lorenzo
Member
- Messages
- 151
I think I mentioned that one half on my shop is a machine shop. This is some of the work that we do together.... the combined trade really work well together.
The piece is a solid 15.2 cm x 15.2 cm x 330.2 cm shaft that a series of paddles attaches to. As you'll see they let the bearing wear through wiping out the end.
This took 3 half length passes and 3 full length passes to build up for maching, as well as the entire day. The first 2 passes were with .035 soild wire, short circuit transfer. On the 3rd I started to use a 1/16" dual shield wire in a spray transfer.... and the 3 full length passes were done with this as well. I went back to the .035 to put in the last 1/2" of weld on the end of the shaft... the spray transfer is way too hot to build the shoulder.
Shaft chucked up in lathe
shaft chucked up in positioner
1st 1/2 pass
2nd 1/2 pass
3rd 1/2 pass
1st full pass
Checking temp... handy tool to have
Smoothed out the 1st pass... prep for 2nd
continued in next post.......
The piece is a solid 15.2 cm x 15.2 cm x 330.2 cm shaft that a series of paddles attaches to. As you'll see they let the bearing wear through wiping out the end.
This took 3 half length passes and 3 full length passes to build up for maching, as well as the entire day. The first 2 passes were with .035 soild wire, short circuit transfer. On the 3rd I started to use a 1/16" dual shield wire in a spray transfer.... and the 3 full length passes were done with this as well. I went back to the .035 to put in the last 1/2" of weld on the end of the shaft... the spray transfer is way too hot to build the shoulder.
Shaft chucked up in lathe
