N
Nidgodh
Guest
Hey guys,
like I mentioned today in another post, I tried again to do some copper welding using TIG /141/ method. Base material was Copper 99.5% thickness 2 mm, filler material was CuSn diameter 2 mm. Welding was done using 4T settings (no pedal) and argon only was used. Two joints were produced, first was fillet weld in welding position PB and second was ''I'' joint in welding position PA. Fillet joint was welded using 150A, ''I'' joint using 135A. Because I didn't use pedal I was forced to stop, let cool the piece and restart on filled joint in welding position PB 3 times (there are visible two small tie-ins on pictures). I also tried to polish that copper PA joint for first time, I achieved mirror finish (I could see myself on that plate nicely). Of course there are some little scratches (I'm far from perfect on copper, those scratches just didn't wanted to go away!), but you can get the picture. Anyway, ''I'' joint in welding position PA, was fully penetrated in full length (will add photo on Monday). The front site of ''I'' joint was polished only, backside is without polish finish. If anybody did copper welding, please share, it's quite hard and unpredictable, welding pool flows like water and it can make hole just like that...
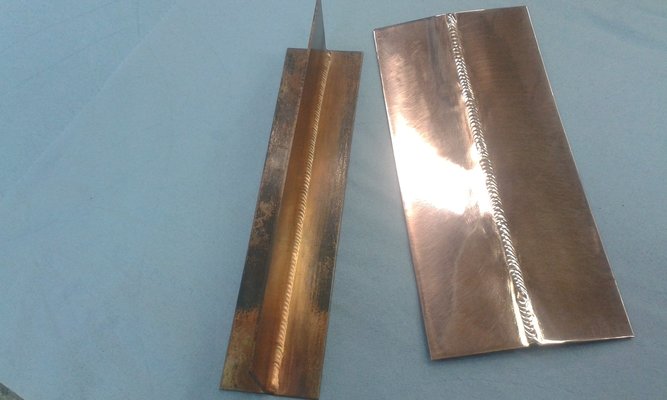
like I mentioned today in another post, I tried again to do some copper welding using TIG /141/ method. Base material was Copper 99.5% thickness 2 mm, filler material was CuSn diameter 2 mm. Welding was done using 4T settings (no pedal) and argon only was used. Two joints were produced, first was fillet weld in welding position PB and second was ''I'' joint in welding position PA. Fillet joint was welded using 150A, ''I'' joint using 135A. Because I didn't use pedal I was forced to stop, let cool the piece and restart on filled joint in welding position PB 3 times (there are visible two small tie-ins on pictures). I also tried to polish that copper PA joint for first time, I achieved mirror finish (I could see myself on that plate nicely). Of course there are some little scratches (I'm far from perfect on copper, those scratches just didn't wanted to go away!), but you can get the picture. Anyway, ''I'' joint in welding position PA, was fully penetrated in full length (will add photo on Monday). The front site of ''I'' joint was polished only, backside is without polish finish. If anybody did copper welding, please share, it's quite hard and unpredictable, welding pool flows like water and it can make hole just like that...
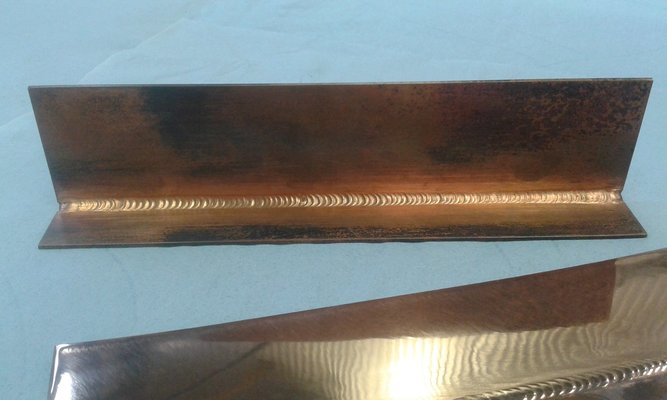
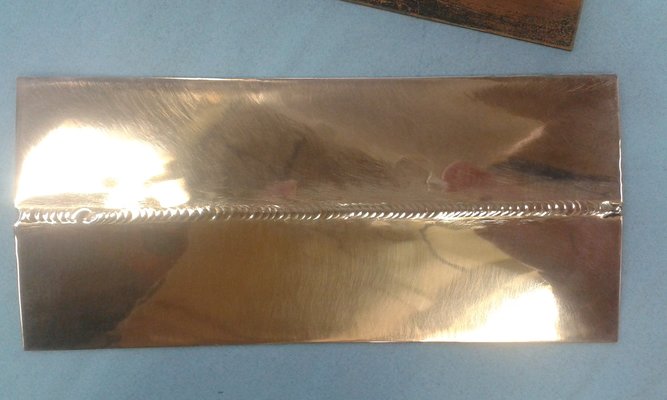
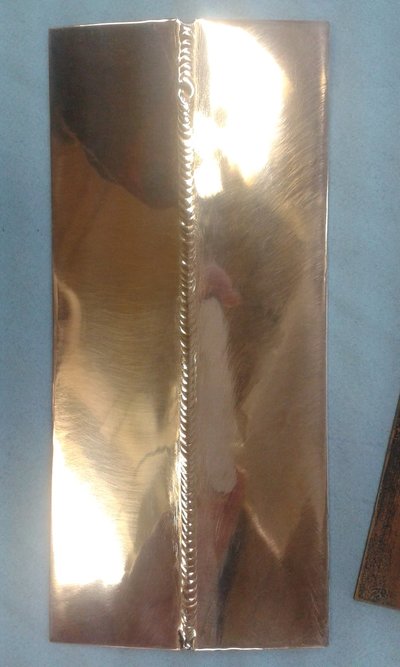
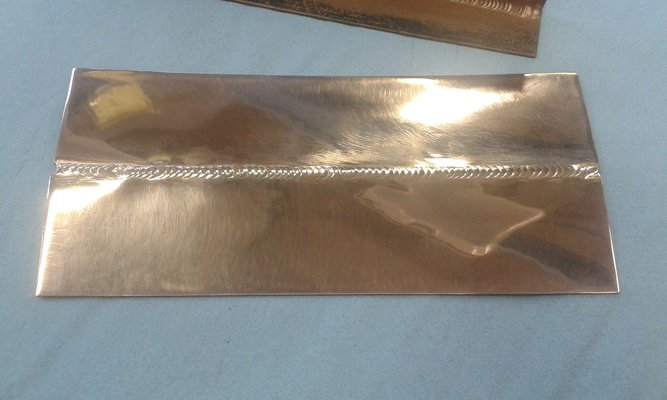
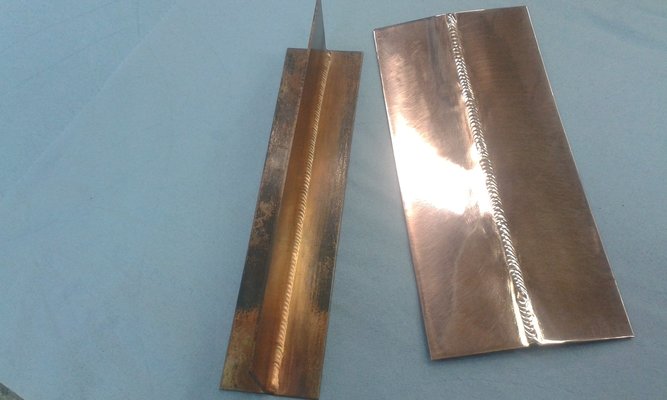