Cut the rest of the rotten inner sill out yesterday and started fitting the new panel, not a great fit as its slightly too short but it's hidden behind a deep flange so should be fine.
I hadn't realised what a time consuming job fitting the new panels is, still not finished on this one and I've got the kick panel patch to fit, a patch to make up on the floor and then the bottom of the door pillar and the outer sill itself.
My question is: what size holes should I drill for plug welding?
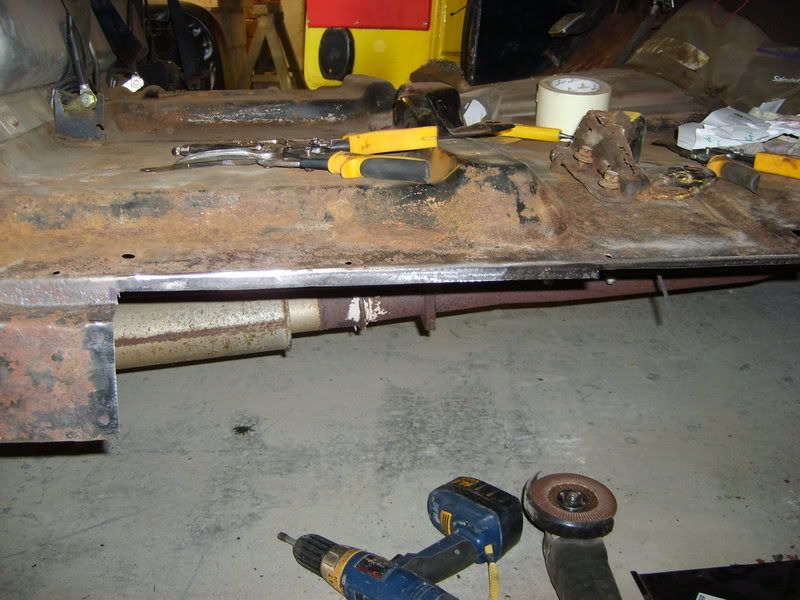
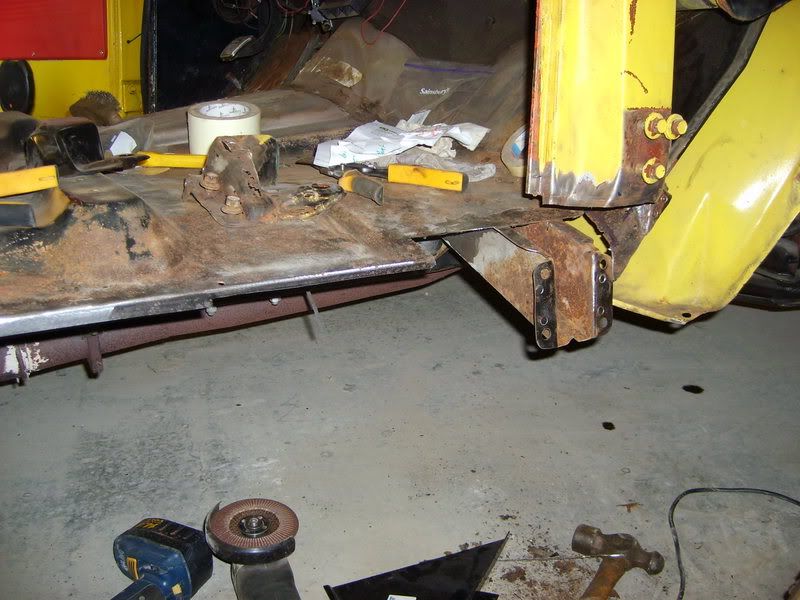
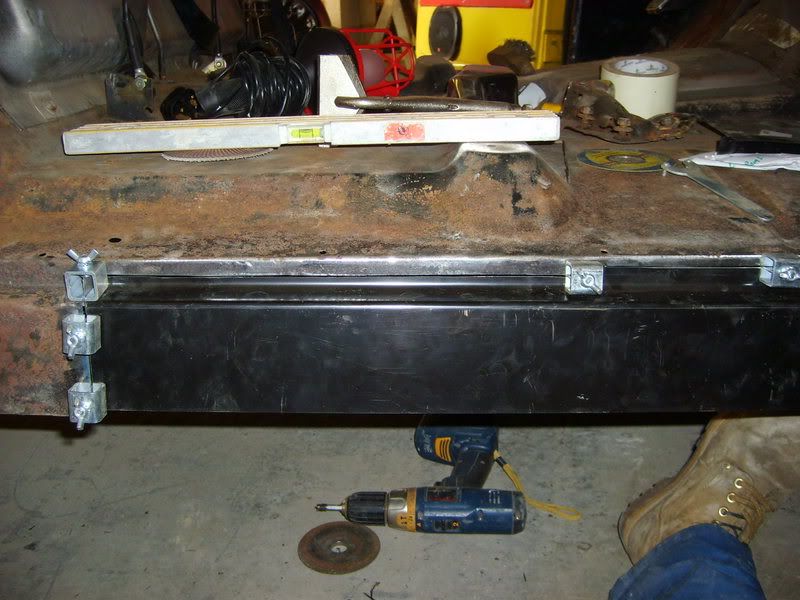
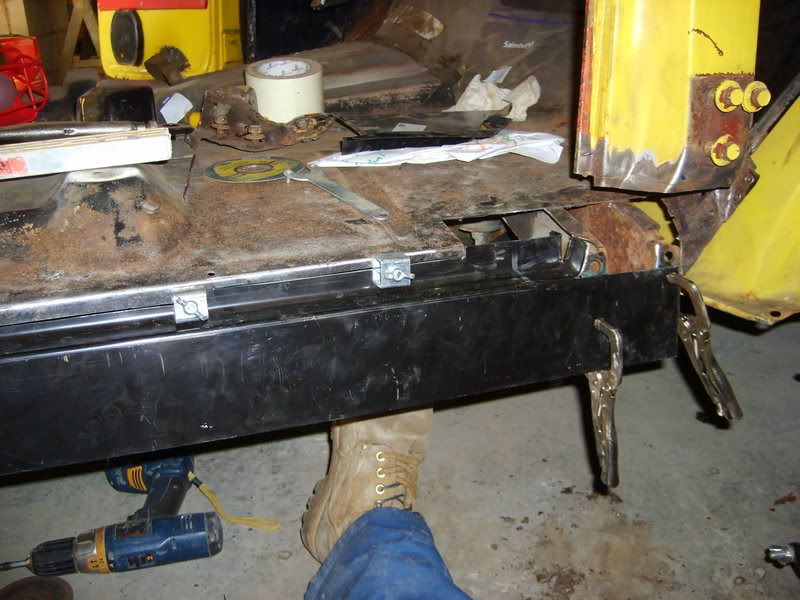
I hadn't realised what a time consuming job fitting the new panels is, still not finished on this one and I've got the kick panel patch to fit, a patch to make up on the floor and then the bottom of the door pillar and the outer sill itself.
My question is: what size holes should I drill for plug welding?