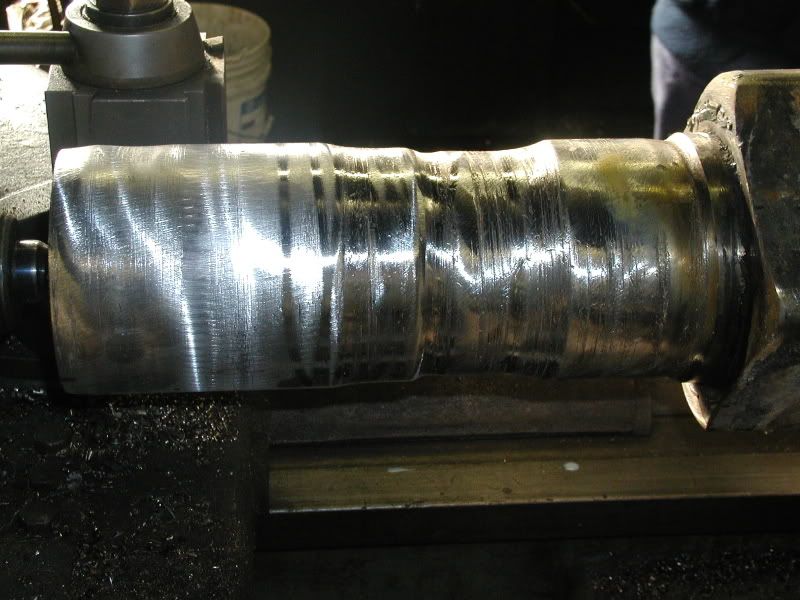
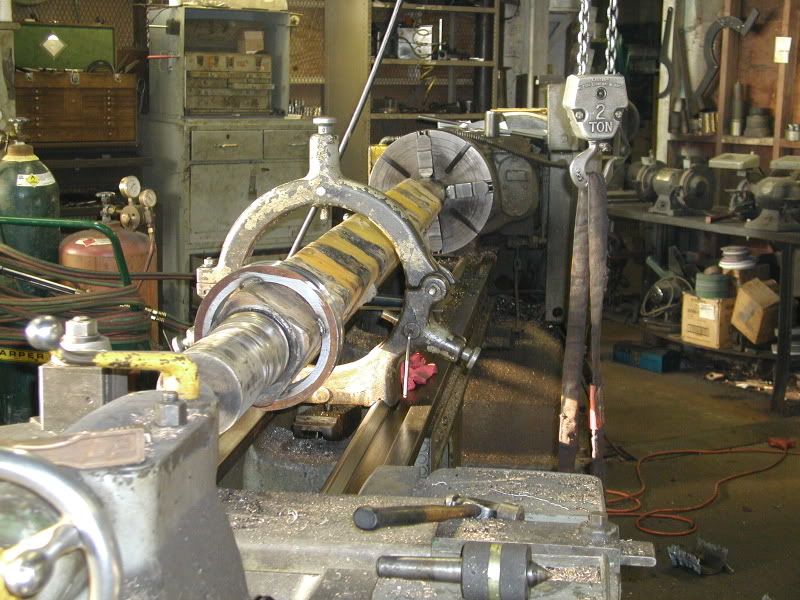
shaft chucked up in positioner
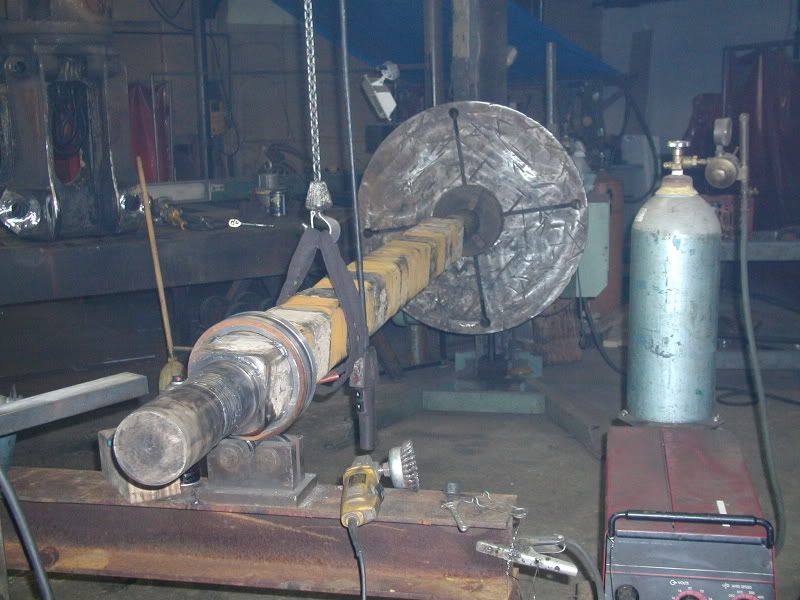
1st 1/2 pass
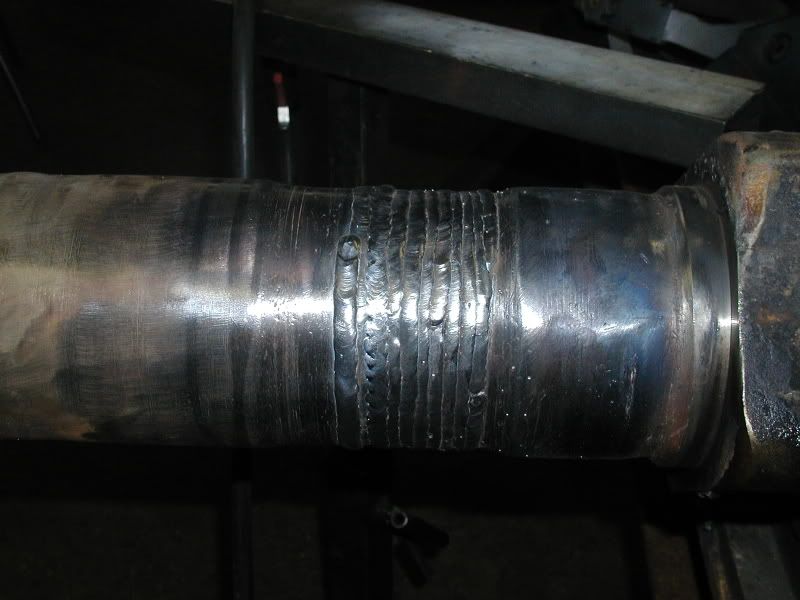
2nd 1/2 pass
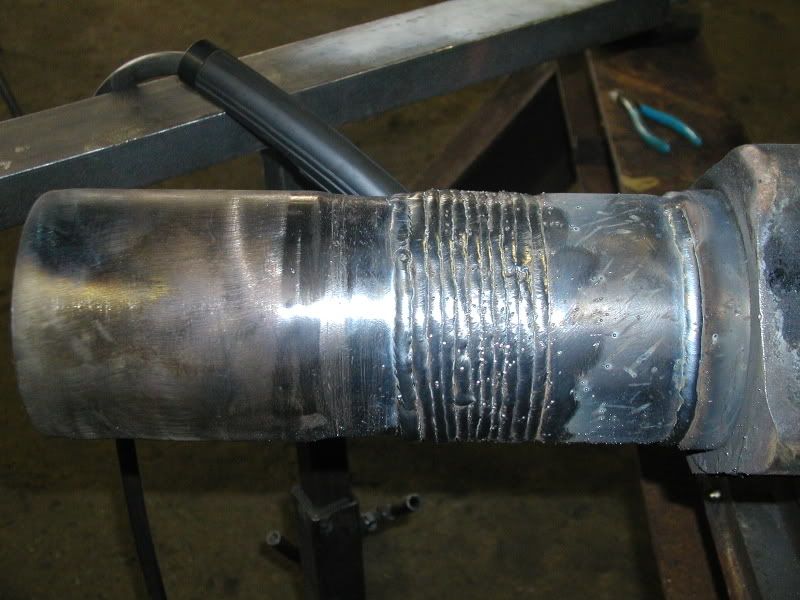
3rd 1/2 pass
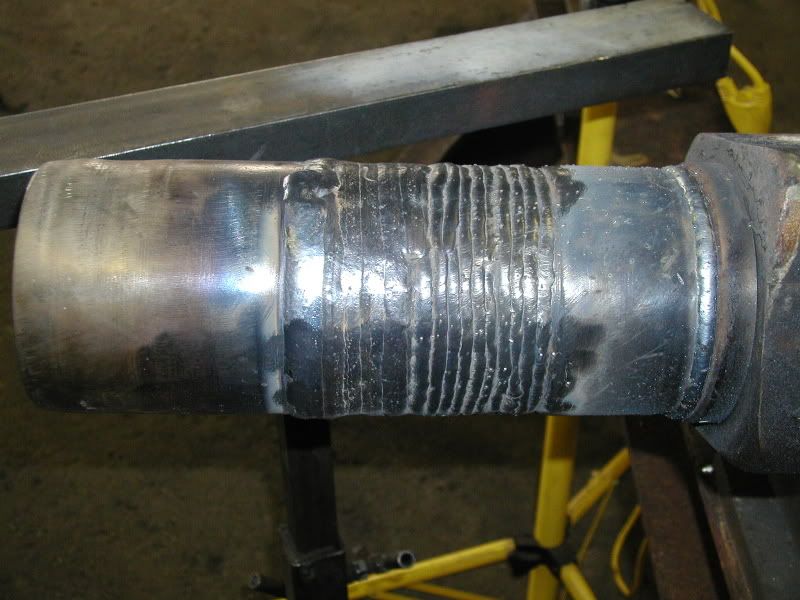
1st full pass
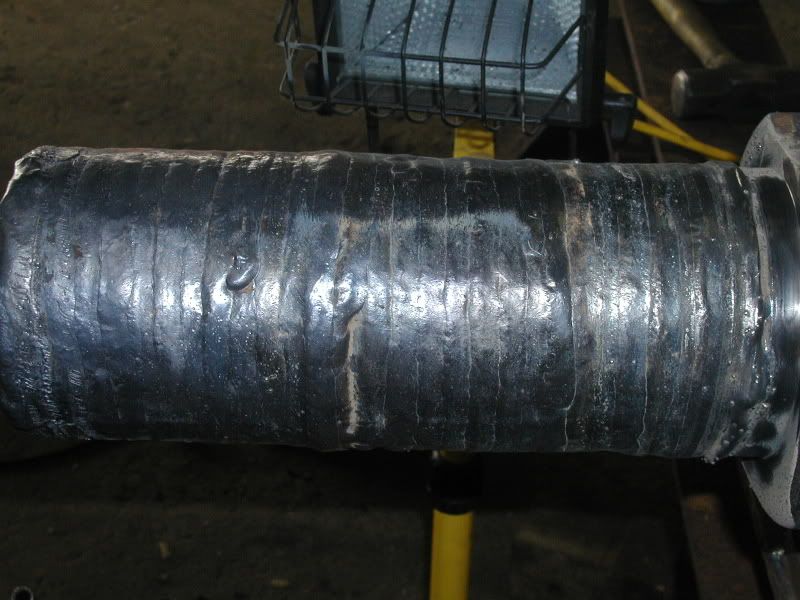
Checking temp... handy tool to have
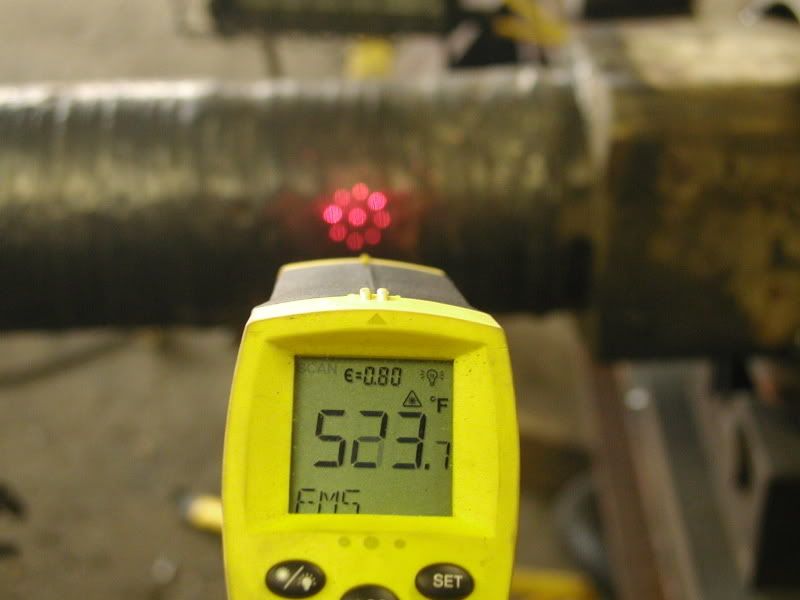
Smoothed out the 1st pass... prep for 2nd
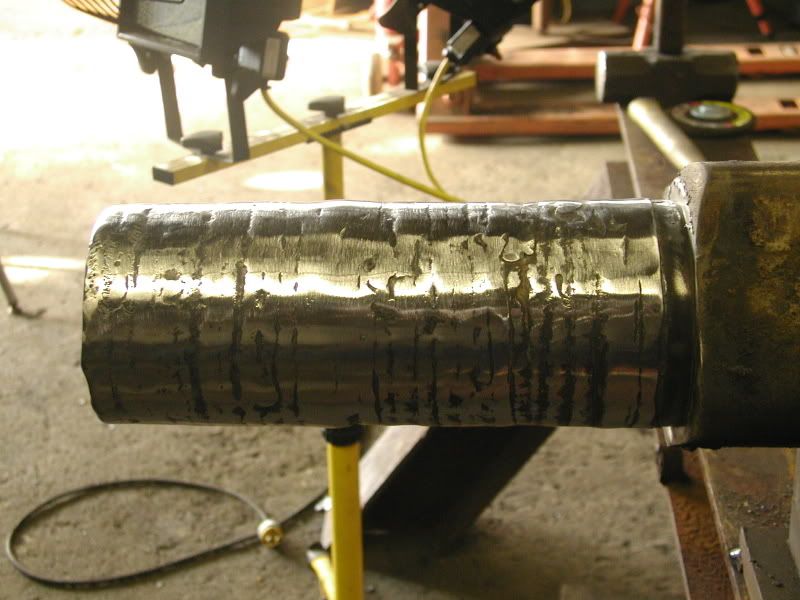
continued in next post.......