Not sure if this is the right section but a mate of mine needs about 50 off little metal parts for motorbikes making. Pictures below. I have an original but it’s a rare thing so looking for small fab shop? They’re only about 48mm long, 1mm mild by the look of it. Anyone like to quote? Bend looks a bit tricky.
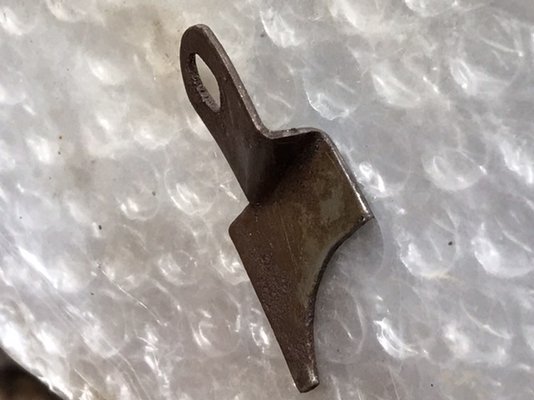


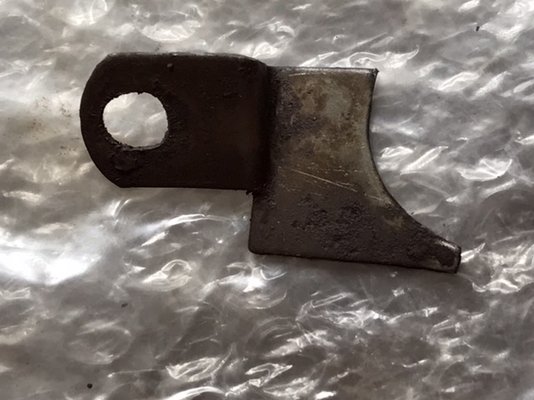
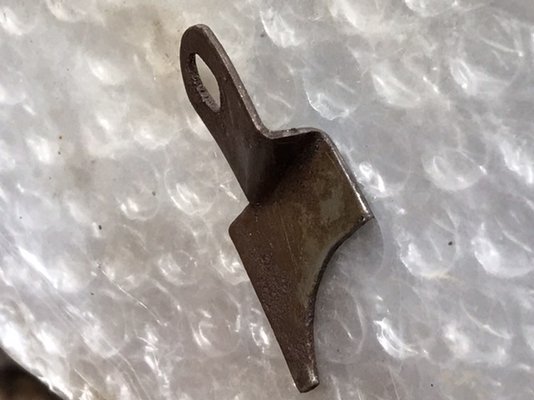