- Messages
- 6,338
mmhhhh you may all be bored of seeing this stuff, but id thought id do a post up, iv been wanting to get away from the stick for this sort of work, time scale stuff, so have been trying different wires, the ones I used were 1.2 flux cored, 1.2 metal cored, 1.6 solid, and 1.6 metal cored..... the conclusion is I'm gonna run 3 wires, 1.6 metal cored, 1.2 metal cored, 1.2 flux cored....
Technical AL sent me a 5KG sample of Lincolns flux cored, I ran the entire roll doing the positional stringers in the last photo , hard to get used to but ran nice in the end, In total welding a lump like that, took around 10KGs of flux cored and around 25KG of metal cored......
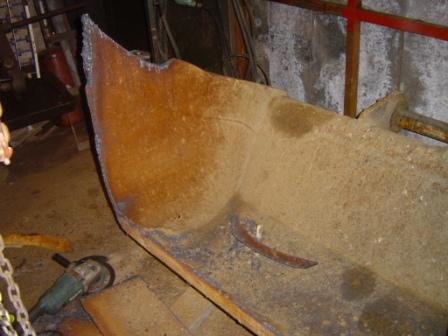
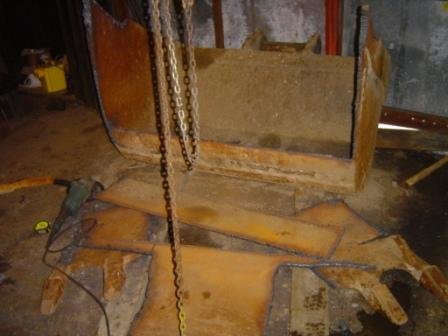
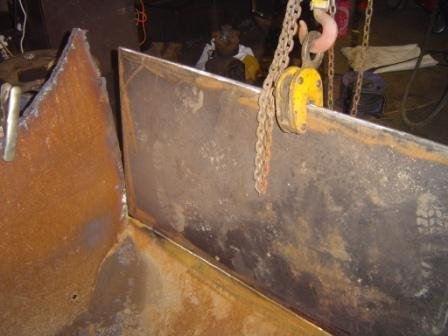
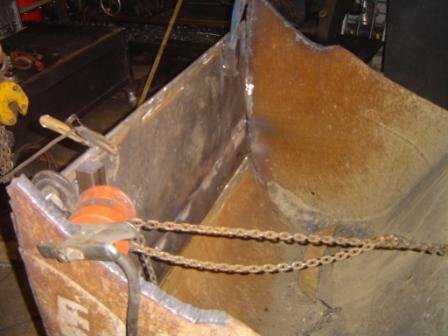
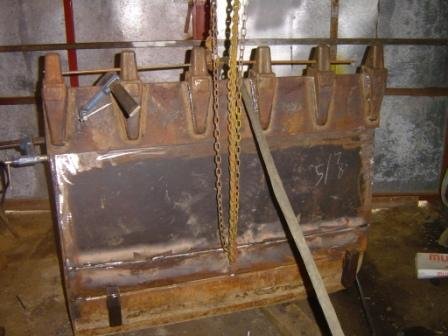
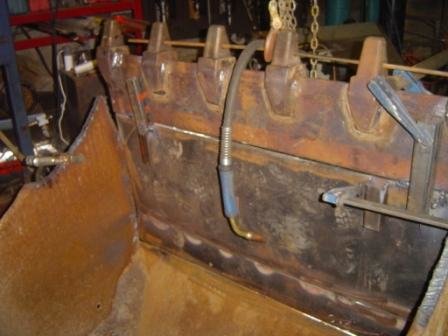
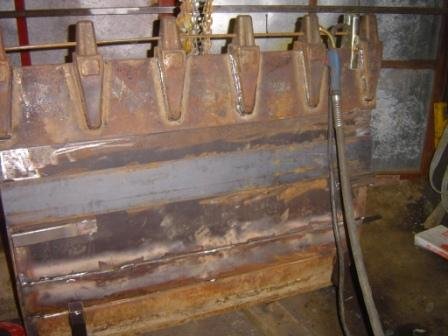
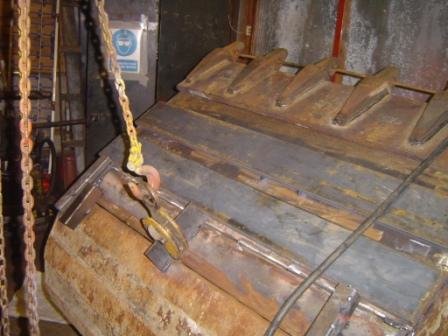
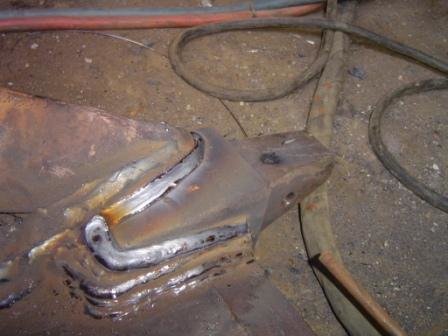
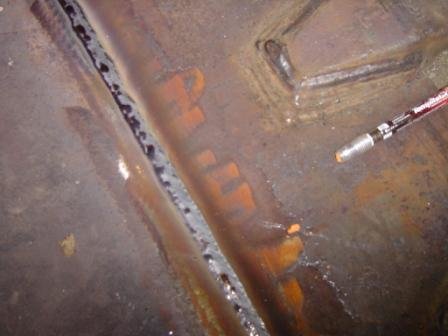
Technical AL sent me a 5KG sample of Lincolns flux cored, I ran the entire roll doing the positional stringers in the last photo , hard to get used to but ran nice in the end, In total welding a lump like that, took around 10KGs of flux cored and around 25KG of metal cored......
