Mark Davison
Member
- Messages
- 169
- Location
- London
I recently bought a new cross slide lead nut for my bantam. It has eliminate pretty much all of the play but seems to have revealed another issue. The lead screw appears bent and the end wonders when rotated. Only the leadscrew shaft itself is straight and true.
The Bantam's cross slide lead screw is in two parts, an inner shaft which has the lead screw thread and a male spline on the other. The male spline slides inside a hollow shaft with a corresponding female spline. The hollow shaft incorporates the drive gear and a male spline at the other end for the micrometer dial. This hollow shaft then runs inside a bush in the block that mounts to the apron. I guess this is to enable it to be disconnected when used with a taper turning attachment.
Anyway, the 'wobble' appears to be a result of the O/D of the hollow outer shaft not being concentric with the female splined inner bore. The linked videos show the issue.
The reslt is tight spots when turning the leadscrew as the cross slide nears the micrometer dial end of the travel.
The question is, how would you go about correcting this? It is tight enough that it is making the new nut unusable in the last one or two inches of cross slide travel. I assume Taking a skim off the OD of the outer hollow shaft whilst mounted on the innershaft with that between centres as per video (and re-bushing the bearing/mounting block) will no doubt affect the micrometer dials fit on the hollow shafts male splines? Not that I can use the lathe without the cross slide leadscrew in it anyway.
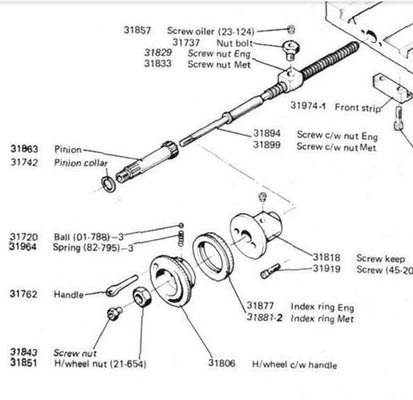
The Bantam's cross slide lead screw is in two parts, an inner shaft which has the lead screw thread and a male spline on the other. The male spline slides inside a hollow shaft with a corresponding female spline. The hollow shaft incorporates the drive gear and a male spline at the other end for the micrometer dial. This hollow shaft then runs inside a bush in the block that mounts to the apron. I guess this is to enable it to be disconnected when used with a taper turning attachment.
Anyway, the 'wobble' appears to be a result of the O/D of the hollow outer shaft not being concentric with the female splined inner bore. The linked videos show the issue.
The reslt is tight spots when turning the leadscrew as the cross slide nears the micrometer dial end of the travel.
The question is, how would you go about correcting this? It is tight enough that it is making the new nut unusable in the last one or two inches of cross slide travel. I assume Taking a skim off the OD of the outer hollow shaft whilst mounted on the innershaft with that between centres as per video (and re-bushing the bearing/mounting block) will no doubt affect the micrometer dials fit on the hollow shafts male splines? Not that I can use the lathe without the cross slide leadscrew in it anyway.
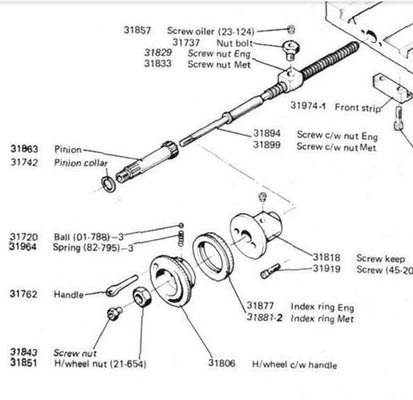