Hi there, i've been looking at this site for sometime now so thought i might aswell register.
I'm having problems with a Telwin Tecnica Plasma 30 cutter. It's been working fine up till now, but i went to use it this morning and it won't go
If i plug it in and turn it on all 4 lights on the left of the panel flash on and go off then the green one comes back on followed about 1second later by the red one, the 2 amber ones between the red and green ones don't come back on. If i press the trigger a solenoid inside the machine clicks, if i flick the switch on left of the panel down(it's sprung loaded) i get a constant steam of air from the nozzle but it still won't start when i press the trigger.
Does anybody have any ideas as to the cause of the problem?
I'm having problems with a Telwin Tecnica Plasma 30 cutter. It's been working fine up till now, but i went to use it this morning and it won't go

If i plug it in and turn it on all 4 lights on the left of the panel flash on and go off then the green one comes back on followed about 1second later by the red one, the 2 amber ones between the red and green ones don't come back on. If i press the trigger a solenoid inside the machine clicks, if i flick the switch on left of the panel down(it's sprung loaded) i get a constant steam of air from the nozzle but it still won't start when i press the trigger.
Does anybody have any ideas as to the cause of the problem?
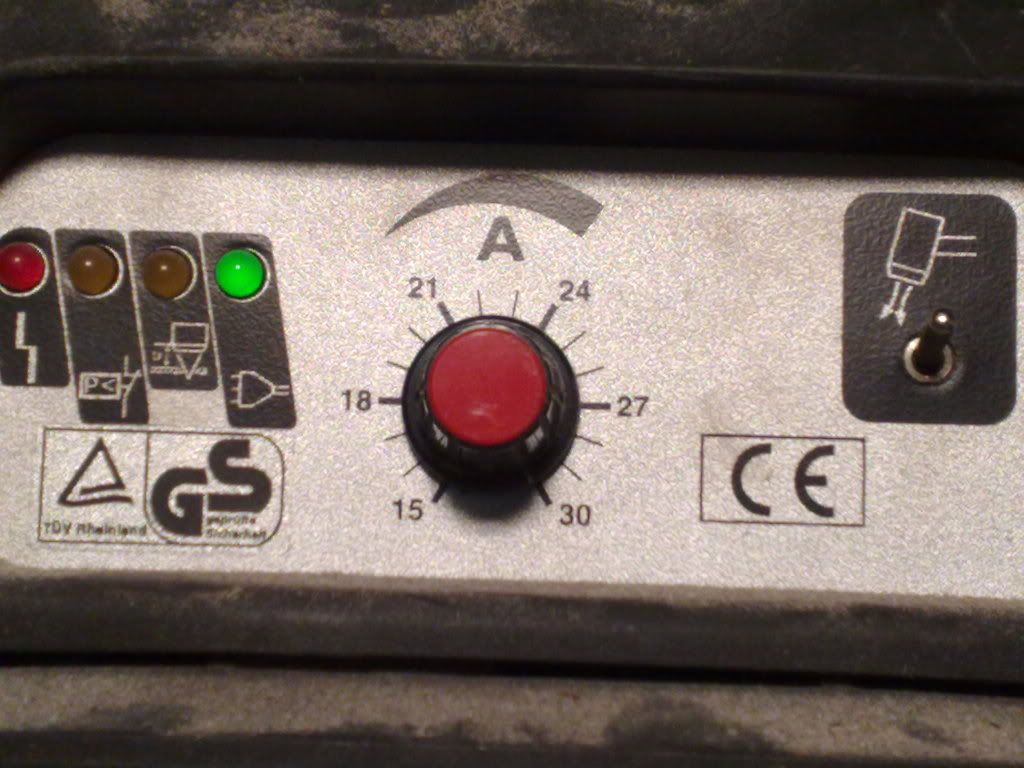