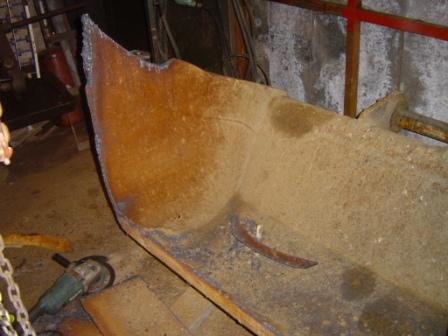
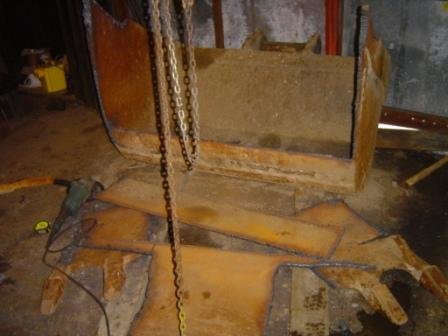
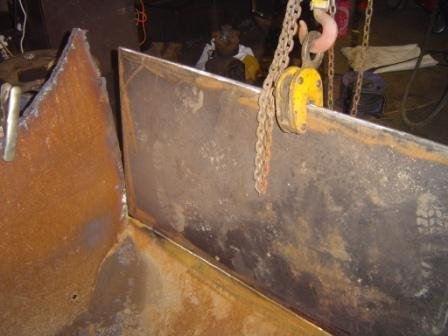
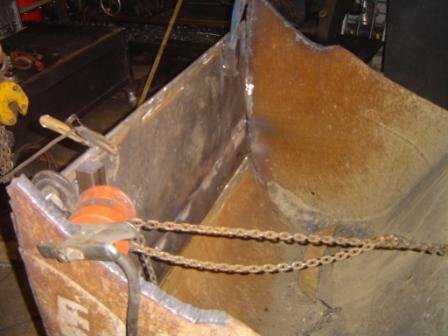
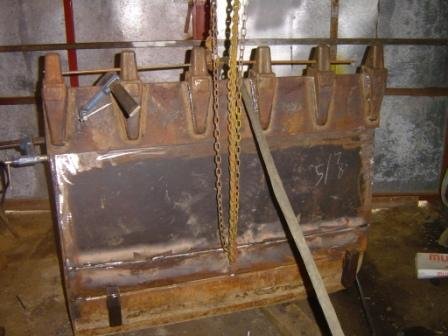
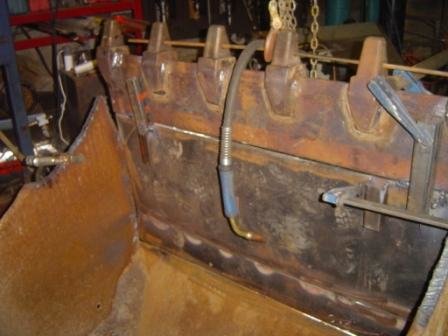
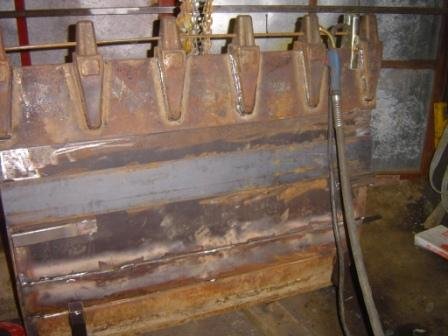
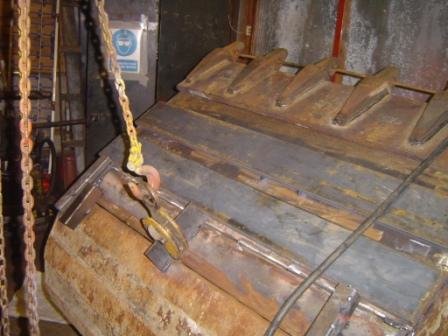
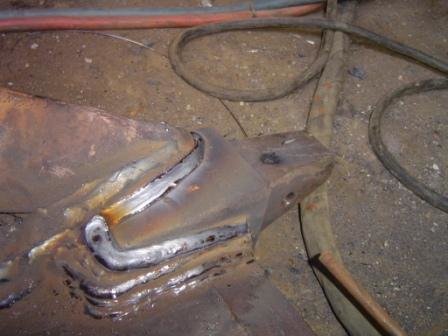
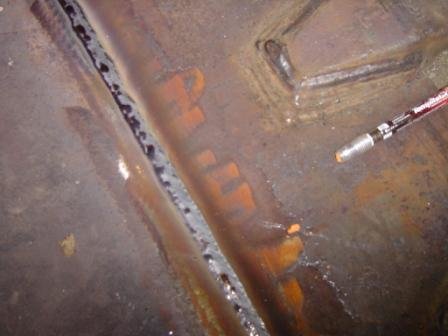