Well I thought I'd post up the pics of my first home project, which is a steel door the for the workshop I built..
Unfortunately I only thought to do pics half way through so there's a big bit in the beginning 'missing'
.
Anyway here goes! The door frame for starters, TIG'd up from 100x50 box section with 50x50 angle for the door to sit in.. I got the footplate cut from 6mm sheet.
The hinges are just tacked on for now..
The door was tacked together inside the frame so I could make sure the gaps were all spot on..
Then once I was happy with the fit all the joins were seem welded and I cut the door skin to fit, which was then drilled for plug welding.
Stuck on in 20 mins with the MIG
A couple from the back..
The recesses for the mortice locks were cut much earlier (chain drilled and filed), but like I said I only thought to do pictures yesterday lol
And that's where I'm upto now, door half skinned, waiting for welds to be ground off and to be trial fitted to the frame
Will keep the updates coming
cheers
Greg
Unfortunately I only thought to do pics half way through so there's a big bit in the beginning 'missing'

Anyway here goes! The door frame for starters, TIG'd up from 100x50 box section with 50x50 angle for the door to sit in.. I got the footplate cut from 6mm sheet.
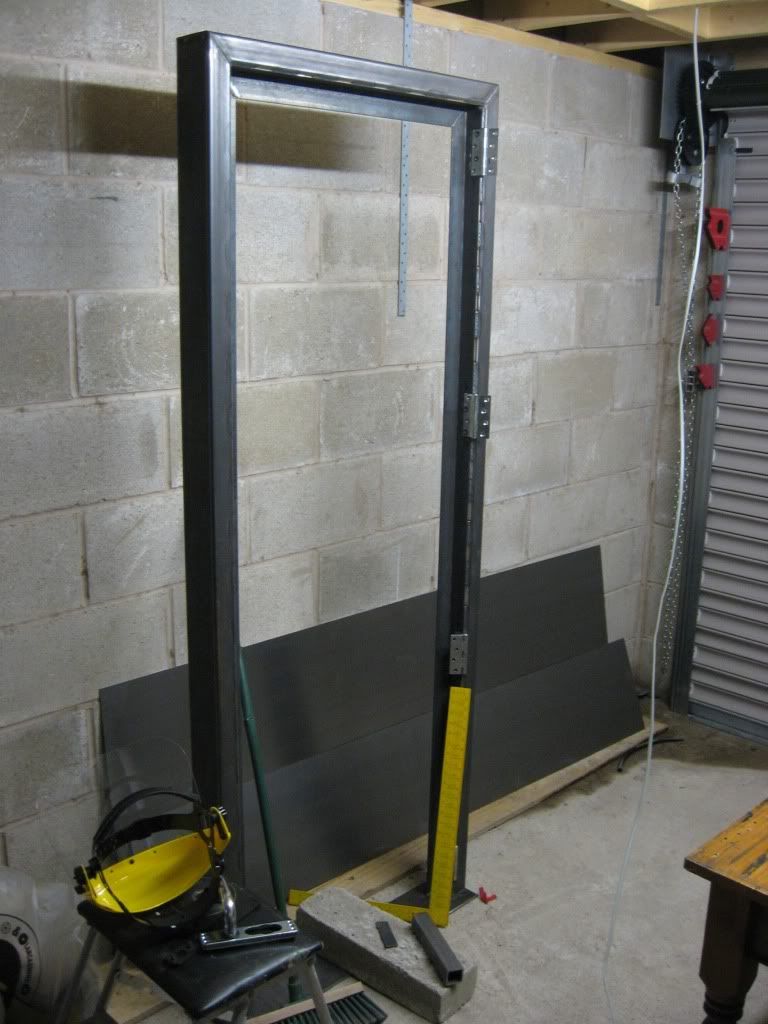
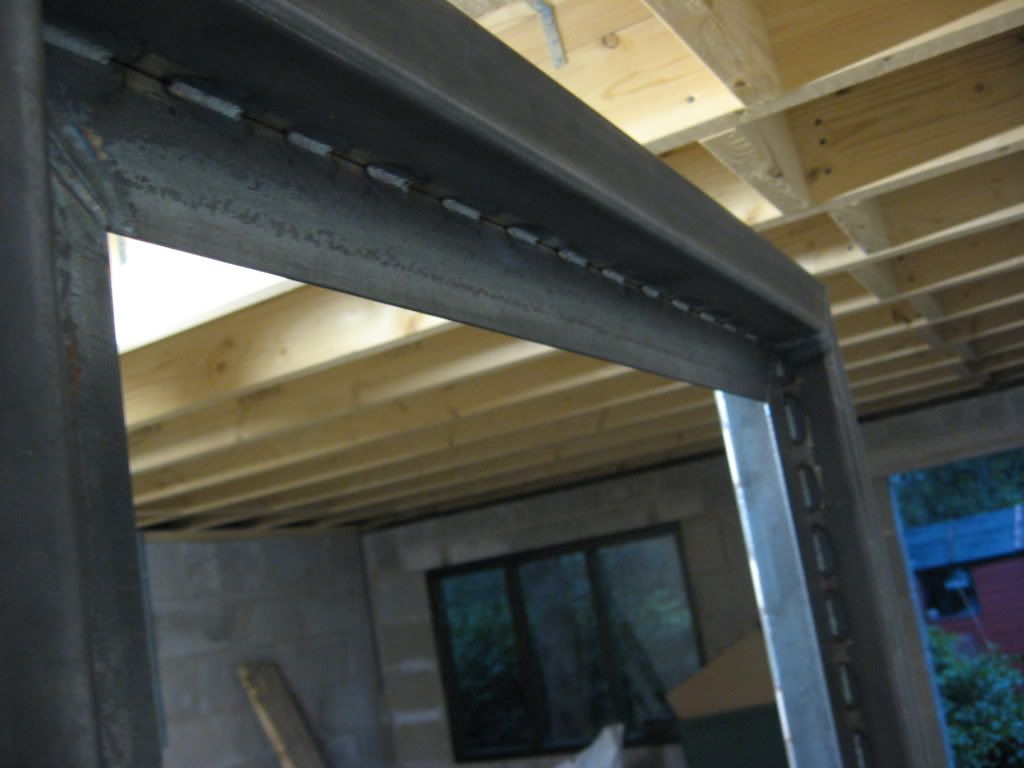
The hinges are just tacked on for now..
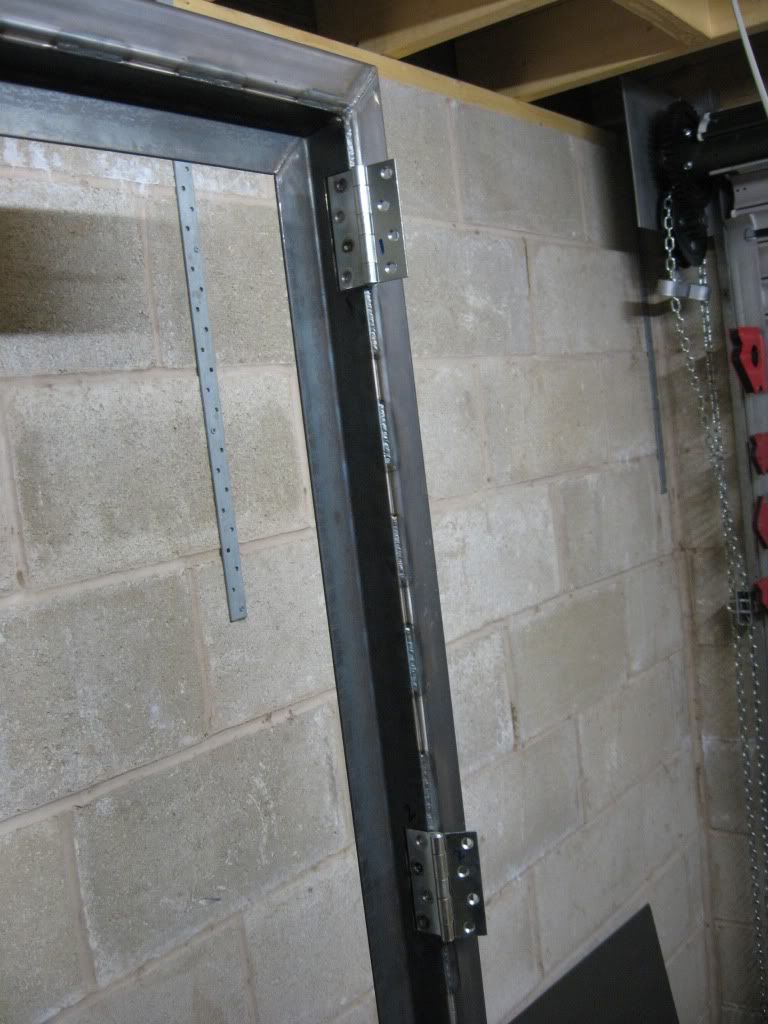
The door was tacked together inside the frame so I could make sure the gaps were all spot on..
