Munkul
Jack of some trades, Master of none
- Messages
- 7,694
- Location
- Cumbria
For your interest/comment/disgust/arousal.
@hotponyshoes sold me a NOS reel of Lincoln 71E-H Outershield wire, and i was keen to try it out!
So here's a very limited and un-scientific review of what I tried.
I've only tried self shielded fluxcore before, in Innershield NR211 flavour. It's not bad stuff to run, but I wasn't impressed with the mechanical properties of the stuff. I thought about trying some structural grade NR232/NR233, but was put off by two facts: one, it takes a lot of skill and practice to run well, and two, it makes a horrible amount of fume.
I was, however, impressed with how easy flux core wire is to run uphill and overhead, so at some point I wanted to try some dualshield wire, as it's more forgiving to run and less fume produced than Innershield.
Any time i need to do repair work on machinery i couldn't weld on the flat, my go-to is 7018 rods, since I'm crap with hard wire MIG uphill.
This is the wire. Good mechanical properties, more than good-enough choice for a general-purpose all position wire for mild steel repair work. Impact rated as well, unlike NR211.
This is the product info and datasheet
www.lincolnelectric.com
So I set it up in the S3, no changes from solid steel wire other than to take most of the tension off the rolls. I had to get a wire basket holder, as the 15kg reels come in centreless baskets.
I used the same gas I use for hard wire - 15% CO2, 2%O2, 83% Ar. This should effectively should act like a gas with up to 20% CO2 which is within the recommended 15-25% CO2
I got rid of the first 20-30 metres of the stuff just to eliminate dirty/corroded wire or damp flux.
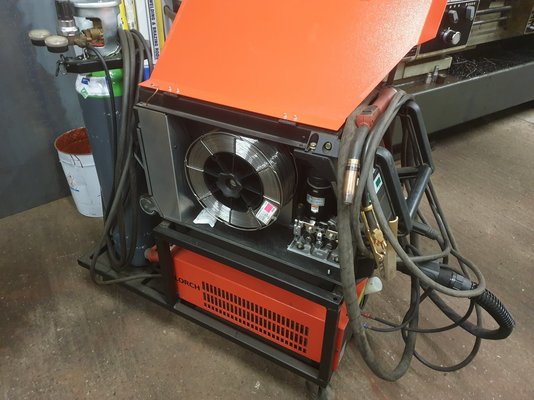
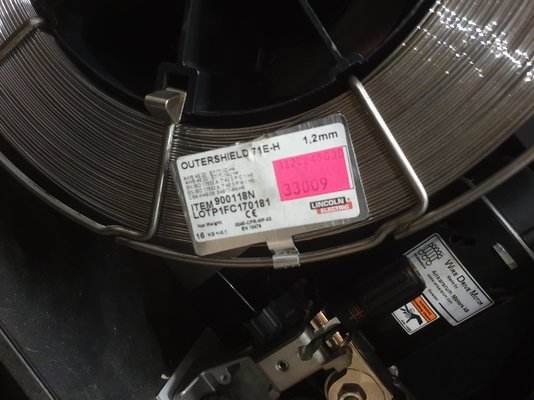
I ran it in the synergic CV program for rutile fluxcore, and took the voltage trim down to -20, as it seemed quite spattery at 0. It ran really nicely at around 180-200 amps and 22 volts, which is slightly lower volts than the datasheet recommended.
I ran a load of fillet test pieces off with 6mm and 8mm plate, pretty much all the same settings. No cleaning or any prep done - this was on purpose. I want it to burn through millscale and crap, if it works like this then it will DEFINITELY work on clean metal.
