Dcal
Member
- Messages
- 4,079
- Location
- Antrim Northern Ireland
Hi all, new to machining and I have just got the Boxford lathe I bought from Austin on here, bolted down and up and running.
I downloaded the "Boxford Know your Lathe" book and got a bit of info off the Boxford Site to get me started.
There are 3 holes in the steel frame for fixings and I used 12mm thread bar chemically anchored into the concrete floor with a nut and washer top and bottom so I could adjust the base up or down and get a good starting point for leveling the bed.
I used an old engineers level to adjust and set the bed and I got it pretty close I think.
Unfortunately while i was working around the lathe I touched the level that was sitting across the bed, it fell into the stand and let the bubble out.
Its a Rabone 8" and the vial seems to be about 75mm x 13mm.
Anyone know where I can get a replacement vial and can they be replaced?
I tried screwing it apart but it seems pretty solid and I didn't want to force it.
Is there a trick in getting them apart? Or is it a specialist job?
After a few choice words I went back to the lathe.
I tried checking out the functions and it all seemed good until I was trying out the powered feed.
While running the screw cutting function the motor came under a lot of load and I switched it off.
The gear train seemed locked up but when I disengaged the drive all seemed ok apart from the screw thread which was solid.
I tried all the functions on the apron but it was still locked up so I partly disassembled the apron on the lathe and I found that the nut that holds the drive nut on the feed screws had tightened and locked solid against the apron body stopping the lead screw from turning at all.
I initially thought the nut had picked up and seized on the apron body but I was able to wind the complete apron off the lead screw and fully disassemble it on the bench.
I discovered that there was nothing stopping the lock nut from over tightening. A quick search on the web uncovered that there should be a small pin through the feed nut, the lock nut and key way to keep the nut from coming loose or over tightening.
The one I have does not have a locking pin or a hole in the key for a pin.
There is a hole drilled through the feed nut and lock nut and the ends of the key have nibs (to stop the key coming completely out of the nut?)
There isn't a slot in the lock-nut for the key nib which might also work, but the distance between the nibs is longer than the complete drive nut assembly anyway.
Are there different ways of locking this on different models?
Whats the best fix?
Can I just drill the key way and fit a steel pin?
I was thinking it would be best to have a pin, slightly smaller than the holes already drilled in the lock nut and feed nut and just tack welding the pin to the key.
Would that work?
Not one of the best days I've had, but its all learning.
Thanks in advance
I downloaded the "Boxford Know your Lathe" book and got a bit of info off the Boxford Site to get me started.
There are 3 holes in the steel frame for fixings and I used 12mm thread bar chemically anchored into the concrete floor with a nut and washer top and bottom so I could adjust the base up or down and get a good starting point for leveling the bed.
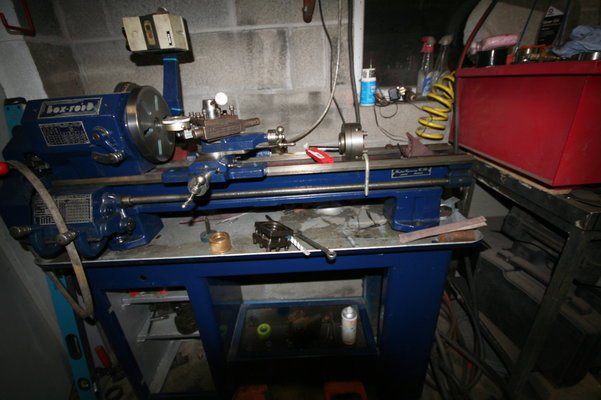
I used an old engineers level to adjust and set the bed and I got it pretty close I think.
Unfortunately while i was working around the lathe I touched the level that was sitting across the bed, it fell into the stand and let the bubble out.
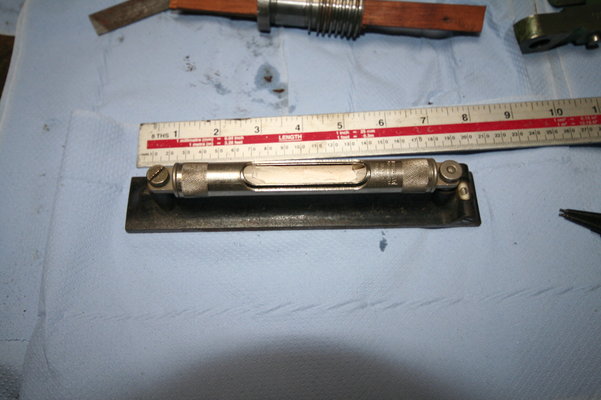
Its a Rabone 8" and the vial seems to be about 75mm x 13mm.
Anyone know where I can get a replacement vial and can they be replaced?
I tried screwing it apart but it seems pretty solid and I didn't want to force it.
Is there a trick in getting them apart? Or is it a specialist job?
