carl0s
Member
- Messages
- 345
- Location
- Kelsall
I had my first try of TIG today. I really like the process, it's much more controllable than MIG.
My first try at mild steel with filler. It needs a lot of work. I think the problem I am having is that instead of feeding filler into the pool, I am sort of pooling the filler on the end of the rod and dabbing that blob onto the material.
I had four goes here (each side), in the order of the photos. The long side with consistent-ish gaps (last photo) was the final attempt, however I did re-run the torch across to re-melt it afterwards a bit.
hmmm:
at least a little bit consistent, but still quite grim:
My first try at autogenous on stainless pipe. I really prefer autogenous I think because I can steady the torch so much better by resting my other hand against the torch hand. I didn't do any sort of purge setup because it's hardly a pipe really - just two small cut offs. Unfortunately I have discovered that the blade on my TCT saw (Dewalt 872L) is rubbish, hence the poor mating of the surfaces and thus gaps. So I've ordered a new blade:
The inside of the autogenous weld is, erm, not welded. That's called "poor/no penetration", right? and not good I guess. You can see the rough fit of the pipes too:
All done at ~75 amps, without pulse, 1.6mm tungsten, 6L/min argon.
Any tips? I think I had the arc length at about 2mm ish.
My first try at mild steel with filler. It needs a lot of work. I think the problem I am having is that instead of feeding filler into the pool, I am sort of pooling the filler on the end of the rod and dabbing that blob onto the material.
I had four goes here (each side), in the order of the photos. The long side with consistent-ish gaps (last photo) was the final attempt, however I did re-run the torch across to re-melt it afterwards a bit.
hmmm:
at least a little bit consistent, but still quite grim:
My first try at autogenous on stainless pipe. I really prefer autogenous I think because I can steady the torch so much better by resting my other hand against the torch hand. I didn't do any sort of purge setup because it's hardly a pipe really - just two small cut offs. Unfortunately I have discovered that the blade on my TCT saw (Dewalt 872L) is rubbish, hence the poor mating of the surfaces and thus gaps. So I've ordered a new blade:



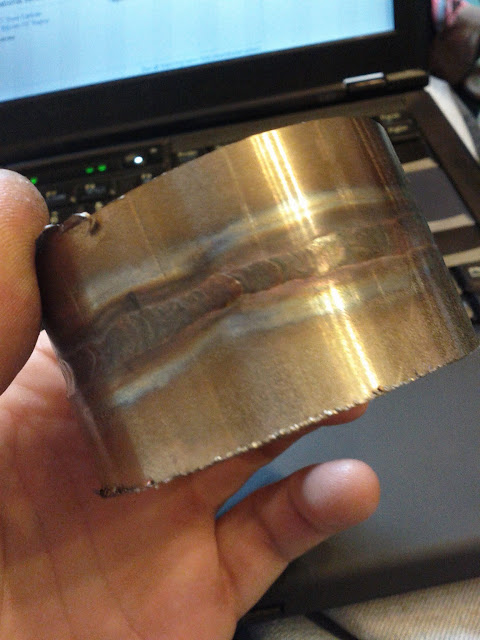


The inside of the autogenous weld is, erm, not welded. That's called "poor/no penetration", right? and not good I guess. You can see the rough fit of the pipes too:
All done at ~75 amps, without pulse, 1.6mm tungsten, 6L/min argon.
Any tips? I think I had the arc length at about 2mm ish.