Pete.
Member
- Messages
- 14,705
- Location
- Kent, UK
I have three granite surface plates that I've started to refurbish this week so it's time to start a thread and record my blundering progress.
Obviously a granite plate has to be flat for it to be any good and there are different grades of flatness (along with different ways of specifying it) so really before you can really trust a plate as a flatness reference you need a way of measuring it, then once measured you then need a way of working on it to bring it into a condition that you are happy with.
I have my autocollimator and my repeat-o-meter which will allow me to assess global and local flatness. You need to use both because whilst the repeat-o-meter is a great tool for showing local variations like humps and dips it cannot (normally) tell the difference between a uniformly flat surface and a uniformly curved one. If you put it on the inside or outside of a sphere it will read the same all over but obviously the sphere isn't flat. It also cannot always tell the difference between the end foot riding a hump and the middle feet falling into a dip, though an experienced operator (which I am not) would be able to interpret the readings correctly from experience most likely.
The autocollimator uses one or two mirrors which travel along the plate and reflect back the image of a cross-hair that shows the operator if the mirror is tilting up or down, and by how much. It tells the operator how much the part of the plate the mirror is sat on deviates from the average plane, so it's a way of 1. assessing the plat initially and 2. checking that the remedial work is producing a flat plane or a uniformly curved one. Important to know because a dished or humped plate is useless.
So, having the checking tools it's time to make the refurbishing tools. You need three things: a lap, some lapping medium and a method of applying both. Given that the process is already well established it made sense to just follow on what others have done so I got myself a small iron plate to use as a lap, some diamond powder as a medium and all that was left was to make a hardened roller to embed the medium into the lap.
A kind member here had send me some rusty capstan tooling which is fully hardened so I decided to make a roller from one of those.
I took a hardened 2" Od MT3 socket and ground the outside on my little MG9 grinder
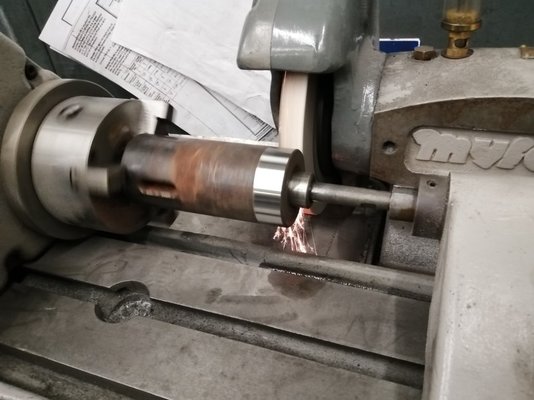
Then I cut it off with a mini-grinder and trued up the ends
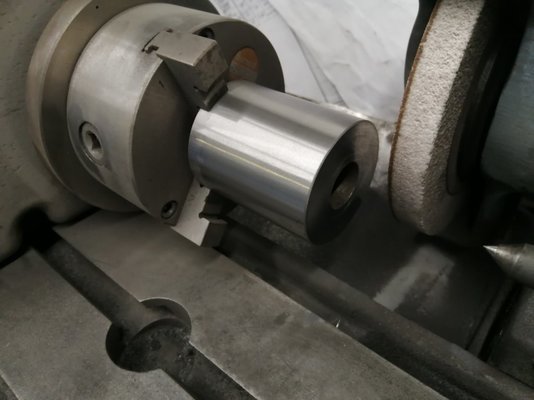
After that I found a rusty old reamer, cleaned the shank up and cut off the flutes. I hammered it as hard as I could into the socket and then ground the ends for an axle.
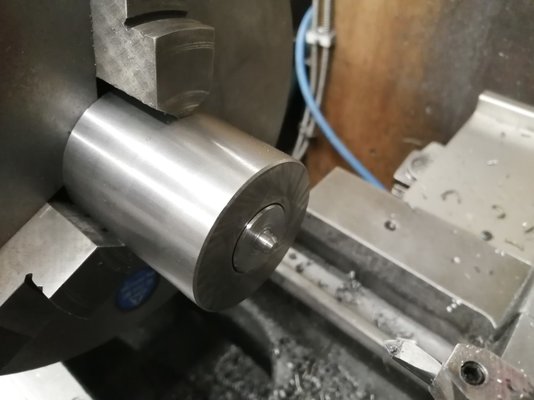
Once the roller was made it was a simple matter to make a yoke and fit a handle.
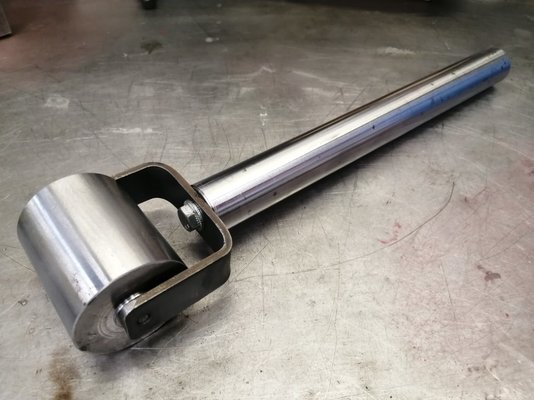
Obviously a granite plate has to be flat for it to be any good and there are different grades of flatness (along with different ways of specifying it) so really before you can really trust a plate as a flatness reference you need a way of measuring it, then once measured you then need a way of working on it to bring it into a condition that you are happy with.
