MattH
Member
- Messages
- 4,524
- Location
- Cornwall
Been working on a system to use 5c collets in my Boxford lathe which has a L00 spindle.
It's been going well so far and I am pleased with the results.
First job was to turn the internal thread on the drawbar pipe. I wanted to get this done first as it's the trickiest job:
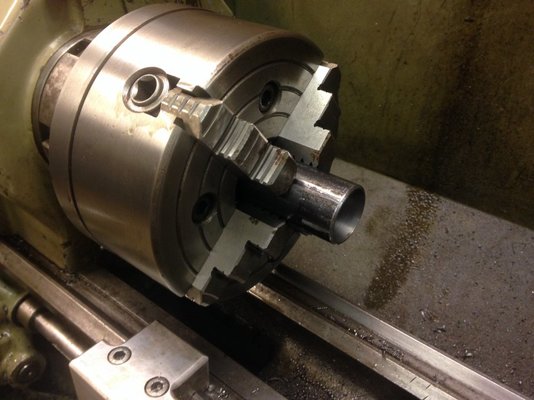
After one test run I managed to turn a 20tpi thread that ended up a perfect fit:
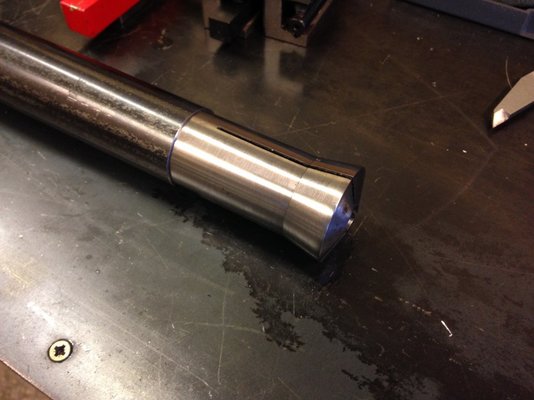
Next I turned a piece of 2" bar to match the internal taper in my spindle (don't know for sure but think it's a weird Morse 4.5). I managed to turn an excellent fit but putting a DTI on the compound and adjusting the angle for zero runout. Blueing the spindle showed this:
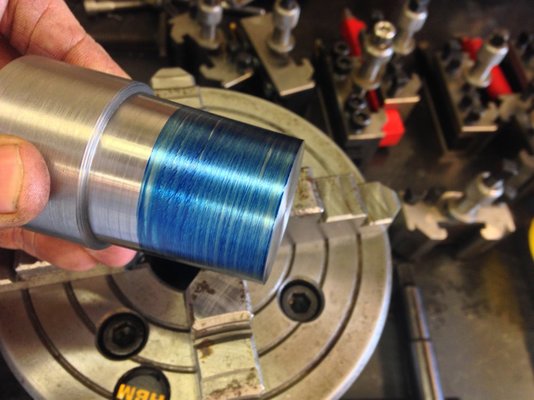
