I've just bought my first TIG welder, a Giant WSE200, yeah I know, chinese tat, or whatever you want to call it! I've bought it with the intention of making a manifold (thick mild steel) and an exhaust system (stainless steel), then move on to some aluminium work for boost pipes, washer bottle etc. hence the AC/DC model rather than DC only.
The welder arrived on Tuesday, being impatient I went to halfords for a bottle of argon, opened it up fully and melted some stainless tube I had laying around, here are the results if you're interested?


That was my first ever attempt, with no filler rods, disposable argon bottle, welder in the living room with the leads going outside! Some of the bits in the 2nd photo are my dad's attempts, I couldn't buy a TIG and not let him have a go!
So, today I got a "proper" bottle of argon from the nearest Hobyweld supplier, had a bit of a practice tonight first up, a bit of mild steel exhaust, the bit of melted pipe to the right of the photo was my dad's lack of control, basically stood on the pedal and held the torch too far away, everything else is my doing, including the melted bit in the middle with a bead over the top where I tried turning the amps up to see what happened!

Next is some ~3mm mild steel, I dipped the tip of the tungsten when I tacked it, I then tacked the other side before I re-ground the tip but didn't grind the weld off, I think that's why the weld is dark?
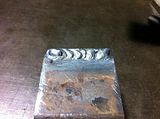
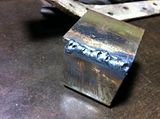
I'm not sure about the holes in the weld, what have I done wrong here? I know none of the welds so far have been the best but these are my first attempts, I'm sure I'll get better at it!
Then I switched it onto AC and had a crack at some aluminium, ~3mm, all I managed to do is heat it up, I think the problem here is I didn't clean it properly?

All I did was file it then sand it, I don't have a stainless wire brush so couldn't really do anything else, what I did notice while trying to weld the aluminium was the arc seemed to be dancing all over the place, rather than being a smooth arc.
This was all done with the grey tipped tungsten that came with the welder, is there such a thing as bad quality tungsten? Will I benefit from getting some "good" tungsten? I was planning on getting some red tipped for mild and stainless, is this a good move?
Tomorrow I'm planning on making a de-cat pipe for my brother out of the old flanges from the cat and the exhaust pipe from the above photos, I'll have a bit more practice first, if it doesn't improve I'll get the MIG out and do it with that, but I'd prefer to do it with the TIG, any pointers?
The welder arrived on Tuesday, being impatient I went to halfords for a bottle of argon, opened it up fully and melted some stainless tube I had laying around, here are the results if you're interested?


That was my first ever attempt, with no filler rods, disposable argon bottle, welder in the living room with the leads going outside! Some of the bits in the 2nd photo are my dad's attempts, I couldn't buy a TIG and not let him have a go!
So, today I got a "proper" bottle of argon from the nearest Hobyweld supplier, had a bit of a practice tonight first up, a bit of mild steel exhaust, the bit of melted pipe to the right of the photo was my dad's lack of control, basically stood on the pedal and held the torch too far away, everything else is my doing, including the melted bit in the middle with a bead over the top where I tried turning the amps up to see what happened!

Next is some ~3mm mild steel, I dipped the tip of the tungsten when I tacked it, I then tacked the other side before I re-ground the tip but didn't grind the weld off, I think that's why the weld is dark?
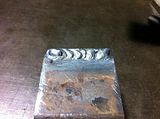
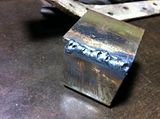
I'm not sure about the holes in the weld, what have I done wrong here? I know none of the welds so far have been the best but these are my first attempts, I'm sure I'll get better at it!
Then I switched it onto AC and had a crack at some aluminium, ~3mm, all I managed to do is heat it up, I think the problem here is I didn't clean it properly?

All I did was file it then sand it, I don't have a stainless wire brush so couldn't really do anything else, what I did notice while trying to weld the aluminium was the arc seemed to be dancing all over the place, rather than being a smooth arc.
This was all done with the grey tipped tungsten that came with the welder, is there such a thing as bad quality tungsten? Will I benefit from getting some "good" tungsten? I was planning on getting some red tipped for mild and stainless, is this a good move?
Tomorrow I'm planning on making a de-cat pipe for my brother out of the old flanges from the cat and the exhaust pipe from the above photos, I'll have a bit more practice first, if it doesn't improve I'll get the MIG out and do it with that, but I'd prefer to do it with the TIG, any pointers?