northwest
Searching for the Holy Grail.........
- Messages
- 6,360
- Location
- Manchester UK
I need to install a Way Lube system to my recently acquired small CNC Mill. This machine has had quite a colourful and chequered history and I have known the machine for a good few years before it came into my possession.
I have started to learn my way around it and I built an enclosure so that I could use flood coolant. That was the catalyst to cause the machine to display it's final flaw,no waylube system. My efforts of squirting a bit of hydraulic oil onto the surfaces just weren't cutting it and the ways were starting to bind.
I looked at it and considered the options, reality was, take it apart, completely. I know, we look for the easier, softer options but it wasn't going to work; it needed to be dismantled completely. I needed the base on the big Mill so I could machine oil channels into it and drill some holes for the fittings.
As they say, a picture paints a thousand word, this is what it looked like when I had removed the covers:
I discovered the ballscrews were not zero backlash and they were tiny, 8mm! So I immediately decided to upgrade them to the biggest I could realistically fit and it was determined that a step up to 10mm diameter ball screw. I also decided that twin angular contact bearings were needed if I was to make a job of it:
As it is the holidays my usual method of paint removal wasn't available to me so I knocked up a makeshift box lined with poly bags and some dichloromethane, 24 hours later, I had this and it was ready to go:
Using a 4mm carbide ball end mill I started the oilways. I drilled and tapped 8x1mm for the oil fittings and decided to use the biggest I had because once this is all together it will be a nightmare to swap them;
I flipped it over and machined the spot where the fittings are going to go, if it looks right it probably is:
This clearly shows the difference in size of the new bearings. I decided to go with a twin angular contact bearings and just suffer the need to make new bearing carriers, I will do those once the new ball nuts arrive and I have installed them and I am sure about the centres staying the same. I might need to move the centre line of the ball screws so best wait, I hate "trial runs".
I drilled into the side of the X axis on both sides and joined those canals from the top to lead the oil straight into the way channels. I must have used the same piece of string to measure with as they broke through perfectly on bothsides:
Coat of primer and the first coat of Tractol before tea:
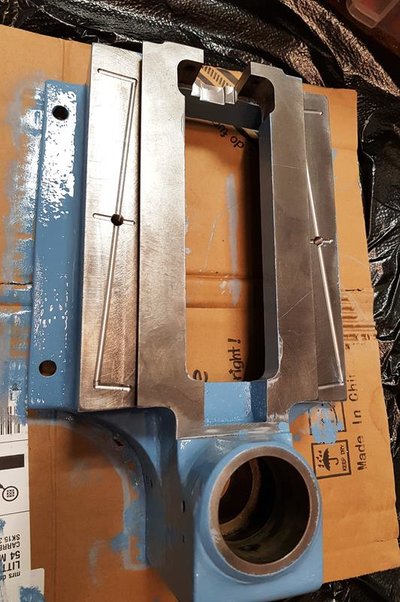
