malcolm
& Clementine the Cat
- Messages
- 9,625
- Location
- Bedford UK
I've bought a lathe. It was cheap as it fell off a fork lift and some of the castings have broken.
Here's a pic of the worst bit:
I gather from other forums that it is possible to weld cast iron using ordinary mild steel wire so long as the cast iron isn't stress bearing.
My problem is I'm missing the rest of this casting. My plan is to make a new section using mild steel and weld it on.
Has anyone else tried this sort of botch? Any ideas on a better solution, or advice on how to go about this sort of thing?
Here's a pic of the worst bit:
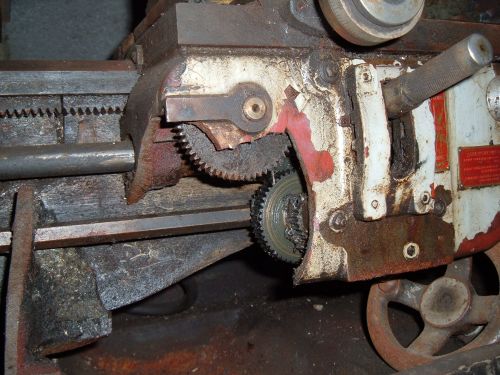
I gather from other forums that it is possible to weld cast iron using ordinary mild steel wire so long as the cast iron isn't stress bearing.
My problem is I'm missing the rest of this casting. My plan is to make a new section using mild steel and weld it on.
Has anyone else tried this sort of botch? Any ideas on a better solution, or advice on how to go about this sort of thing?