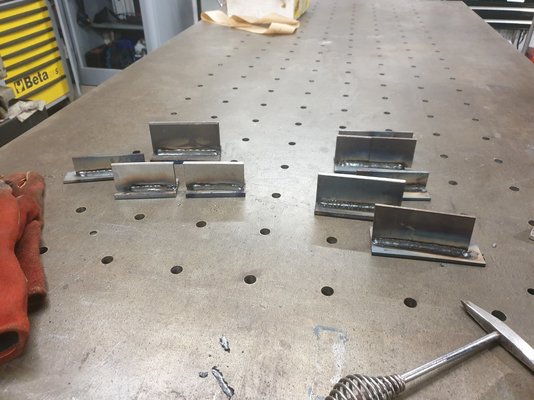
This 8mm was on the flat. - I ran it with a slight drag angle, near 90 degrees. I did another piece with a push angle like solid wire MIG and it looked and felt OK, but "If there's slag, we drag"
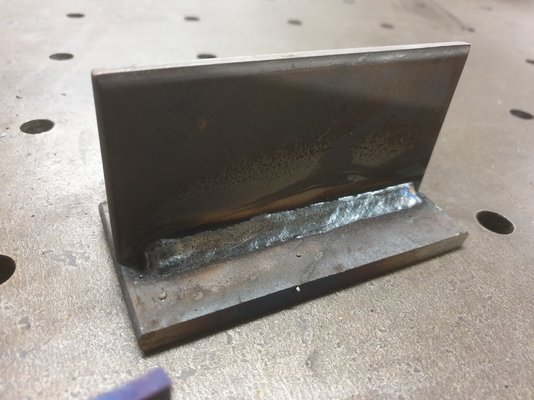
This was 6mm vertical up. I ran it with a 90 degree with slight push. I also did an 8mm vertical up, which looked way worse. I didn't chop this one up.
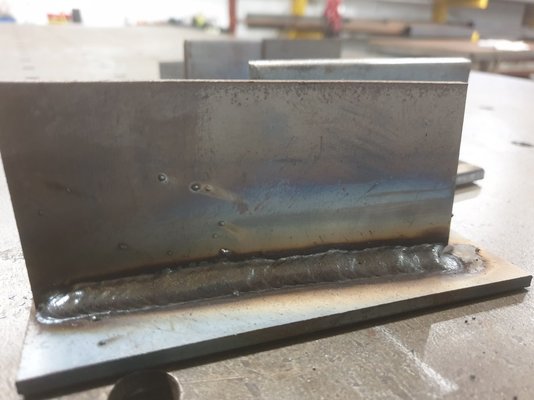
I cut some pieces out to check penetration and did a "scientific" bend test, of putting a sliced section in the vice and bending it with a big adjustable.
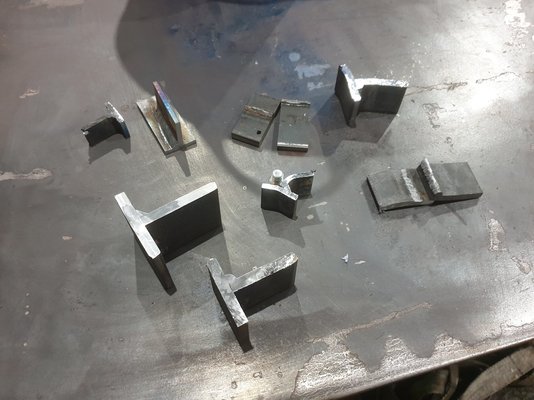
This was the uphill on 8mm. The profile is very poor, i should have paused a lot longer. Penetration was good (sorry my etching doesn't show up) but not especially deep. The millscale wouldn't have helped.
The weld broke, but it tore out of the parent material below the penetration. My theory is that the weld toes were really bad, and acted as stress risers, helping it to fail. I will have to repeat this test with either more amps, or pause on the toes for longer.
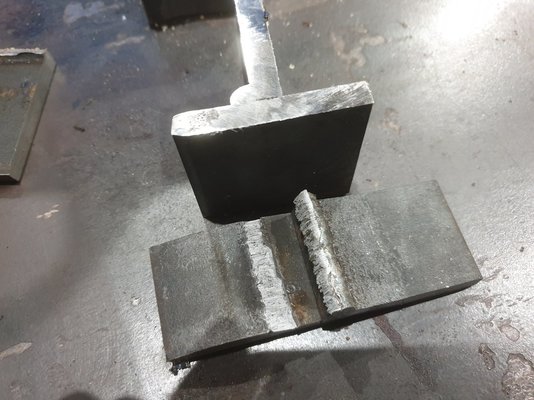
This was the flat on 8mm. This was entirely my fault. The weld was too cold and too small. Penetration was poor, barely nipping the root, and it snapped in the middle of the weld. I need to repeat this test with a load more amps.