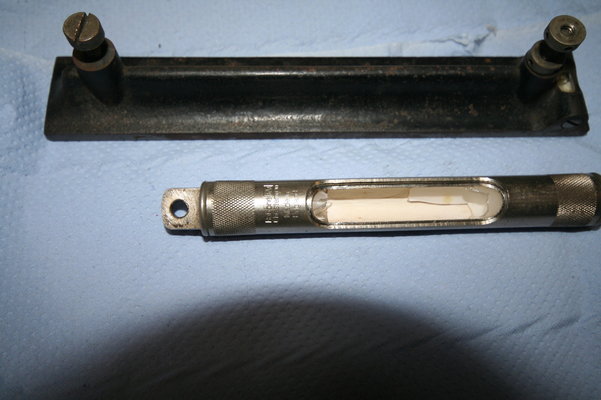
After a few choice words I went back to the lathe.
I tried checking out the functions and it all seemed good until I was trying out the powered feed.
While running the screw cutting function the motor came under a lot of load and I switched it off.
The gear train seemed locked up but when I disengaged the drive all seemed ok apart from the screw thread which was solid.
I tried all the functions on the apron but it was still locked up so I partly disassembled the apron on the lathe and I found that the nut that holds the drive nut on the feed screws had tightened and locked solid against the apron body stopping the lead screw from turning at all.
I initially thought the nut had picked up and seized on the apron body but I was able to wind the complete apron off the lead screw and fully disassemble it on the bench.
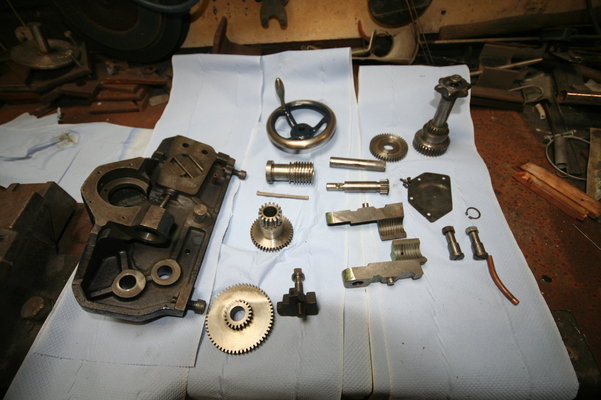
I discovered that there was nothing stopping the lock nut from over tightening. A quick search on the web uncovered that there should be a small pin through the feed nut, the lock nut and key way to keep the nut from coming loose or over tightening.
The one I have does not have a locking pin or a hole in the key for a pin.
There is a hole drilled through the feed nut and lock nut and the ends of the key have nibs (to stop the key coming completely out of the nut?)
There isn't a slot in the lock-nut for the key nib which might also work, but the distance between the nibs is longer than the complete drive nut assembly anyway.
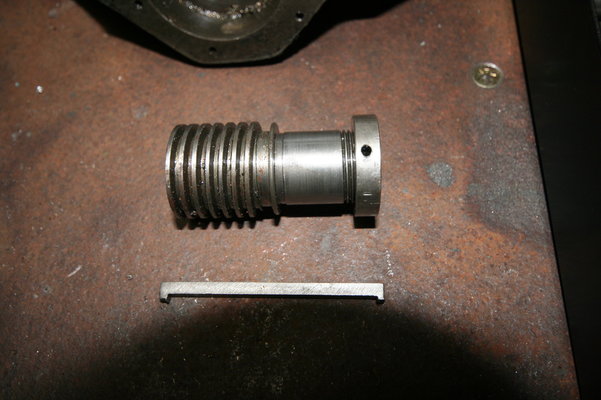
Are there different ways of locking this on different models?
Whats the best fix?
Can I just drill the key way and fit a steel pin?
I was thinking it would be best to have a pin, slightly smaller than the holes already drilled in the lock nut and feed nut and just tack welding the pin to the key.
Would that work?
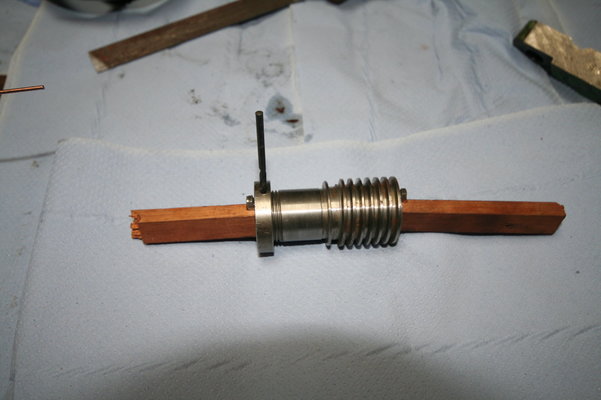
Not one of the best days I've had, but its all learning.
Thanks in advance