving the rest of the 5mm plate on the floor of the garage in the background.