SV1BDO
Member
- Messages
- 101
- Location
- Greece, Egio City
My welder (Riland 175GD), a simple synergic MIG machine, has the ability to adjust Inductance & Arc Force. I like to use the Inductance at the maximum level (+10) as it reduces spattering. Now I made some tests adjusting the Arc Force at the maximul level (+20), when you get into globular transfer mode.
In the first series of pics I have welded 5mm thick hinges on 4mm thick ST37-2 mild steel plate, using short arc transfer (Inductance +10, Arc Force 0).
Without changing other settings (Voltage was at 21.0V & speed at 8,1m, as shown from the simple synergic curve of Riland), I adjusted the Arc Force at the maximum value of +20. The manual says that the numbers shown for Inductance & Arc Force are percentage and not absolute values. Bellow is the result, welding 4mm plates. The seam is more fluid, but there are a lot of oversized spatters.
The backside of the plate show signs of good penetration. There are also some droplets (or spatters, I don't know exactly) that did not melt into the pool and are still visible. Despite of these small flaws, I believe that globular transfer do better penetration in thick material (over 5mm).
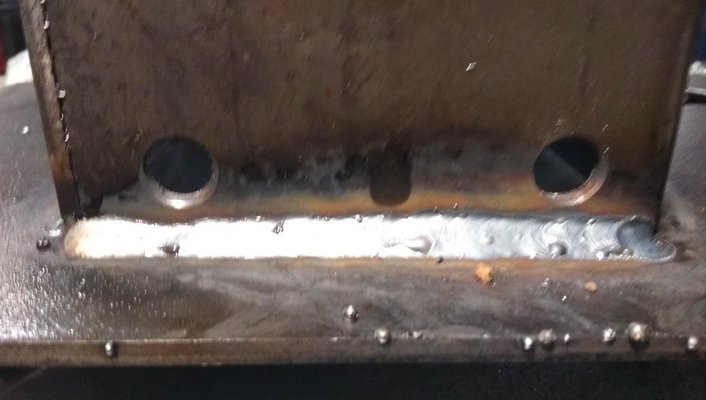
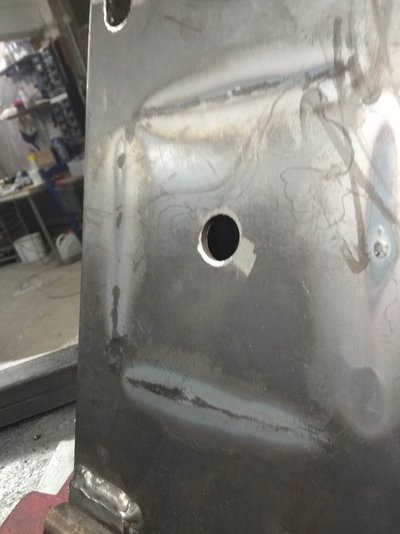
In the first series of pics I have welded 5mm thick hinges on 4mm thick ST37-2 mild steel plate, using short arc transfer (Inductance +10, Arc Force 0).
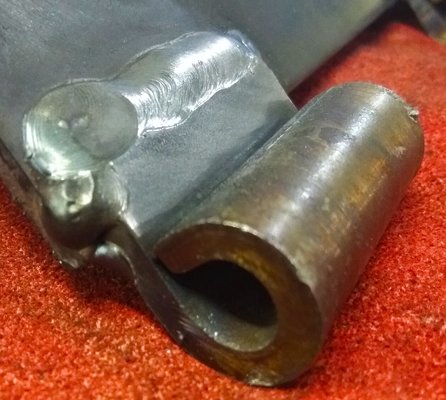
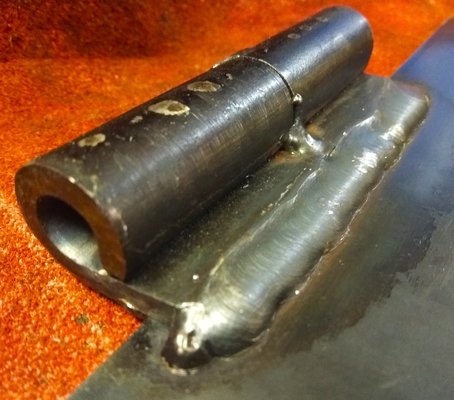

Without changing other settings (Voltage was at 21.0V & speed at 8,1m, as shown from the simple synergic curve of Riland), I adjusted the Arc Force at the maximum value of +20. The manual says that the numbers shown for Inductance & Arc Force are percentage and not absolute values. Bellow is the result, welding 4mm plates. The seam is more fluid, but there are a lot of oversized spatters.
The backside of the plate show signs of good penetration. There are also some droplets (or spatters, I don't know exactly) that did not melt into the pool and are still visible. Despite of these small flaws, I believe that globular transfer do better penetration in thick material (over 5mm).
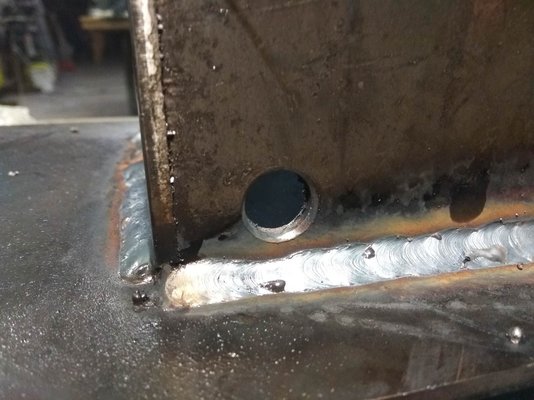
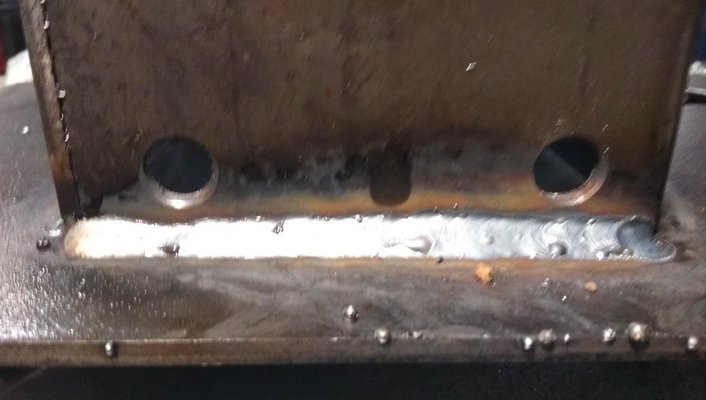
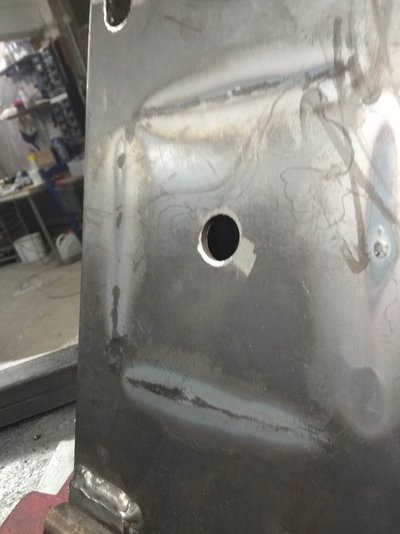