Ton-up
Member
- Messages
- 2,292
- Location
- Essex, England.
Two parts to this, the first part I'm posting is in the hope it may help other R-tec plasma owners, although I am not sure that I am correct!
I recently put a non-working R-tec 40amp plasma torch on the forum in the freebies section. It was there because when our p50hf plasma was purchased by my employer it worked fine, but very quickly it started to cause trouble, working very intermittently and just got put in the corner and forgot about.
I got my hands on it and found that although air always came out the torch when the torch was switched, there would be a short hf arc or nothing at all that or a short burst of arc then nothing.
I spoke to r-tec who diagnosed a torch problem. They told me that the p50hf torches were changed to 70 amp torches just after we bought our one as they found 40amp ones were not man enough!
Pondy wanted the torch head only, so I cut it off, and I took the lead and plug apart for my scrap bin but I found this on opening the plug-
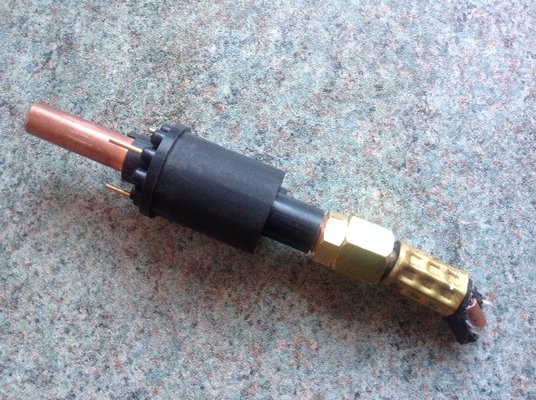
The copper tube that goes into the machine is carries both electric and air. The lead to the torch is basically an air hose with a copper cable inside and a cople of control wires. These are connected together with the brass nuts and fittings shown here -
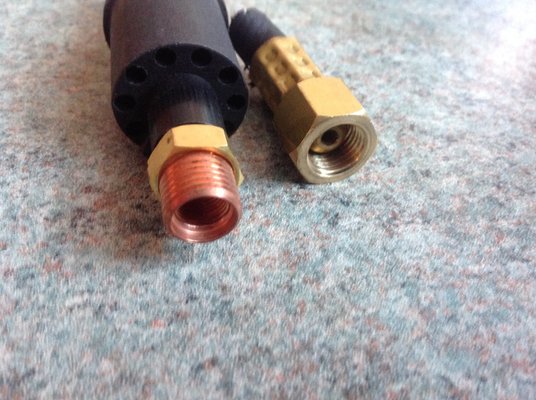
Now, I believe that all the problems were due to these fittings not being tight. This can be seen in the pic as the crimped section is drooping. There was probably .5 to 1mm of slack in the fitting, the locking nut being done up tight behind the main nut.
I cannot see any reason to have the fitting loose as air pressure would escape around the cone, reducing the true pressure seen at the torch and the air may also hold the two parts of the fitting apart to stop contact between the two parts. There appears to be arcing between the nut and around the stem of the fitting.
I don't think the fitting was set loose in assembly to allow movement of the lead, it would have an 'O' ring or simular and the control wires would also need to turn.
So if you have a problem with your torch, it may pay to check this fitting is tight.
Further to my problems, the new R-tec 70amp torch has blown a hole in the side. Tried it a few times and the machine worked fine, so started cutting a 24" length of 10mm plate. Got about 18" in and there was a pop and a jet of sparks and air shot out the side! Like in this recent post-
https://www.mig-welding.co.uk/forum/threads/r-tech-p30c-cut-quality.87486/page-3
Does anyone know why this has happened? Another call to R-tec on monday..........
I recently put a non-working R-tec 40amp plasma torch on the forum in the freebies section. It was there because when our p50hf plasma was purchased by my employer it worked fine, but very quickly it started to cause trouble, working very intermittently and just got put in the corner and forgot about.
I got my hands on it and found that although air always came out the torch when the torch was switched, there would be a short hf arc or nothing at all that or a short burst of arc then nothing.
I spoke to r-tec who diagnosed a torch problem. They told me that the p50hf torches were changed to 70 amp torches just after we bought our one as they found 40amp ones were not man enough!
Pondy wanted the torch head only, so I cut it off, and I took the lead and plug apart for my scrap bin but I found this on opening the plug-
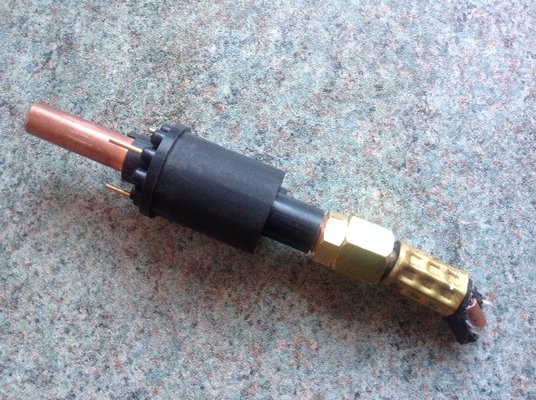
The copper tube that goes into the machine is carries both electric and air. The lead to the torch is basically an air hose with a copper cable inside and a cople of control wires. These are connected together with the brass nuts and fittings shown here -
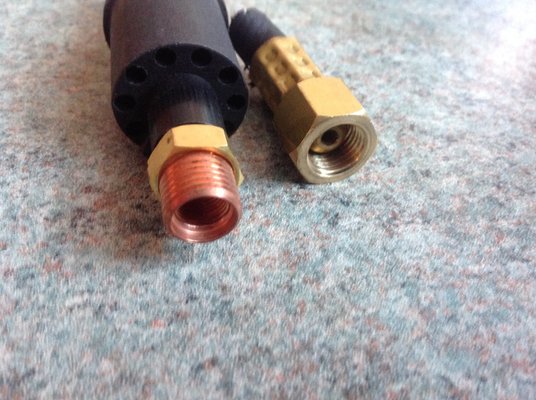
Now, I believe that all the problems were due to these fittings not being tight. This can be seen in the pic as the crimped section is drooping. There was probably .5 to 1mm of slack in the fitting, the locking nut being done up tight behind the main nut.
I cannot see any reason to have the fitting loose as air pressure would escape around the cone, reducing the true pressure seen at the torch and the air may also hold the two parts of the fitting apart to stop contact between the two parts. There appears to be arcing between the nut and around the stem of the fitting.
I don't think the fitting was set loose in assembly to allow movement of the lead, it would have an 'O' ring or simular and the control wires would also need to turn.
So if you have a problem with your torch, it may pay to check this fitting is tight.
Further to my problems, the new R-tec 70amp torch has blown a hole in the side. Tried it a few times and the machine worked fine, so started cutting a 24" length of 10mm plate. Got about 18" in and there was a pop and a jet of sparks and air shot out the side! Like in this recent post-
https://www.mig-welding.co.uk/forum/threads/r-tech-p30c-cut-quality.87486/page-3
Does anyone know why this has happened? Another call to R-tec on monday..........