outofthefire
Member
- Messages
- 2,881
A couple I'm playing with, the top one is an old farriers rasp, hardened brought home to put in our brand new oven (just got to wait till our lass isn't looking )
The bottom one is from a piece of steel I'd forgotten about, I found it the other day tidying up for the new kitchen. It's RWL34 damasteel, a powder metallurgy made stainless steel named after the famous knife maker Bob Loveless, https://damasteel.se/story-of-rwl34/
I've marked out the holes for the handle and the bevels which I'm going to cut with a file. I haven't decided whether to heat treat it myself or pay someone to do it, I've got a smaller offcut to play with so I'll decide on that outcome.
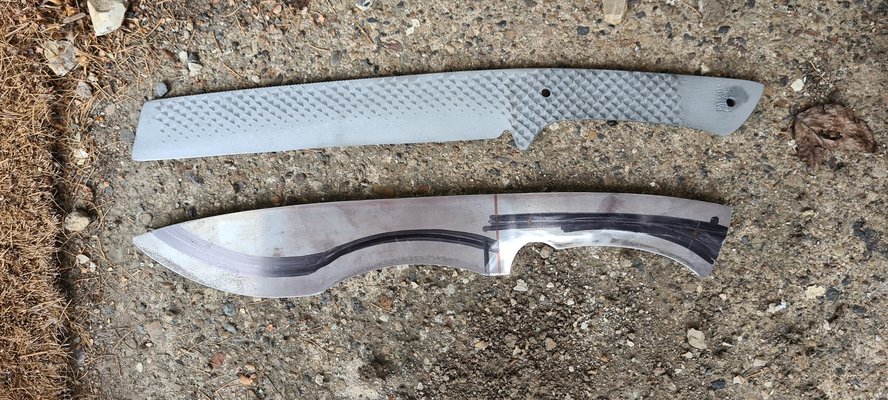
The bottom one is from a piece of steel I'd forgotten about, I found it the other day tidying up for the new kitchen. It's RWL34 damasteel, a powder metallurgy made stainless steel named after the famous knife maker Bob Loveless, https://damasteel.se/story-of-rwl34/
I've marked out the holes for the handle and the bevels which I'm going to cut with a file. I haven't decided whether to heat treat it myself or pay someone to do it, I've got a smaller offcut to play with so I'll decide on that outcome.
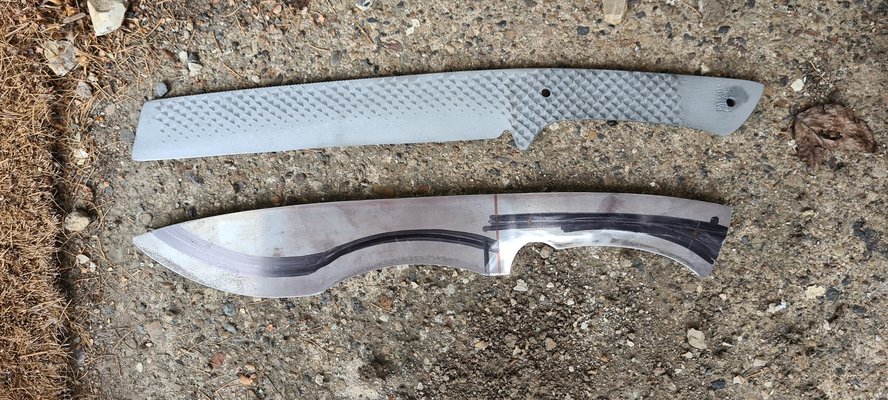