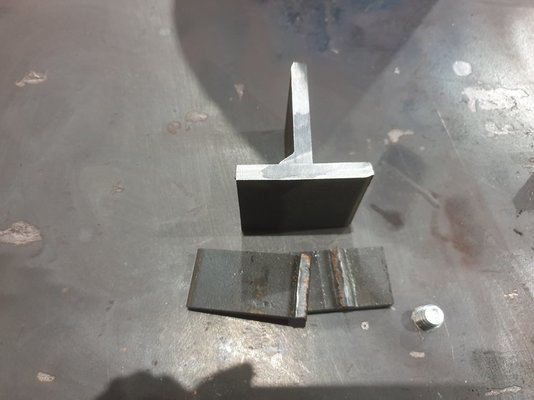
This was the flat on 6mm. Same amps as the 8mm. Profile is good, and the weld did not break at all. Plenty penetration.
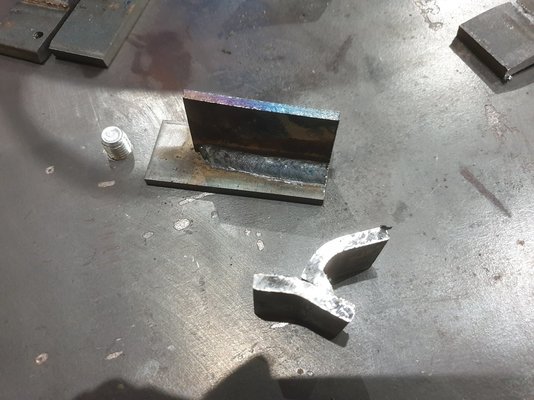
So, my limited conclusions:
- Easy to run uphill. Not as easy as 7018, as it digs in quite savagely. Possibly needing those extra recommended volts to spread the arc out a bit more, i might get better weld toes.
- There is a significant amount of slag with this stuff, but it's self releasing, and really easy to scrape off. Like the best 6013s I've ever ran.
- More fume than solid-wire, but less fume than MMA welding.
- 180 amps on 6mm plate is sufficient to give an excellent weld.
- Needs probably 220 amps and upwards to give a good weld on 8mm in the flat.
- Needs some practice and setting changes to get a good uphill weld.
I'm going to experiment a bit more with this stuff, and get some settings that work on 8mm. At the moment, I can't trust it or myself for anything important.
...And then go back to hard wire for general purpose. I'll keep this stuff for machinery repair work where I need to run out of position.
@hotponyshoes sold me a NOS reel of Lincoln 71E-H Outershield wire, and i was keen to try it out!
So here's a very limited and un-scientific review of what I tried.
I've only tried self shielded fluxcore before, in Innershield NR211 flavour. It's not bad stuff to run, but I wasn't impressed with the mechanical properties of the stuff. I thought about trying some structural grade NR232/NR233, but was put off by two facts: one, it takes a lot of skill and practice to run well, and two, it makes a horrible amount of fume.
I was, however, impressed with how easy flux core wire is to run uphill and overhead, so at some point I wanted to try some dualshield wire, as it's more forgiving to run and less fume produced than Innershield.
Any time i need to do repair work on machinery i couldn't weld on the flat, my go-to is 7018 rods, since I'm crap with hard wire MIG uphill.
This is the wire. Good mechanical properties, more than good-enough choice for a general-purpose all position wire for mild steel repair work. Impact rated as well, unlike NR211.
This is the product info and datasheet
Welding Wire, Flux and Rods | Lincoln Electric
Find Lincoln Electric industry leading Stick (SMAW), MIG (GMAW), TIG (GTAW), Flux-Cored (FCAW-G and FCAW-S) and Submerged Arc (SAW) welding wire.
So I set it up in the S3, no changes from solid steel wire other than to take most of the tension off the rolls. I had to get a wire basket holder, as the 15kg reels come in centreless baskets.
I used the same gas I use for hard wire - 15% CO2, 2%O2, 83% Ar. This should effectively should act like a gas with up to 20% CO2 which is within the recommended 15-25% CO2
I got rid of the first 20-30 metres of the stuff just to eliminate dirty/corroded wire or damp flux.
