brewdexta
The biggest tool in the box
- Messages
- 5,737
- Location
- UK
The colchester chipmaster uses a Kopps Variator to alter speed, this is a mechanical method using 2 cones in an oil bath, by moving the cones the ratios change. Great bit of kit and you can still get parts from Allspeeds for them but they are expensive and can be noisy in their autumn years.
I decided to swap out mine and replace the motor with a more modern 3 phase motor and inverter as I bought the lathe quite cheap and thought it was worth the investment.
There are various configurations with the variator on the end of the motor or seperate, see lathes.co.uk for details.
My chipmaster was an early one with the variator on the end, here's a pic of the old motor and variator being extracted by mounting it on a pallet truck with some timber strapped to it.
Here's the list of parts used from Bearing Boys for the pulley and belts, I did this about 10 months ago so prices may have changed
1 x 1108-24 taperlock bush £3.20 (for motors with 24mm shafts)
1 x SP090/2 taper pulley £8.27
2 x SPA1707, SPA1732 or SPA1750 wedge belts number around 8.60 each
you only need two belts, the reason I have mentioned 3 sizes is that I'm using the SPA1707 with an internal circumference of 1707mm and the motor plate adjustment is right at the top and because I'm using a bigger pulley than the old motor I should have moved the motor to the left rather than using the same centre line, this means the belt needs to be a bit bigger. This may vary between models of chipmaster so is only relevent for early models.
Here's the motor mounted on the same plate as the old motor, but a lot smaller, the old motor was 1.5HP, the new is 2HP. Chipmasters had 1.5HP for college use and 3HP for undustrial use. Mine is ex-Leeds university before it went to a gas fitters workshop in Huddersfiled.
The reason the motor needs to be moved to the left a bit is so the drive belt doesn't catch the belt that drives the screwfeed as the pulley on the motor is bigger. The belt for the screwfeed is not on the next pic but you can see the pulley, I took it off to fettle an oil leak on the screwfeed driveshaft.
I got the motor and inverter from Inverter Drive Supermarket - based on price and the fact you could easily access all the info you needed on their web site, again prices may have gone up now. its a 2HP motor with a 24mm shaft and is nominally 1400rpm at 50Hz but is VFD friendly.
I worked out the speed of the old motor and the new set up and settled on a 90mm pulley as the ideal compromise. The old motor was 1440rpm, and the Kopps unit output range was 480 - 4320rpm. The chipmaster lathe speed range without gearbox is 350 - 3000 so there is a ratio of 1.37:1 input to output. The top pulley is 123.6mm OD so 118mm PCD.
The new VFD is 140 to 2800rpm so with a top speed of 2800, the lathe will go the following speeds at different pulley sizes, according to my calcs
60mm PC diameter pulley 188mm circumference = 2041 rpm @ 2800 motor speed
80mm PC diameter pulley 251mm circumference = 2725 rpm @ 2800 motor speed
85mm PC diameter pulley 267mm circumference = 2898 rpm @ 2800 motor speed
90mm PC diameter pulley 283mm circumference = 3072 rpm @ 2800 motor speed
1 x MAQ90L4 B3 Marelli - 1.5kW (2HP) 230V/400V IE2 3ph 4 Pole AC Motor for Speed Control - B3 Foot Mounting £106
FR-D720S-070-EC Mitsubishi D720S - 1.5kW (or 1.1kW) 230V 1ph to 3ph AC Inverter Drive Speed Controller £158.80
C3P15-M4M20-3 3 Phase Power Cable 1.5mm2 with M4 Rings and M20 Gland - 3m Length ££10.60
I bought the screened cable becuase it made the installation easier and I didn't want to interfere with Radio 6 music
I fed it around the back of the lathe through the existing bakelite junction box then through into the underneath of the lathe.
Here's pics of motor plate and inverter
I also bought a controller from Newton Tesla to fit on the top of the lathe, I made a small bracket out of aluminium, could do with a bit of extra strength behind it but it works fine,
Netwon Tesla controller £66 on ebay
Here's pics of the controller, the motor and lathe is very quiet, the fan on the inverter is louder
Cheers
Andy
I decided to swap out mine and replace the motor with a more modern 3 phase motor and inverter as I bought the lathe quite cheap and thought it was worth the investment.
There are various configurations with the variator on the end of the motor or seperate, see lathes.co.uk for details.
