BenL
New Member
- Messages
- 26
- Location
- Estepona, Spain
Hi all,
This would be my first post here, I have read of LOT of posts and found some great advice on here so thanks in advance for any help.
I am working on a VW Beetle and part of the chassis is not in good shape. One specific section that needs to be replaced extends out from the main part of the chassis (not my car below) both the top and bottom parts are rusted.
The part you see also has a bottom section, that is rusted also. My question is should I do a straight cut through both as per below (bottom section not shown) or stagger the cuts so the new welded piece is not one line?
I am leaning towards staggering the cut between the top and the bottom sections, what other options are there?
This would be my first post here, I have read of LOT of posts and found some great advice on here so thanks in advance for any help.
I am working on a VW Beetle and part of the chassis is not in good shape. One specific section that needs to be replaced extends out from the main part of the chassis (not my car below) both the top and bottom parts are rusted.
The part you see also has a bottom section, that is rusted also. My question is should I do a straight cut through both as per below (bottom section not shown) or stagger the cuts so the new welded piece is not one line?
I am leaning towards staggering the cut between the top and the bottom sections, what other options are there?
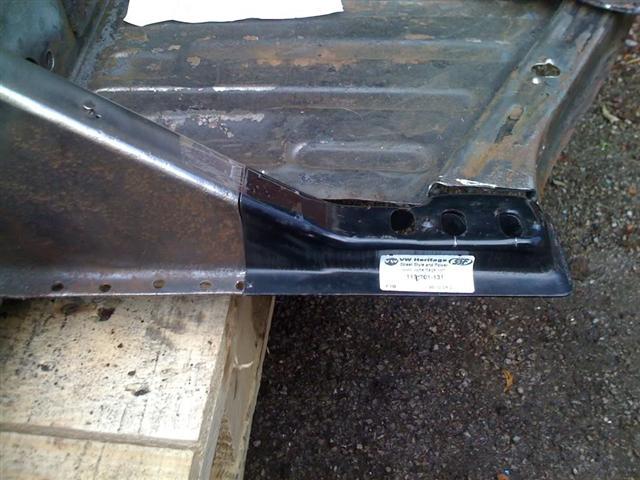