alogaparaloga
Member
- Messages
- 14
I thought to start a thread with some photos of my welds so as I can get some constructive comments and improve my skills. 
I don't have any scrap material to play with so I started welding anged tube slices which I cut some time ago for my custom exhaust system.
The pipe is quite forgiving as it is 2.0mm thick.
I started with problems due to a leak on the regulator as the arrow shows on the pic
I have to call weld equip if they can get this replaced as I have it for a few months but I just got it out of the box. For that the only fix was to buy a replacement one from Halfords and I managed to start.
The following pictures show my welds. BTW I use 86/14% argon/CO2. and the welder is set to the power recommended for my clarke 151en, with the feed rate set at 7 instead of 6 as per manual's recomendations as the wire melts back in the shroud.
I also found my torch angle not to be the best so I started welding smaller sections and tha sorted thing a bit.

I don't have any scrap material to play with so I started welding anged tube slices which I cut some time ago for my custom exhaust system.
The pipe is quite forgiving as it is 2.0mm thick.
I started with problems due to a leak on the regulator as the arrow shows on the pic


I have to call weld equip if they can get this replaced as I have it for a few months but I just got it out of the box. For that the only fix was to buy a replacement one from Halfords and I managed to start.
The following pictures show my welds. BTW I use 86/14% argon/CO2. and the welder is set to the power recommended for my clarke 151en, with the feed rate set at 7 instead of 6 as per manual's recomendations as the wire melts back in the shroud.
I also found my torch angle not to be the best so I started welding smaller sections and tha sorted thing a bit.

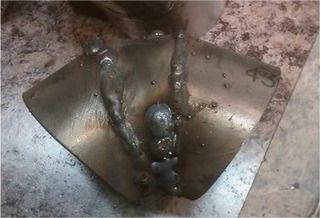
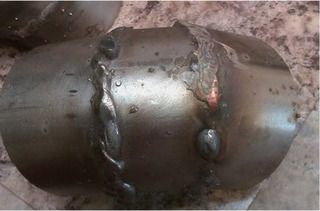



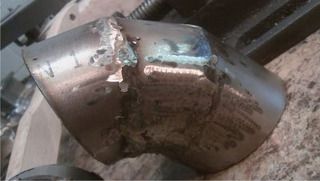
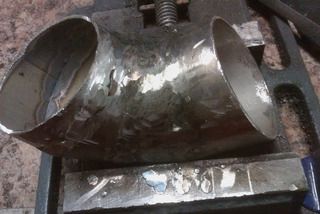
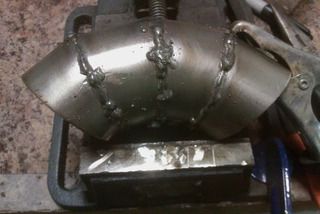
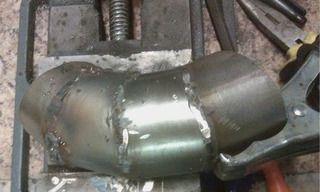