hello forum,
im quite new to mig welding but its something i have been very interested in, i have finaly bought a welder (wolf 140 mig) to help with my suzuki sj jeep project and help me learn. so far i have had one really good practice go on sheet metal around 1mm but so far i havent been able to get any penetration, i have tried a few things like increasing the voltage and wire speed and slowing down the movement of the torch but to no sucsess.
the metal on the jeep is thiner than the metal im using to repair it, the repair metal is about 1mm. so far i have tacked the metal in place whith a lot of tacks but what i want to do is grind the tacks back and do a continuous seem weld, but im not sure if i will be able to get good penetration on the thick metal without blowing holes in the thiner metal.
to take back the tack welds i have bought some 40grit flap discs, but these dont fit in my grinder because the hole in the center is too small, i was under the impression that all of these holes where the same size, is there any adaption i can do or should i buy the right ones?
i am using co2 that came with the welder but would argon be better for thin metal? as the co2 ran out today, it was one of the small bottles and it didnt last very long.
thankyou for the help
joe
im quite new to mig welding but its something i have been very interested in, i have finaly bought a welder (wolf 140 mig) to help with my suzuki sj jeep project and help me learn. so far i have had one really good practice go on sheet metal around 1mm but so far i havent been able to get any penetration, i have tried a few things like increasing the voltage and wire speed and slowing down the movement of the torch but to no sucsess.
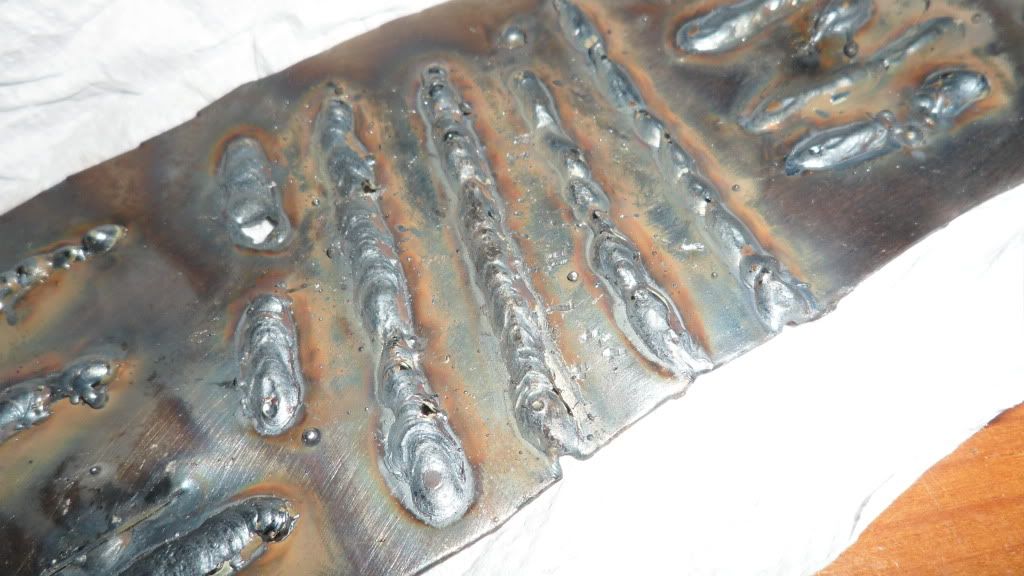

the metal on the jeep is thiner than the metal im using to repair it, the repair metal is about 1mm. so far i have tacked the metal in place whith a lot of tacks but what i want to do is grind the tacks back and do a continuous seem weld, but im not sure if i will be able to get good penetration on the thick metal without blowing holes in the thiner metal.
to take back the tack welds i have bought some 40grit flap discs, but these dont fit in my grinder because the hole in the center is too small, i was under the impression that all of these holes where the same size, is there any adaption i can do or should i buy the right ones?
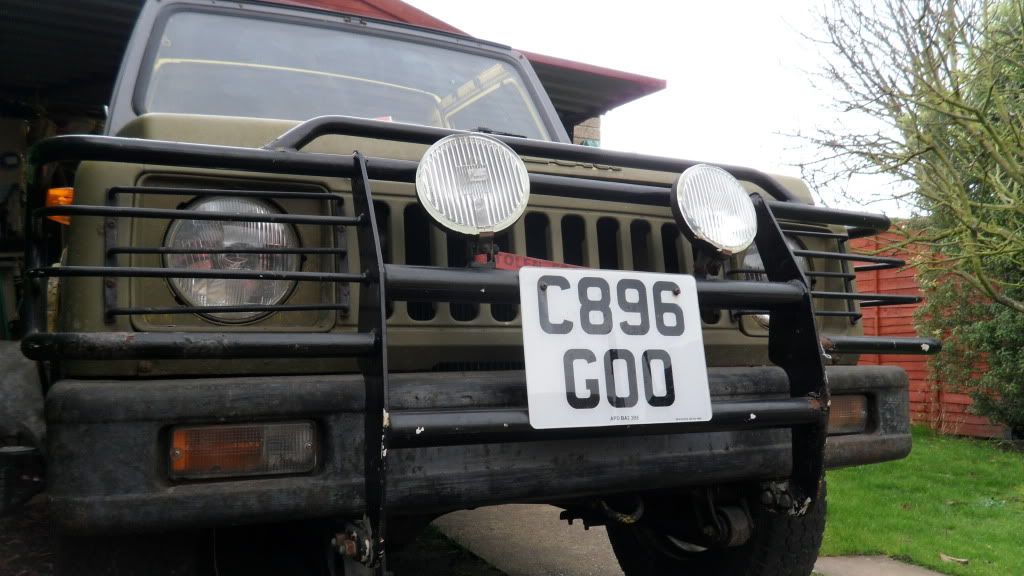
i am using co2 that came with the welder but would argon be better for thin metal? as the co2 ran out today, it was one of the small bottles and it didnt last very long.
thankyou for the help
joe