My chipmaster was an early one with the variator on the end, here's a pic of the old motor and variator being extracted by mounting it on a pallet truck with some timber strapped to it.
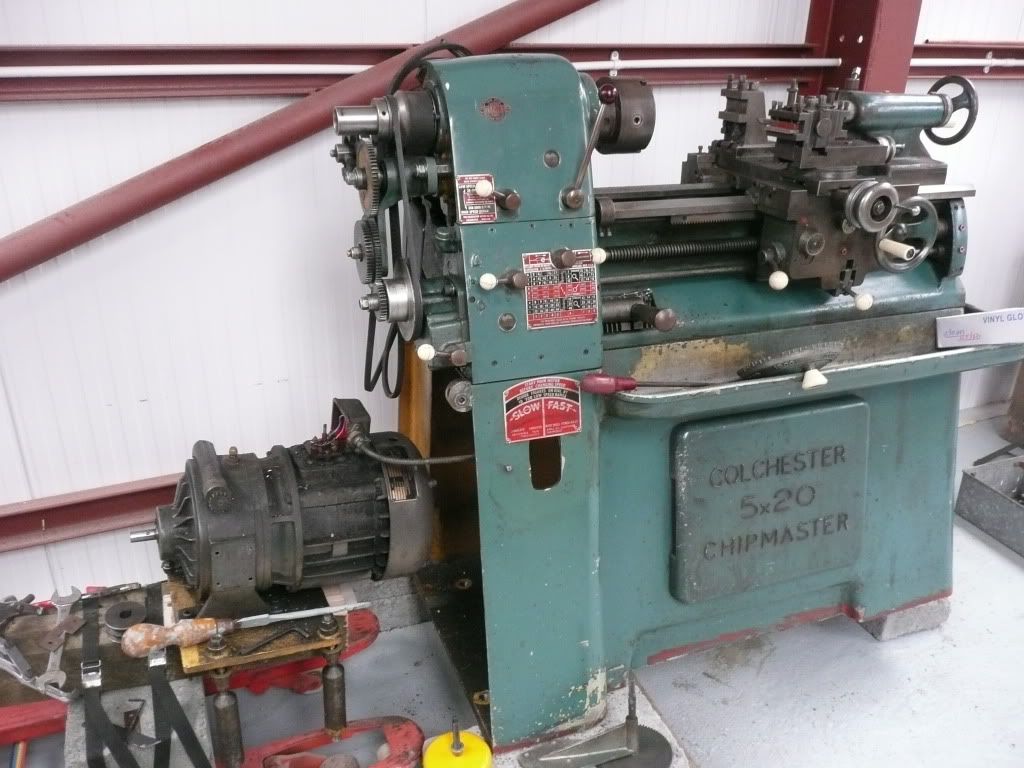
Here's the list of parts used from Bearing Boys for the pulley and belts, I did this about 10 months ago so prices may have changed
1 x 1108-24 taperlock bush £3.20 (for motors with 24mm shafts)
1 x SP090/2 taper pulley £8.27
2 x SPA1707, SPA1732 or SPA1750 wedge belts number around 8.60 each
you only need two belts, the reason I have mentioned 3 sizes is that I'm using the SPA1707 with an internal circumference of 1707mm and the motor plate adjustment is right at the top and because I'm using a bigger pulley than the old motor I should have moved the motor to the left rather than using the same centre line, this means the belt needs to be a bit bigger. This may vary between models of chipmaster so is only relevent for early models.
Here's the motor mounted on the same plate as the old motor, but a lot smaller, the old motor was 1.5HP, the new is 2HP. Chipmasters had 1.5HP for college use and 3HP for undustrial use. Mine is ex-Leeds university before it went to a gas fitters workshop in Huddersfiled.
