Pete.
Member
- Messages
- 14,880
- Location
- Kent, UK
Our lad went to change the top engine mount on his Golf, snapped off one of the bolts. The first I knew about it was when he phoned to say the bolt was snapped and the extractor was snapped off in in and could I do anything? I asked for a photo and when I saw it I knew it was going to be a tough one. It's a M12 x 1.25 stainless bolt screwed into a cast aluminium housing with about 35mm thread engagement. Nightmare combo. At least it was accessible.
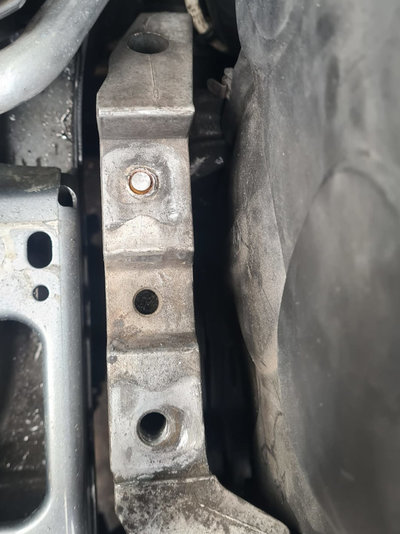
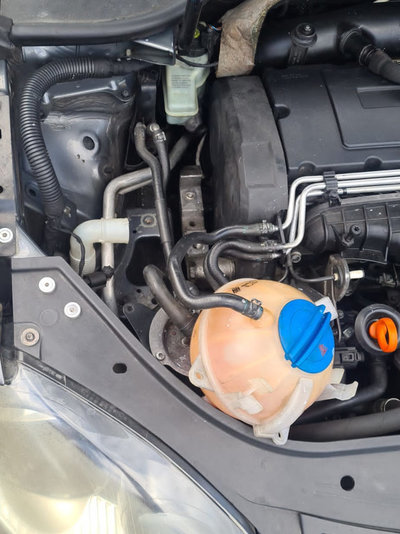
I have an old fire blanket that I tore a hole in the middle and put the hole over the part and used the blanket to protect the surroundings. First job was to remove the extractor. Popped a washer over it, gave it a squirt with the mig then put a M12 nut on top and welded that. Wound the extractor straight out.
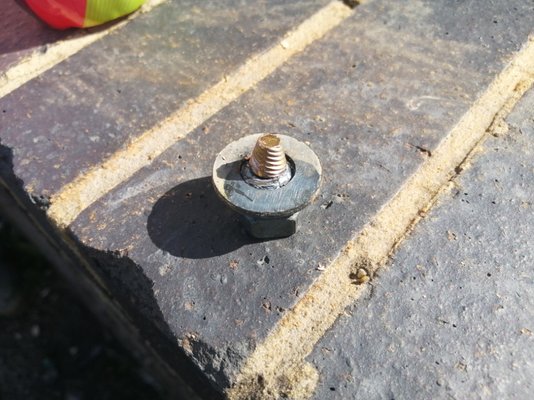
Next for the bolt. I filled the drilled end up with weld then tried the same trick by welding over a washer then a nut. It wrenched the nut off. Tried again, it pulled the weld out of the hole. Tried several times more, same result. Tried a bigger nut = more heat input, that sheared off. I figured that if I kept trying and trying I'd be pouring more heat into the ally housing and eventually it would let go. Turns out it took 9 attempts
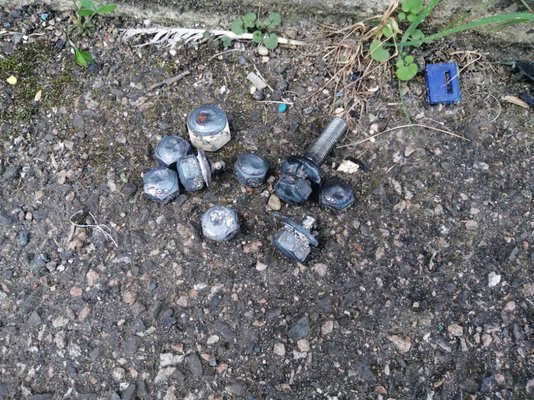
And the result - new bolt screws right in. To say that he was relieved is an understatement, because the next step was to drop the engine, remove the plate and put it in my milling machine.