I have started to learn my way around it and I built an enclosure so that I could use flood coolant. That was the catalyst to cause the machine to display it's final flaw,no waylube system. My efforts of squirting a bit of hydraulic oil onto the surfaces just weren't cutting it and the ways were starting to bind.
I looked at it and considered the options, reality was, take it apart, completely. I know, we look for the easier, softer options but it wasn't going to work; it needed to be dismantled completely. I needed the base on the big Mill so I could machine oil channels into it and drill some holes for the fittings.
As they say, a picture paints a thousand word, this is what it looked like when I had removed the covers:
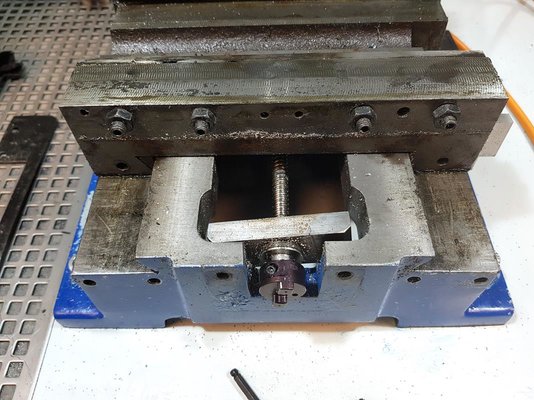
I discovered the ballscrews were not zero backlash and they were tiny, 8mm! So I immediately decided to upgrade them to the biggest I could realistically fit and it was determined that a step up to 10mm diameter ball screw. I also decided that twin angular contact bearings were needed if I was to make a job of it:
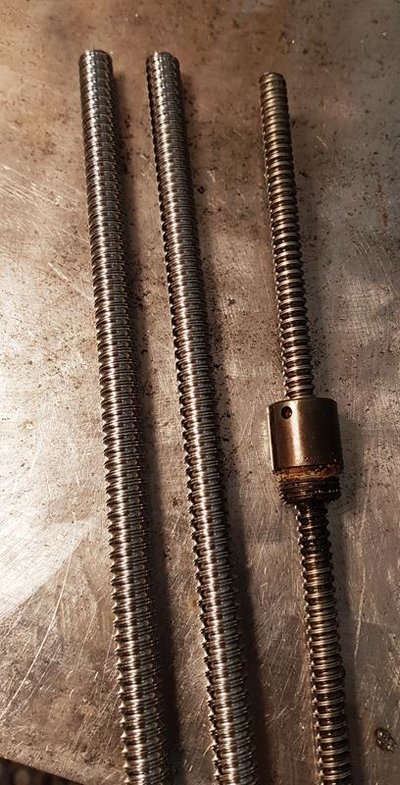
As it is the holidays my usual method of paint removal wasn't available to me so I knocked up a makeshift box lined with poly bags and some dichloromethane, 24 hours later, I had this and it was ready to go:
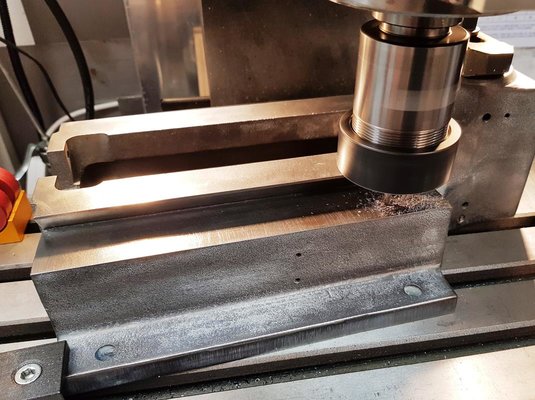
Using a 4mm carbide ball end mill I started the oilways. I drilled and tapped 8x1mm for the oil fittings and decided to use the biggest I had because once this is all together it will be a nightmare to swap them;
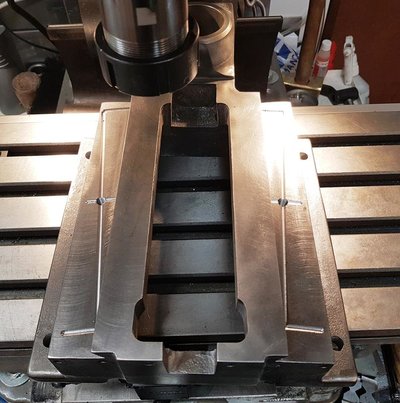
I flipped it over and machined the spot where the fittings are going to go, if it looks right it probably is:
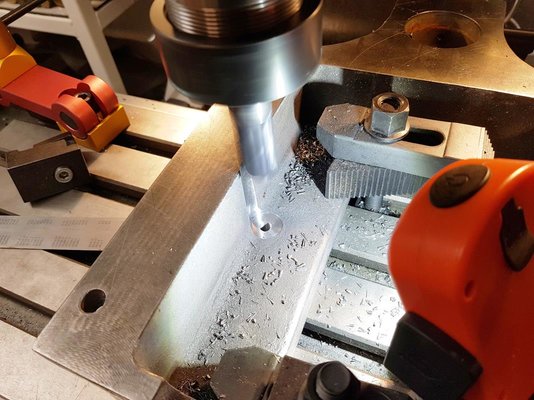
This clearly shows the difference in size of the new bearings. I decided to go with a twin angular contact bearings and just suffer the need to make new bearing carriers, I will do those once the new ball nuts arrive and I have installed them and I am sure about the centres staying the same. I might need to move the centre line of the ball screws so best wait, I hate "trial runs".
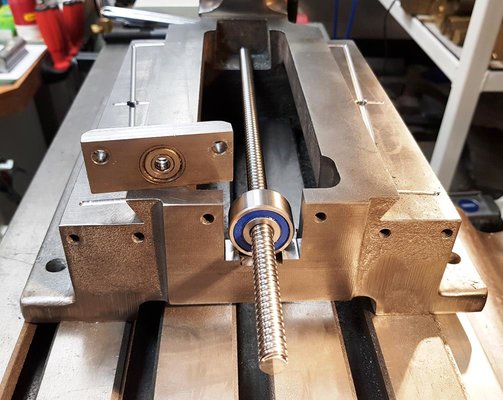
I drilled into the side of the X axis on both sides and joined those canals from the top to lead the oil straight into the way channels. I must have used the same piece of string to measure with as they broke through perfectly on bothsides:
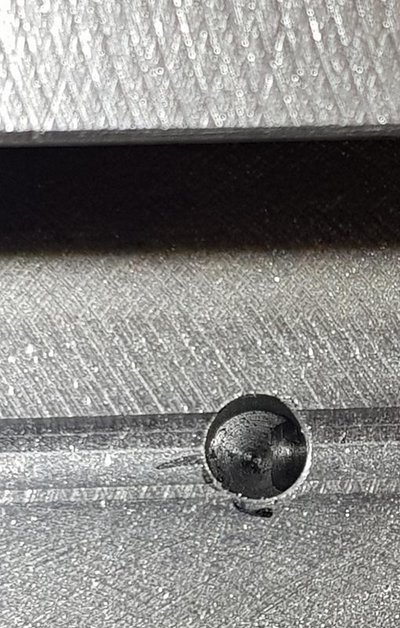
Coat of primer and the first coat of Tractol before tea:
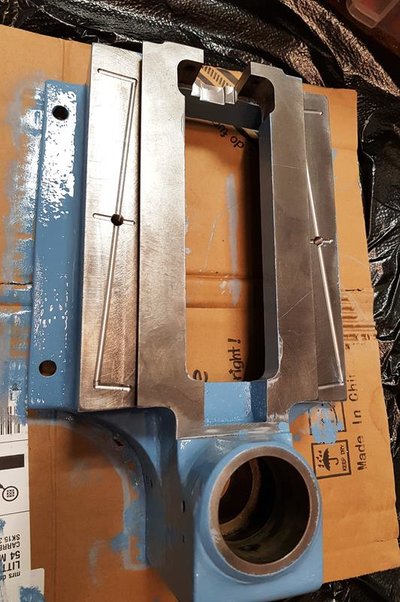