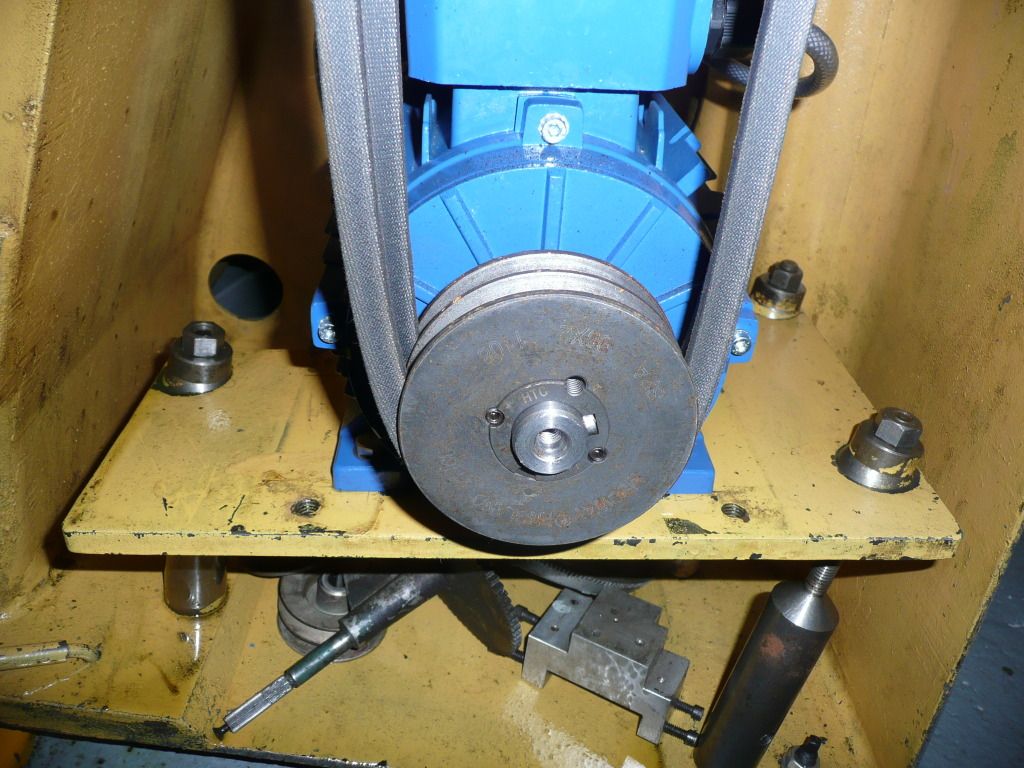
The reason the motor needs to be moved to the left a bit is so the drive belt doesn't catch the belt that drives the screwfeed as the pulley on the motor is bigger. The belt for the screwfeed is not on the next pic but you can see the pulley, I took it off to fettle an oil leak on the screwfeed driveshaft.
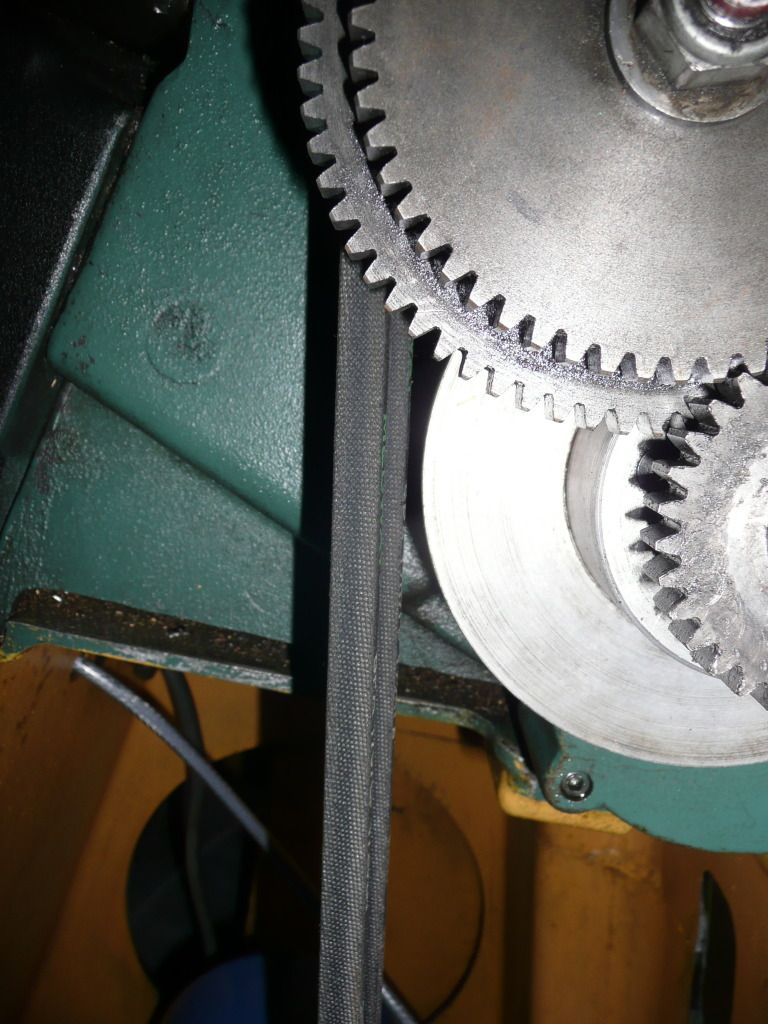
I got the motor and inverter from Inverter Drive Supermarket - based on price and the fact you could easily access all the info you needed on their web site, again prices may have gone up now. its a 2HP motor with a 24mm shaft and is nominally 1400rpm at 50Hz but is VFD friendly.