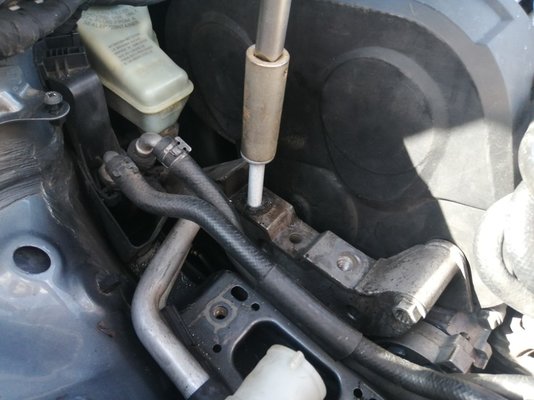
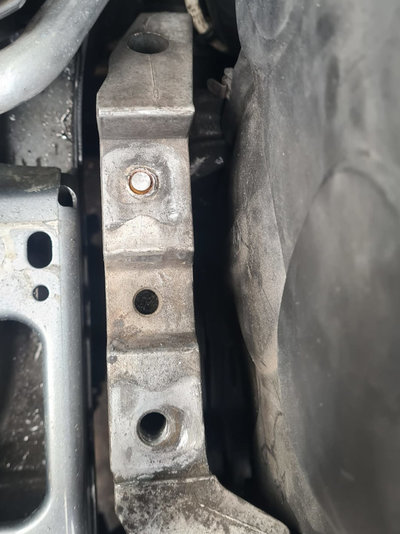
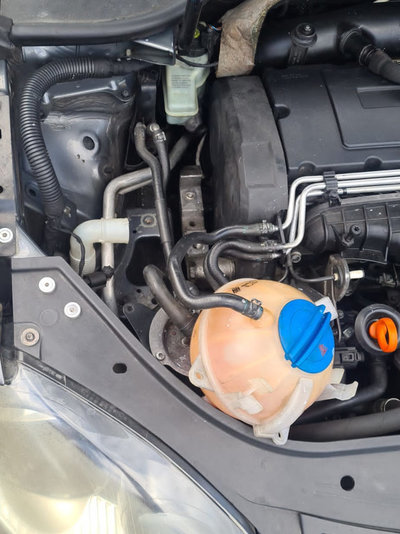
I have an old fire blanket that I tore a hole in the middle and put the hole over the part and used the blanket to protect the surroundings. First job was to remove the extractor. Popped a washer over it, gave it a squirt with the mig then put a M12 nut on top and welded that. Wound the extractor straight out.
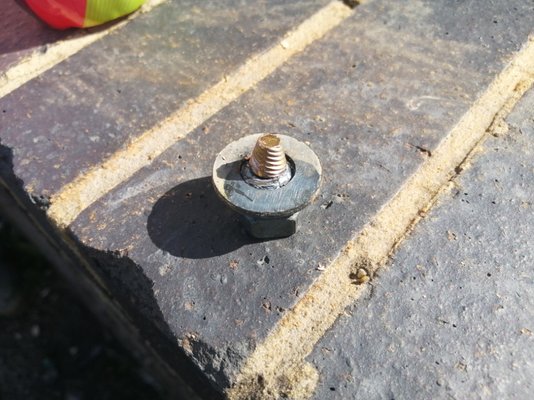
Next for the bolt. I filled the drilled end up with weld then tried the same trick by welding over a washer then a nut. It wrenched the nut off. Tried again, it pulled the weld out of the hole. Tried several times more, same result. Tried a bigger nut = more heat input, that sheared off. I figured that if I kept trying and trying I'd be pouring more heat into the ally housing and eventually it would let go. Turns out it took 9 attempts

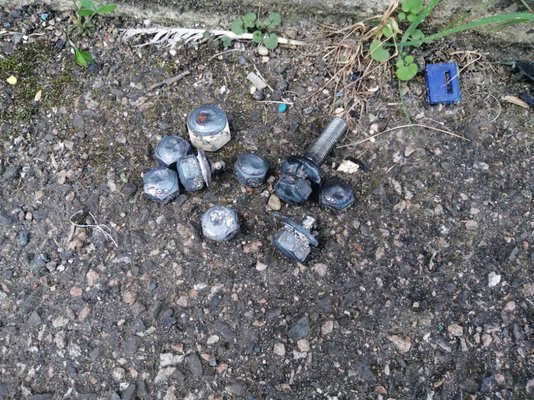
And the result - new bolt screws right in. To say that he was relieved is an understatement, because the next step was to drop the engine, remove the plate and put it in my milling machine.
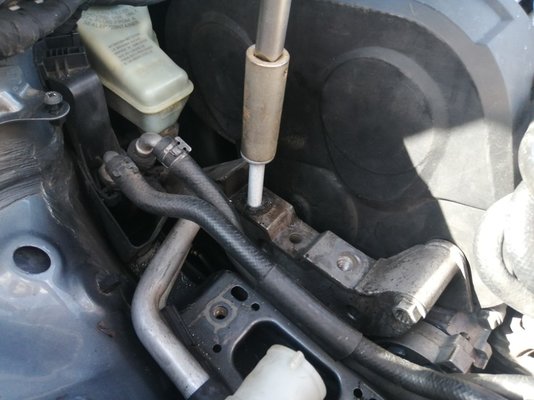