Richard.
Member
- Messages
- 18,347
- Location
- Cambridgeshire
We have a little range of positioners that we manufacture as modular systems. So they are fully integrated with a control system and a power source.
Like all Lorch equipment, you simply feed it information and the equipment takes care of the rest perfectly.
A customer wants to speed up a little repetitive job of Tig welding a disc onto a stainless tube to form an end cap. They have Been doing it manually and now looking to increase quality and speed.
So me and Matt had a bash at some today on the Turn 50 modular system with V50
Matt dialled in the tube diameter, a travel speed and a lovely pulse setting and away we went.
Some pics from today.
Cap fitted
Welded up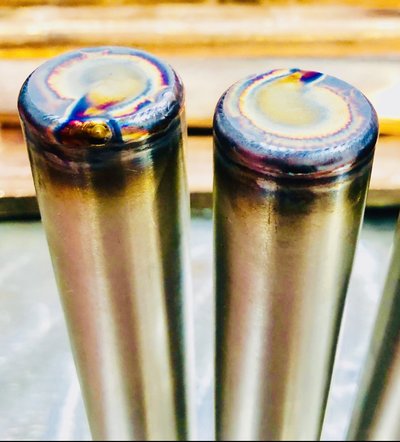
A little polish.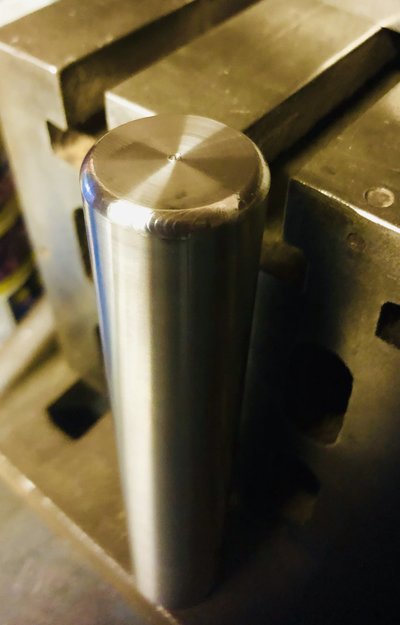
Like all Lorch equipment, you simply feed it information and the equipment takes care of the rest perfectly.
A customer wants to speed up a little repetitive job of Tig welding a disc onto a stainless tube to form an end cap. They have Been doing it manually and now looking to increase quality and speed.
So me and Matt had a bash at some today on the Turn 50 modular system with V50
Matt dialled in the tube diameter, a travel speed and a lovely pulse setting and away we went.
Some pics from today.
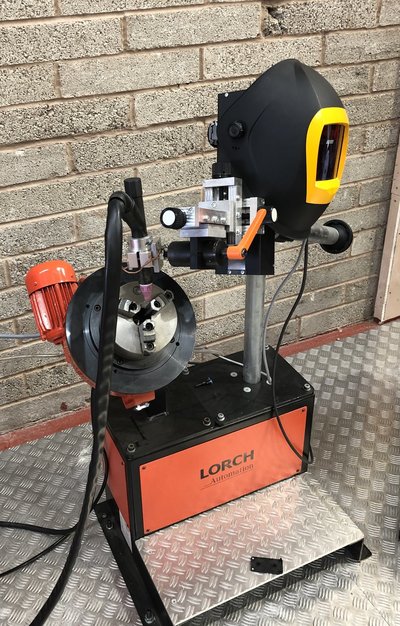
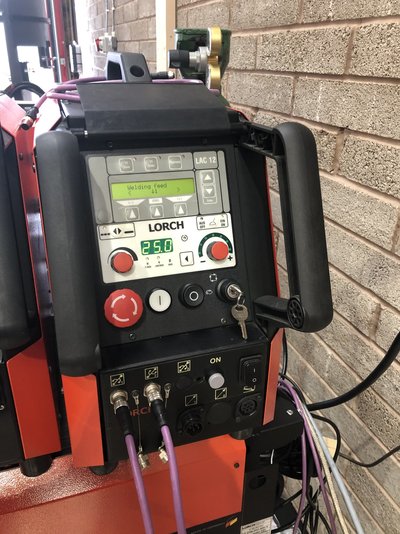
Cap fitted
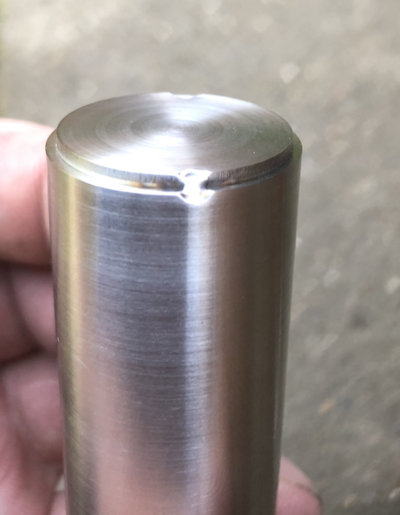
Welded up
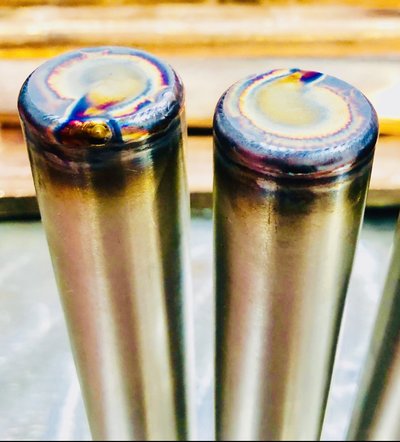
A little polish.
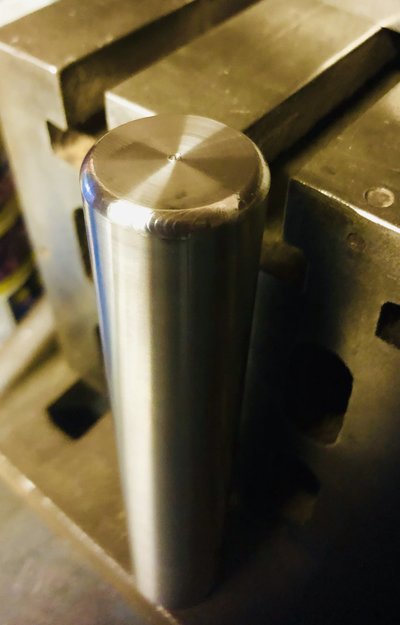