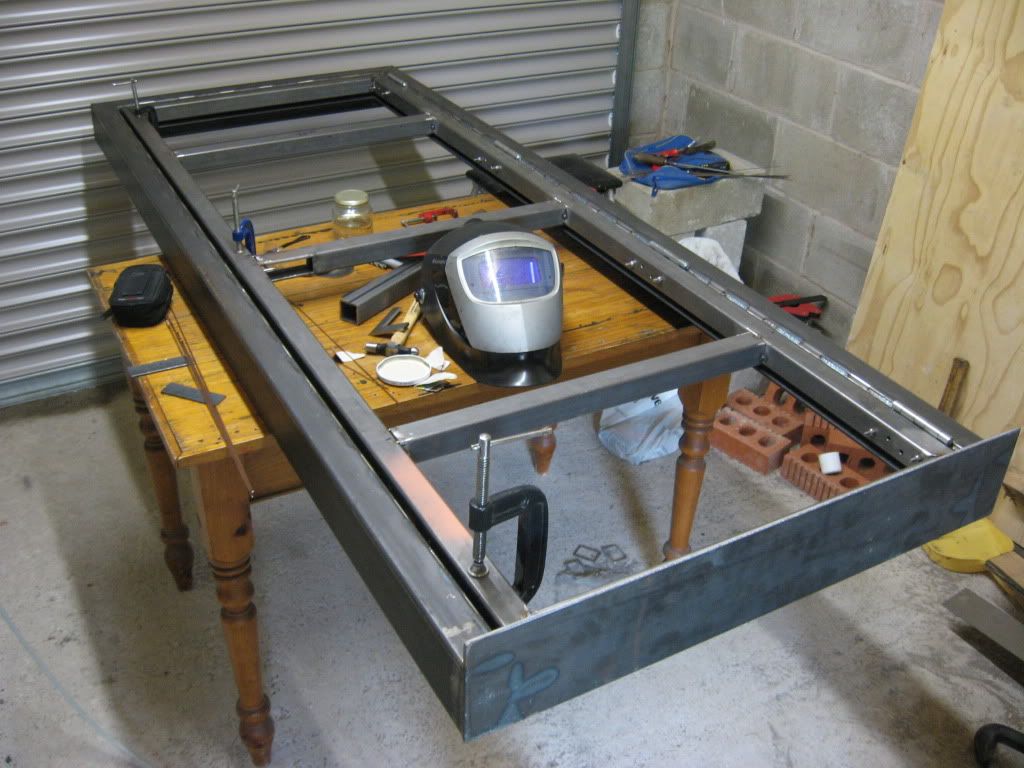
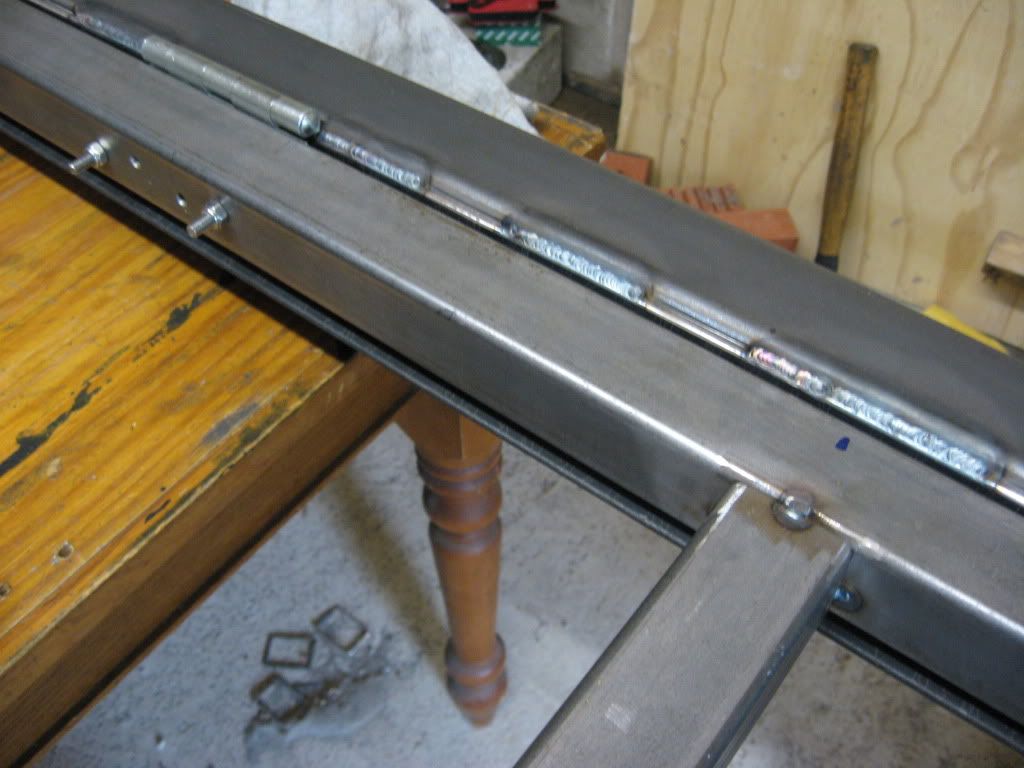
Then once I was happy with the fit all the joins were seem welded