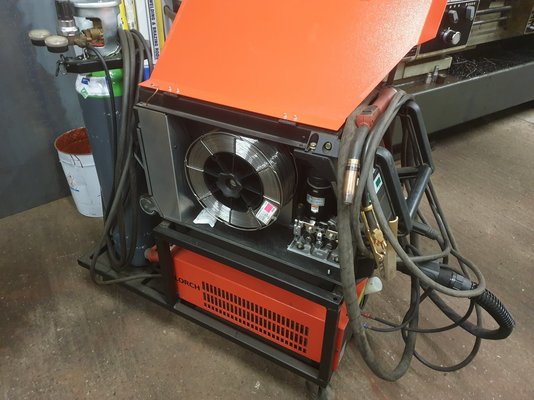
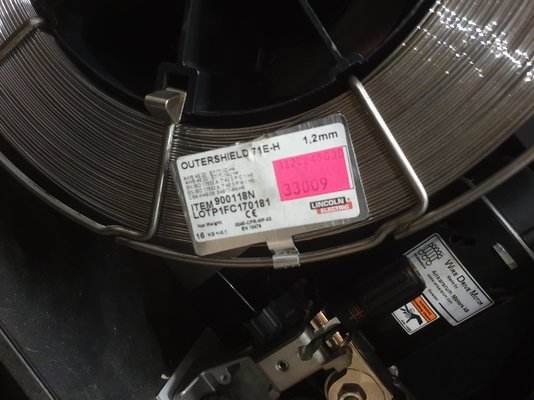
I ran it in the synergic CV program for rutile fluxcore, and took the voltage trim down to -20, as it seemed quite spattery at 0. It ran really nicely at around 180-200 amps and 22 volts, which is slightly lower volts than the datasheet recommended.
I ran a load of fillet test pieces off with 6mm and 8mm plate, pretty much all the same settings. No cleaning or any prep done - this was on purpose. I want it to burn through millscale and crap, if it works like this then it will DEFINITELY work on clean metal.
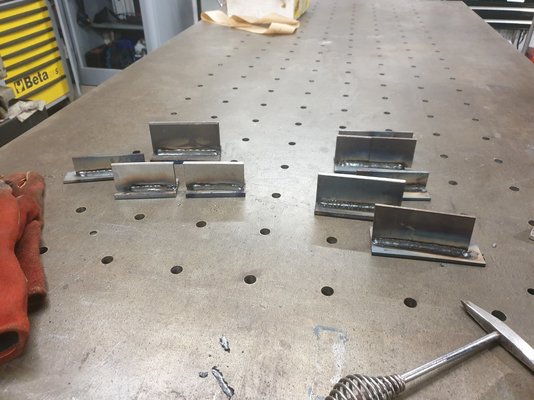
This 8mm was on the flat. - I ran it with a slight drag angle, near 90 degrees. I did another piece with a push angle like solid wire MIG and it looked and felt OK, but "If there's slag, we drag"
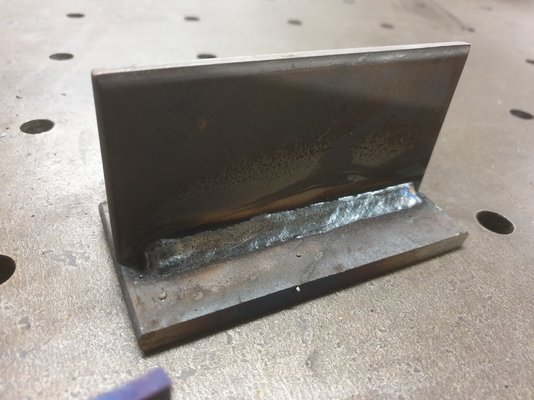
This was 6mm vertical up. I ran it with a 90 degree with slight push. I also did an 8mm vertical up, which looked way worse. I didn't chop this one up.
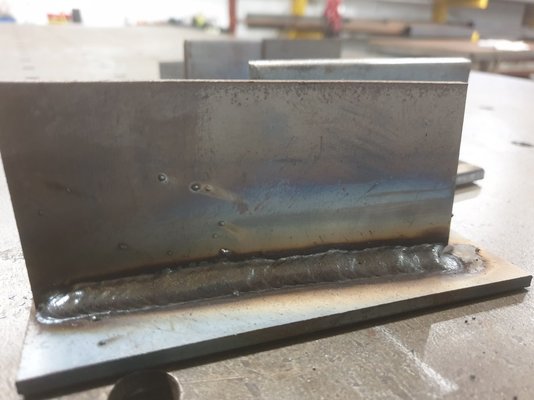
I cut some pieces out to check penetration and did a "scientific" bend test, of putting a sliced section in the vice and bending it with a big adjustable.
