Mr Roo
Member
- Messages
- 597
- Location
- Edinburgh
Local firm asked me a few weeks ago to come in and give a hand for a wee while as they’re buying some new kit and need someone who’s savvy to get them started. Came at the right time as I’ve been furloughed on 100% salary and didn’t have any projects lined up!
(My name and number was passed along by a company I used to work for - pleased with that!)
it’s an agricultural(ish) company, and part of the job is making excavator brackets for picking up the various equipment for various machines.
previously, they’d been ordering in completed brackets, but the weld quality was... well, it was gash! so they decided to use this mob for supplying the plasma cut components, and then they’d weld them themselves. (Except, as with most “well thought out” plans, they forgot a vital component... the guy welding was a plant mechanic who could sortofweld. This is where I was supposed to come in!)
started last week, and the first thing I noticed was that the cut quality was terrible. Some of these plates were so far off the square they wouldn’t stand up - meaning it was taking a bit longer to get these brackets fabricated as there was loads of faffing about to do!
mentioned it to the owner who said this was why he’s bought a plasma cutter... but the excuse from the other company was pure gold:
“They’re not cut on the p*ss! They’re cut at an angle so you can get plenty of weld under them!”
Fella’s now bought an escco table and a hypertherm 200a cutter, so parts are coming in quicker and neater, and time is being saved all ‘round!
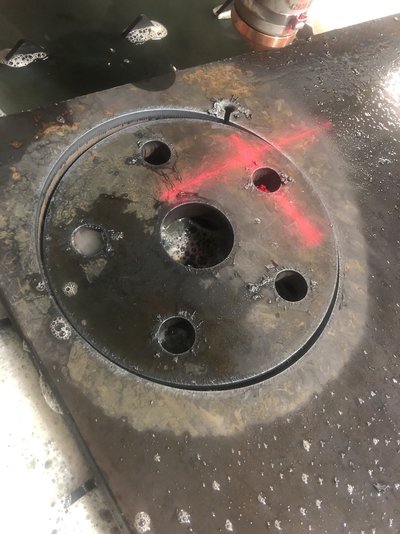
(My name and number was passed along by a company I used to work for - pleased with that!)
it’s an agricultural(ish) company, and part of the job is making excavator brackets for picking up the various equipment for various machines.
previously, they’d been ordering in completed brackets, but the weld quality was... well, it was gash! so they decided to use this mob for supplying the plasma cut components, and then they’d weld them themselves. (Except, as with most “well thought out” plans, they forgot a vital component... the guy welding was a plant mechanic who could sortofweld. This is where I was supposed to come in!)
started last week, and the first thing I noticed was that the cut quality was terrible. Some of these plates were so far off the square they wouldn’t stand up - meaning it was taking a bit longer to get these brackets fabricated as there was loads of faffing about to do!
mentioned it to the owner who said this was why he’s bought a plasma cutter... but the excuse from the other company was pure gold:
“They’re not cut on the p*ss! They’re cut at an angle so you can get plenty of weld under them!”

Fella’s now bought an escco table and a hypertherm 200a cutter, so parts are coming in quicker and neater, and time is being saved all ‘round!
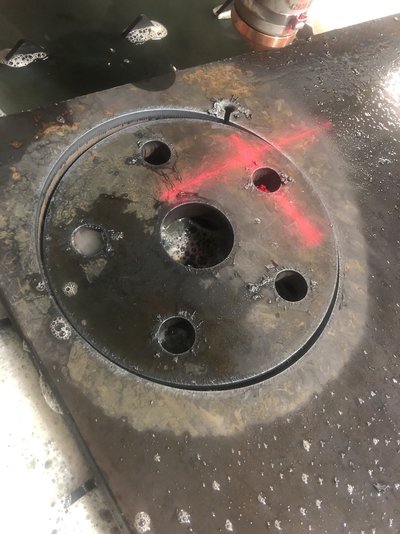