I then bored it all the way through for a tight sliding fit on the body of a collet and then adjusted the compound with the help of the DTI again to turn the 5C taper:
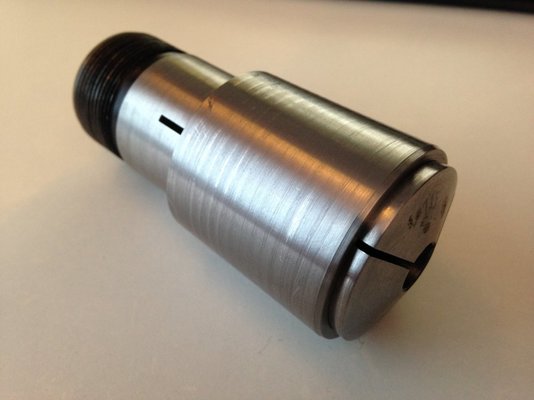
I turned a spacer for a loose sliding fit over the end of the drawbar with a counter bore on one end to fit over the end of the lathes spindle. This holds the drawbar centrally in the spindle and gives a bearing surface for tightening the drawbar (the large slug is the blank for the handle):
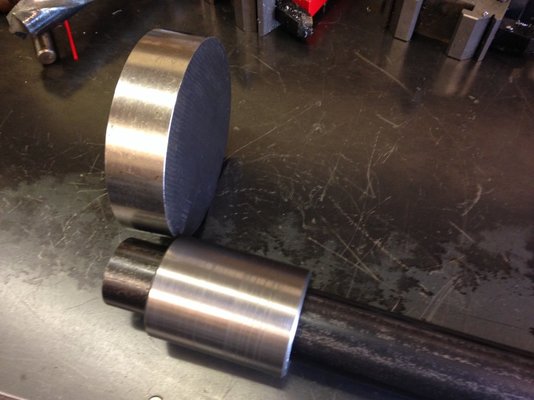
This shows the collet in the adapter and screwed into he drawbar:
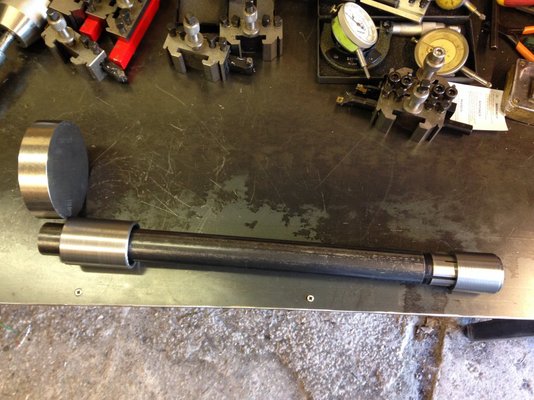
Test fit in the spindle nose:
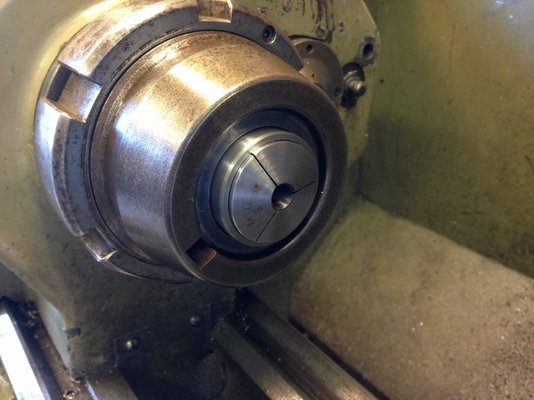
The drawbar is 1 1/4 and the spindle bore is 1 3/8ths:
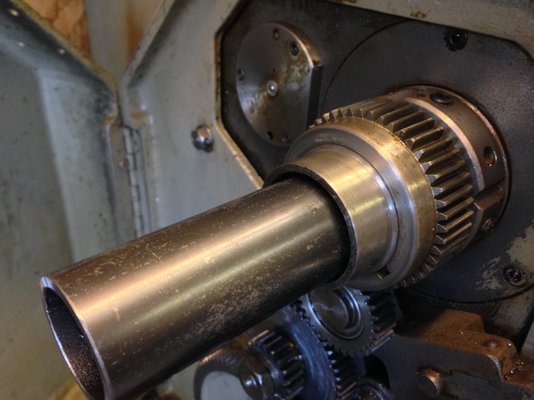
It's been going well so far and I am pleased with the results.