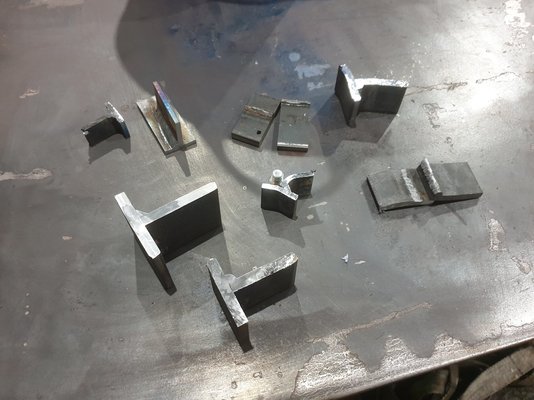
This was the uphill on 8mm. The profile is very poor, i should have paused a lot longer. Penetration was good (sorry my etching doesn't show up) but not especially deep. The millscale wouldn't have helped.
The weld broke, but it tore out of the parent material below the penetration. My theory is that the weld toes were really bad, and acted as stress risers, helping it to fail. I will have to repeat this test with either more amps, or pause on the toes for longer.
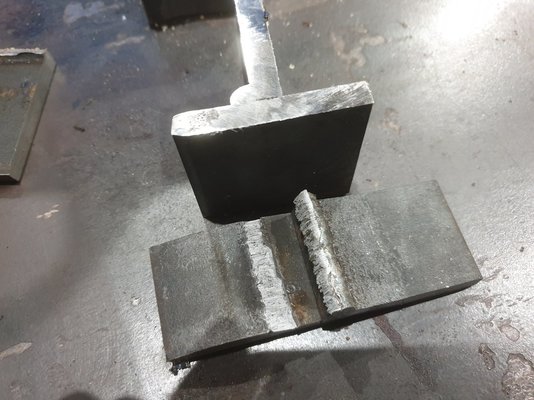
This was the flat on 8mm. This was entirely my fault. The weld was too cold and too small. Penetration was poor, barely nipping the root, and it snapped in the middle of the weld. I need to repeat this test with a load more amps.
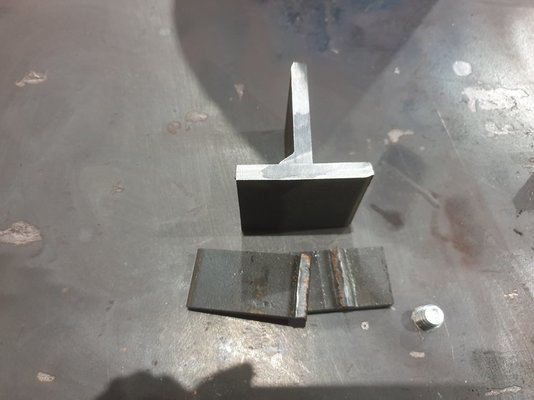
This was the flat on 6mm. Same amps as the 8mm. Profile is good, and the weld did not break at all. Plenty penetration.
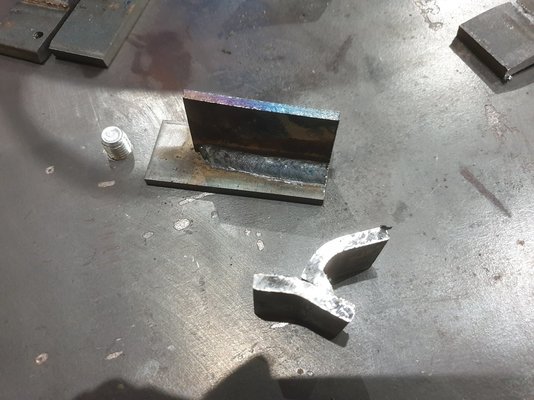
So, my limited conclusions:
- Easy to run uphill. Not as easy as 7018, as it digs in quite savagely. Possibly needing those extra recommended volts to spread the arc out a bit more, i might get better weld toes.
- There is a significant amount of slag with this stuff, but it's self releasing, and really easy to scrape off. Like the best 6013s I've ever ran.
- More fume than solid-wire, but less fume than MMA welding.
- 180 amps on 6mm plate is sufficient to give an excellent weld.
- Needs probably 220 amps and upwards to give a good weld on 8mm in the flat.
- Needs some practice and setting changes to get a good uphill weld.
I'm going to experiment a bit more with this stuff, and get some settings that work on 8mm. At the moment, I can't trust it or myself for anything important.
...And then go back to hard wire for general purpose. I'll keep this stuff for machinery repair work where I need to run out of position.