I worked out the speed of the old motor and the new set up and settled on a 90mm pulley as the ideal compromise. The old motor was 1440rpm, and the Kopps unit output range was 480 - 4320rpm. The chipmaster lathe speed range without gearbox is 350 - 3000 so there is a ratio of 1.37:1 input to output. The top pulley is 123.6mm OD so 118mm PCD.
The new VFD is 140 to 2800rpm so with a top speed of 2800, the lathe will go the following speeds at different pulley sizes, according to my calcs

60mm PC diameter pulley 188mm circumference = 2041 rpm @ 2800 motor speed
80mm PC diameter pulley 251mm circumference = 2725 rpm @ 2800 motor speed
85mm PC diameter pulley 267mm circumference = 2898 rpm @ 2800 motor speed
90mm PC diameter pulley 283mm circumference = 3072 rpm @ 2800 motor speed
1 x MAQ90L4 B3 Marelli - 1.5kW (2HP) 230V/400V IE2 3ph 4 Pole AC Motor for Speed Control - B3 Foot Mounting £106
FR-D720S-070-EC Mitsubishi D720S - 1.5kW (or 1.1kW) 230V 1ph to 3ph AC Inverter Drive Speed Controller £158.80
C3P15-M4M20-3 3 Phase Power Cable 1.5mm2 with M4 Rings and M20 Gland - 3m Length ££10.60
I bought the screened cable becuase it made the installation easier and I didn't want to interfere with Radio 6 music