I have my autocollimator and my repeat-o-meter which will allow me to assess global and local flatness. You need to use both because whilst the repeat-o-meter is a great tool for showing local variations like humps and dips it cannot (normally) tell the difference between a uniformly flat surface and a uniformly curved one. If you put it on the inside or outside of a sphere it will read the same all over but obviously the sphere isn't flat. It also cannot always tell the difference between the end foot riding a hump and the middle feet falling into a dip, though an experienced operator (which I am not) would be able to interpret the readings correctly from experience most likely.
The autocollimator uses one or two mirrors which travel along the plate and reflect back the image of a cross-hair that shows the operator if the mirror is tilting up or down, and by how much. It tells the operator how much the part of the plate the mirror is sat on deviates from the average plane, so it's a way of 1. assessing the plat initially and 2. checking that the remedial work is producing a flat plane or a uniformly curved one. Important to know because a dished or humped plate is useless.
So, having the checking tools it's time to make the refurbishing tools. You need three things: a lap, some lapping medium and a method of applying both. Given that the process is already well established it made sense to just follow on what others have done so I got myself a small iron plate to use as a lap, some diamond powder as a medium and all that was left was to make a hardened roller to embed the medium into the lap.
A kind member here had send me some rusty capstan tooling which is fully hardened so I decided to make a roller from one of those.
I took a hardened 2" Od MT3 socket and ground the outside on my little MG9 grinder
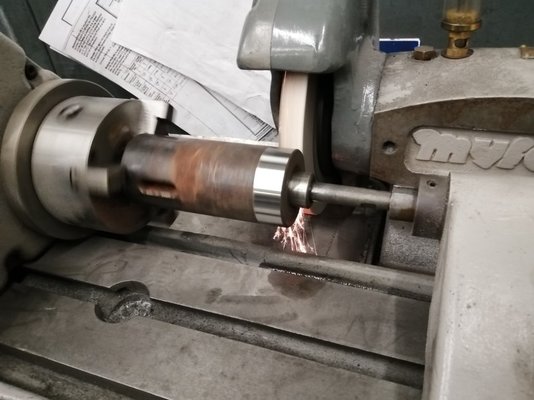
Then I cut it off with a mini-grinder and trued up the ends
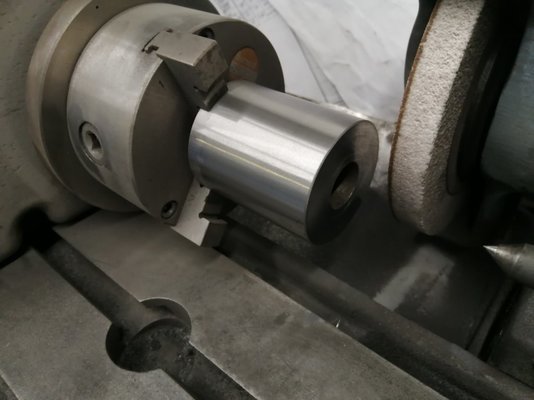
After that I found a rusty old reamer, cleaned the shank up and cut off the flutes. I hammered it as hard as I could into the socket and then ground the ends for an axle.
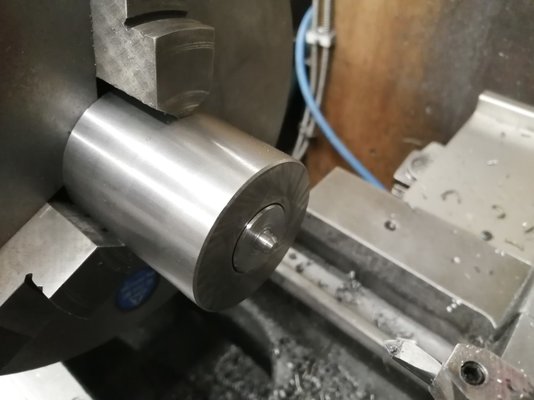
Once the roller was made it was a simple matter to make a yoke and fit a handle.
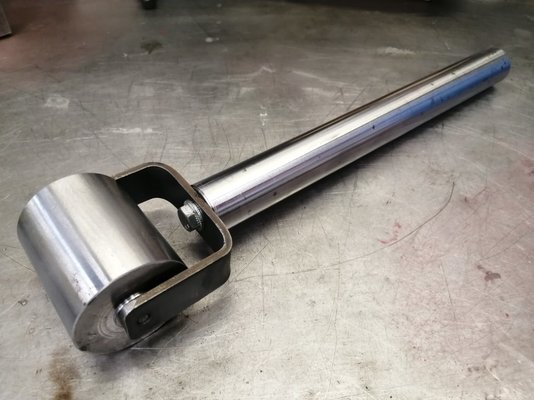