Misterg
Member
- Messages
- 1,455
- Location
- North Wales
I got myself a Sherman 206P AC/DC TIG set before the drawbridge came up at the end of last year, but unfortunately, the pedal didn't make it through. I've made a pedal mechanism which seems to work very nicely and want to make a cover to go over it. For a bit of practice, as much as anything else, I decided to try and weld one up from 3mm aluminium.
I did a couple of tests but welding 3mm:
Top one was a slightly hesitant 125 amps, bottom 130 amps with slower travel & pedal to the floor for most of the weld.
(AC 80Hz, 32% EP, 2.4mm 2%La tungsten, 6LPM Ar in each case)
Back sides:
Q1 - what is "normal" for TIG welding this thickness ali? Should there be penetration visible for the full length of the weld?
I cut a section from it, and while there was a definite groove that I wouldn't like in anything structural, I decided it was good enough for the job in hand:
Sides tacked together:
Welding the first seam went OK (IMHO!)
Blew a hole in the second (trying to be more bold and get better penetration|)
I thought the first side wasn't too bad inside:
Second side looked decidedly crummy.
Bit (quite a bit) of filing:
Fit-up poor in both cases.
Continued...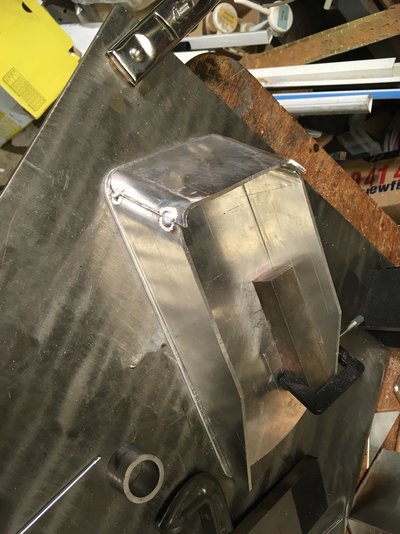
I did a couple of tests but welding 3mm:
Top one was a slightly hesitant 125 amps, bottom 130 amps with slower travel & pedal to the floor for most of the weld.
(AC 80Hz, 32% EP, 2.4mm 2%La tungsten, 6LPM Ar in each case)
Back sides:
Q1 - what is "normal" for TIG welding this thickness ali? Should there be penetration visible for the full length of the weld?
I cut a section from it, and while there was a definite groove that I wouldn't like in anything structural, I decided it was good enough for the job in hand:
Sides tacked together:
Welding the first seam went OK (IMHO!)
Blew a hole in the second (trying to be more bold and get better penetration|)
I thought the first side wasn't too bad inside:
Second side looked decidedly crummy.
Bit (quite a bit) of filing:
Fit-up poor in both cases.
Continued...
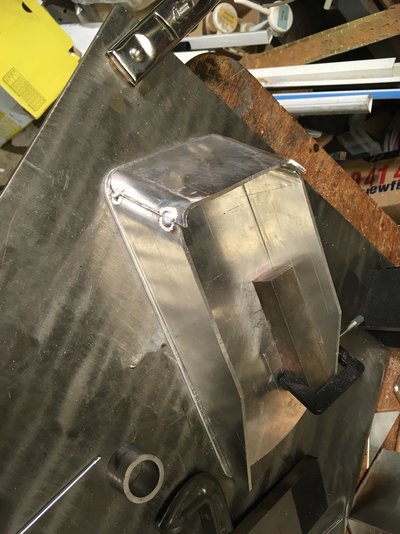