Here's pics of motor plate and inverter
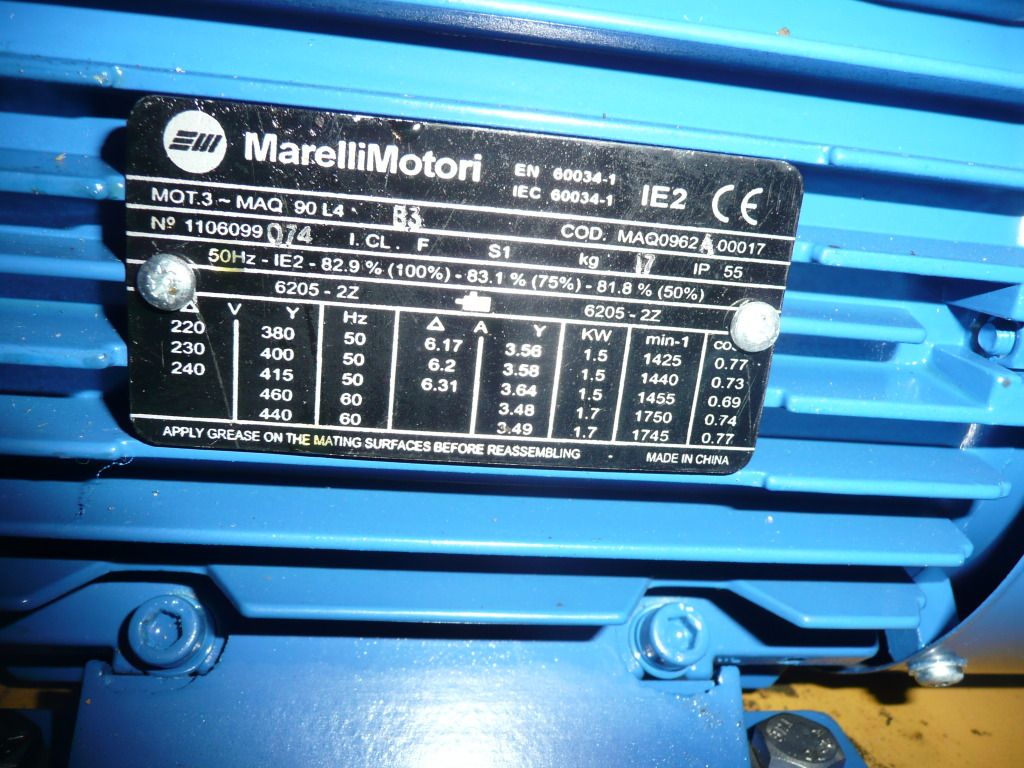
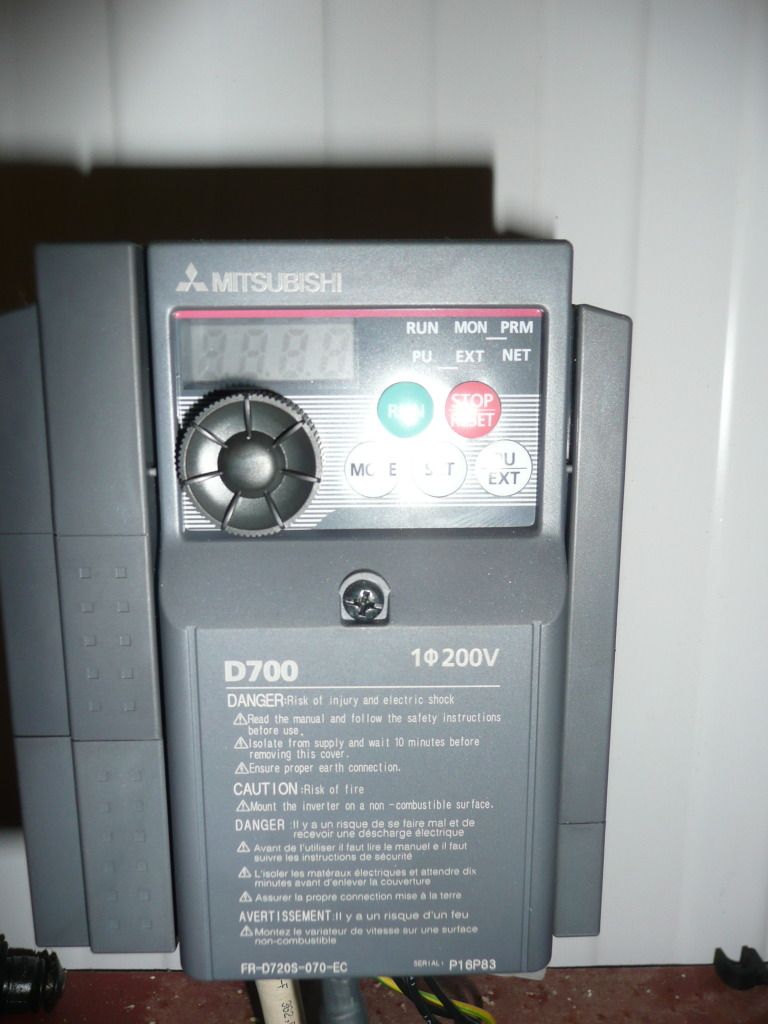
I also bought a controller from Newton Tesla to fit on the top of the lathe, I made a small bracket out of aluminium, could do with a bit of extra strength behind it but it works fine,
Netwon Tesla controller £66 on ebay
Here's pics of the controller, the motor and lathe is very quiet, the fan on the inverter is louder

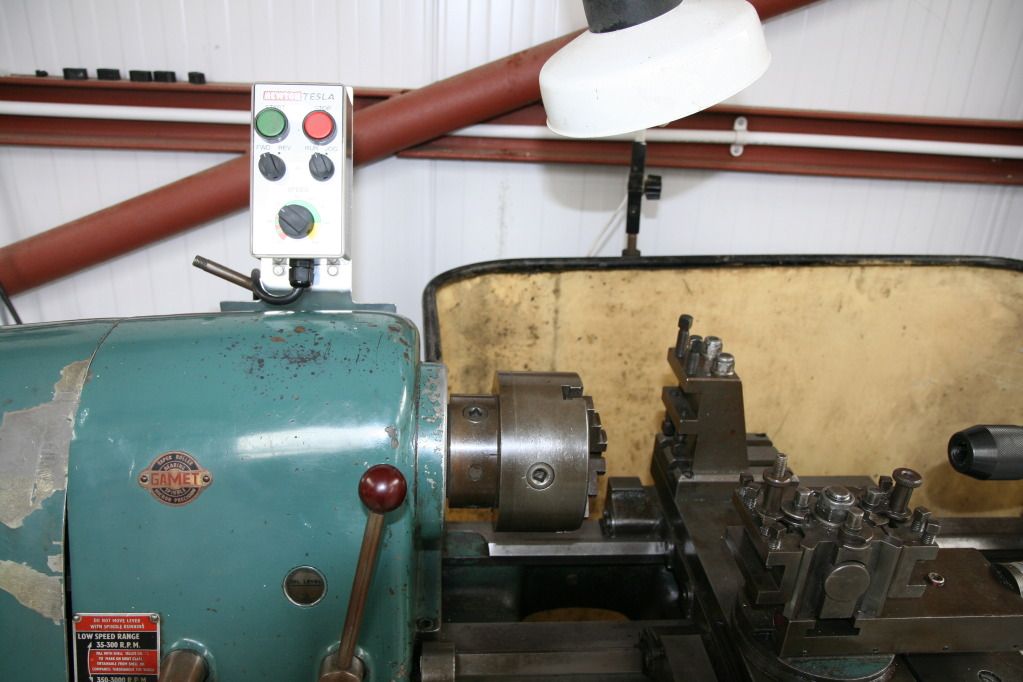
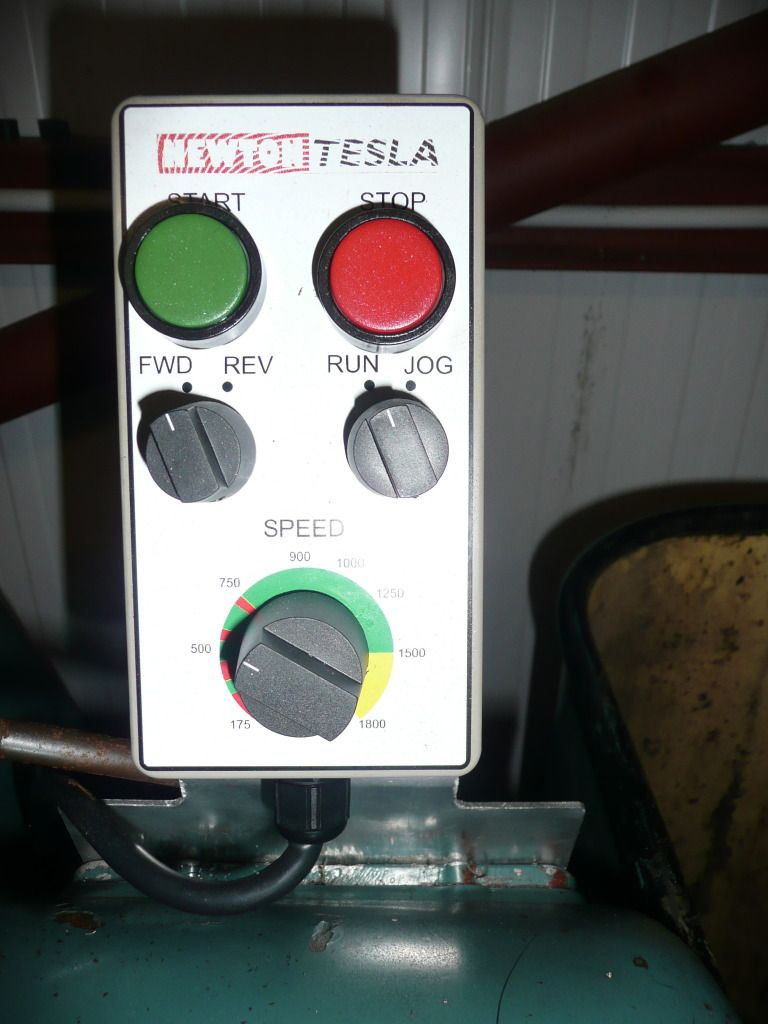
Cheers
Andy