Hello from Canada!
I have a Lincoln 180 dual mig with a 100SG spool gun (I'm using 220v, 100% Argon gas at 35 cuft/hr). I've been hobby welding steel for about 10 years with no issues, but aluminum is a whole new animal. I would like to build a few things out of 2 inch square tubing so I picked up a scrap piece of 1/8" wall 1.75" tubing (no scrap 2"). I have a wire feed and voltage control knob, and trying to use the settings on the chart in the welder have produced horrible results. After hours of youtube videos Im still not sure how it can be this bad, especially after watching videos where guys set up a new gun and run it relatively issue free! I have come across comments about material that is 1/8th of an inch thick will produce horrible welds, so maybe that's my issue? I'm not sold on that, as a ton of the videos guys/gals are laying down beads on aluminum plate that is thinner that 1/8". I think part of the issue is I was trying beads on the same chunk of tubing and as it got hotter, I was blowing holes through it, so I need to let the piece cool down. I need to check my wire speed as I dont know what the 1-10 settings on the dial actually mean and maybe I don't have enough wire speed for proper spray transfer. With the recommended settings on the machine, I would either pile up material and have no penetration, or blow holes though it (as seen in the first photo). Best I could do was the second photo, but the bead doesn't look good and I cant see this actually welding two pieces of aluminum together. If anyone has used this spool gun and can offer and advice that would be great!
Thank you in advance
T
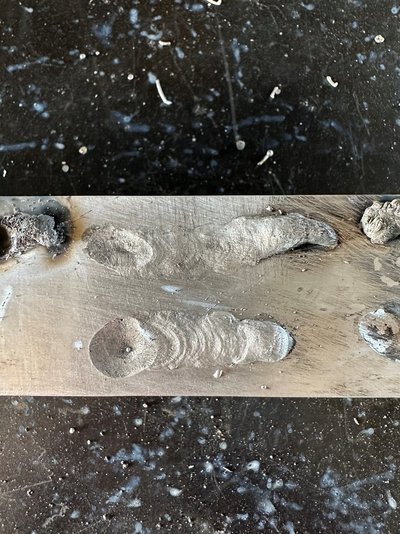
I have a Lincoln 180 dual mig with a 100SG spool gun (I'm using 220v, 100% Argon gas at 35 cuft/hr). I've been hobby welding steel for about 10 years with no issues, but aluminum is a whole new animal. I would like to build a few things out of 2 inch square tubing so I picked up a scrap piece of 1/8" wall 1.75" tubing (no scrap 2"). I have a wire feed and voltage control knob, and trying to use the settings on the chart in the welder have produced horrible results. After hours of youtube videos Im still not sure how it can be this bad, especially after watching videos where guys set up a new gun and run it relatively issue free! I have come across comments about material that is 1/8th of an inch thick will produce horrible welds, so maybe that's my issue? I'm not sold on that, as a ton of the videos guys/gals are laying down beads on aluminum plate that is thinner that 1/8". I think part of the issue is I was trying beads on the same chunk of tubing and as it got hotter, I was blowing holes through it, so I need to let the piece cool down. I need to check my wire speed as I dont know what the 1-10 settings on the dial actually mean and maybe I don't have enough wire speed for proper spray transfer. With the recommended settings on the machine, I would either pile up material and have no penetration, or blow holes though it (as seen in the first photo). Best I could do was the second photo, but the bead doesn't look good and I cant see this actually welding two pieces of aluminum together. If anyone has used this spool gun and can offer and advice that would be great!
Thank you in advance
T
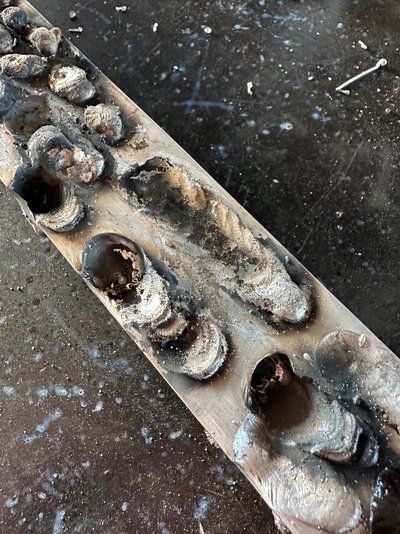
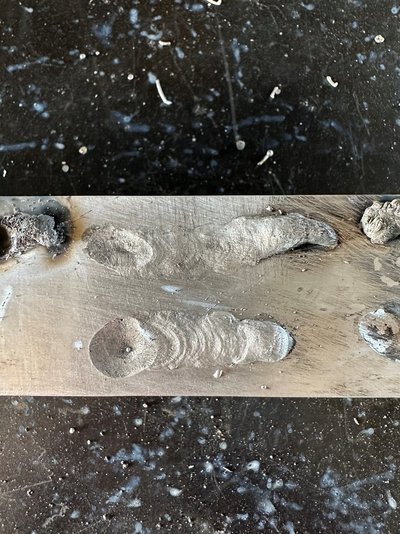