First job was to turn the internal thread on the drawbar pipe. I wanted to get this done first as it's the trickiest job:
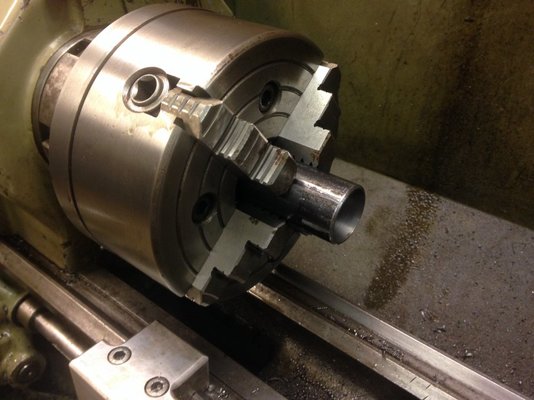
After one test run I managed to turn a 20tpi thread that ended up a perfect fit:
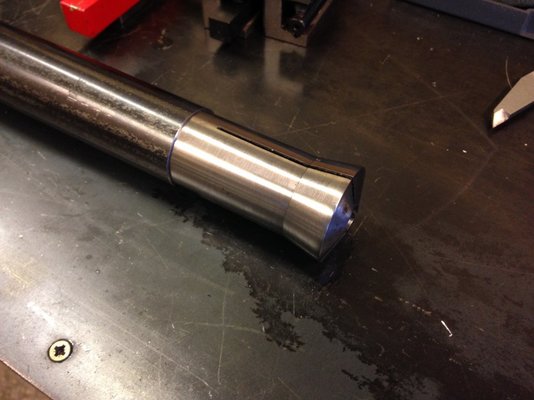
Next I turned a piece of 2" bar to match the internal taper in my spindle (don't know for sure but think it's a weird Morse 4.5). I managed to turn an excellent fit but putting a DTI on the compound and adjusting the angle for zero runout. Blueing the spindle showed this:
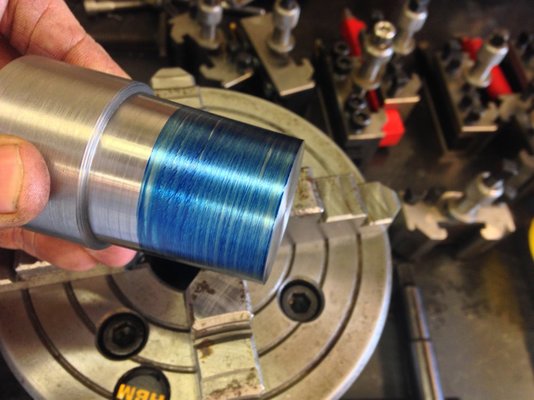
I then bored it all the way through for a tight sliding fit on the body of a collet and then adjusted the compound with the help of the DTI again to turn the 5C taper:
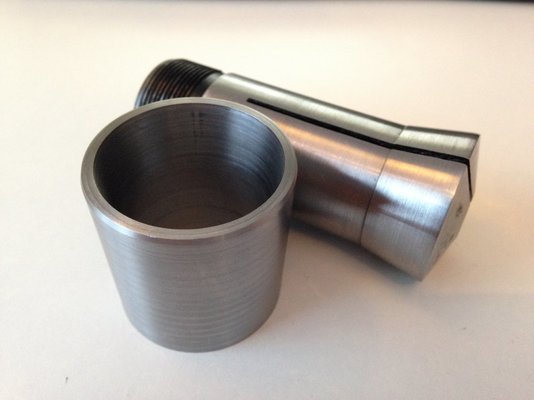
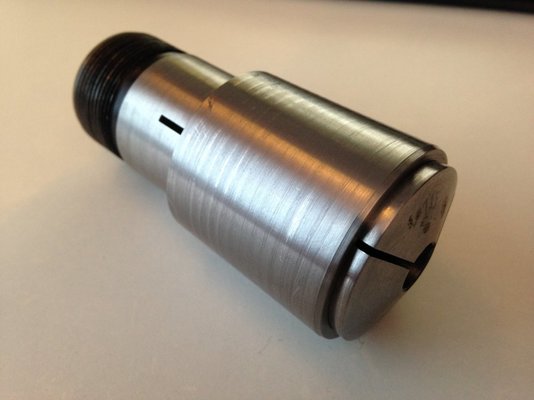
I turned a spacer for a loose sliding fit over the end of the drawbar with a counter bore on one end to fit over the end of the lathes spindle. This holds the drawbar centrally in the spindle and gives a bearing surface for tightening the drawbar (the large slug is the blank for the handle):
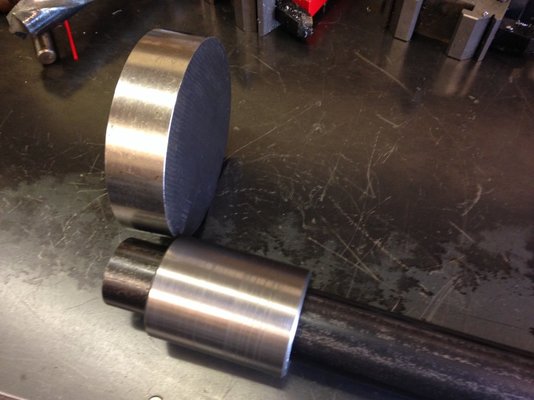
This shows the collet in the adapter and screwed into he drawbar:
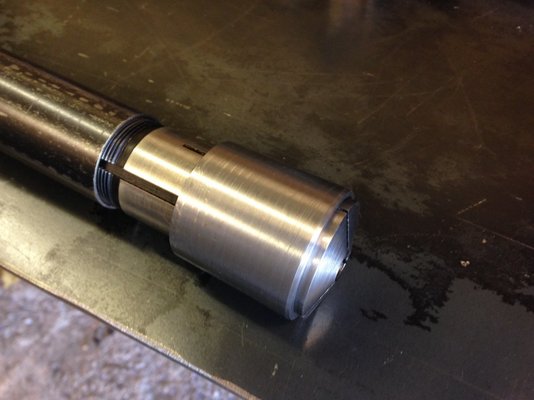
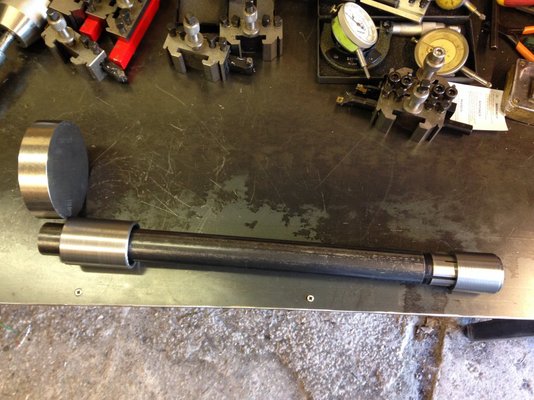
Test fit in the spindle nose:
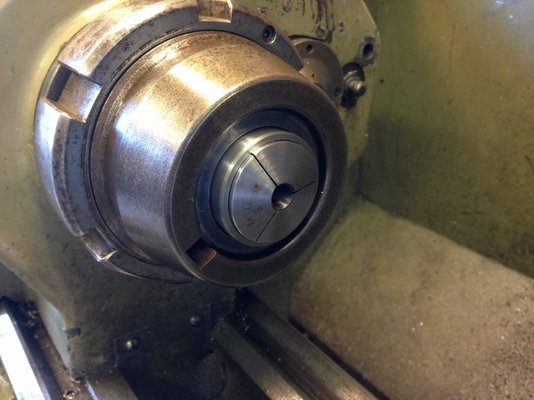
The drawbar is 1 1/4 and the spindle bore is 1 3/8ths:
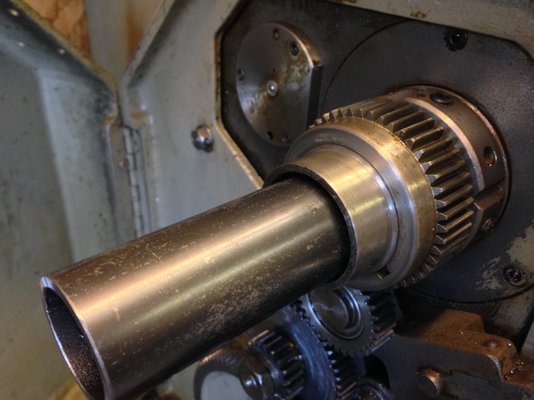