and I cut the door skin to fit, which was then drilled for plug welding.
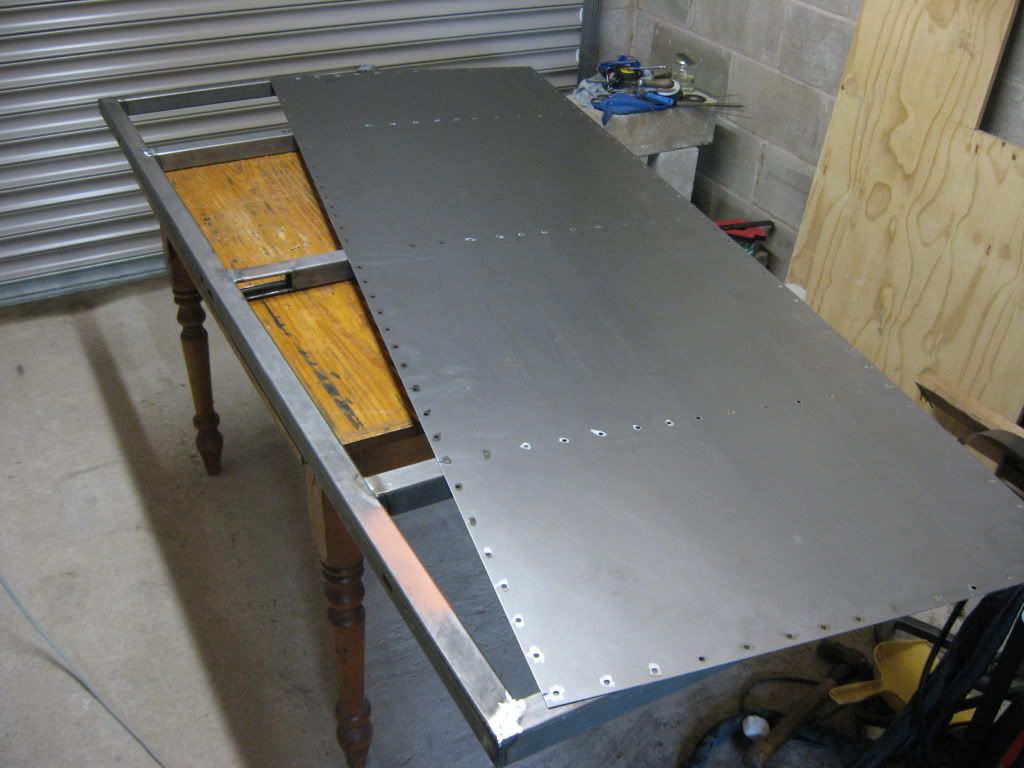
Stuck on in 20 mins with the MIG

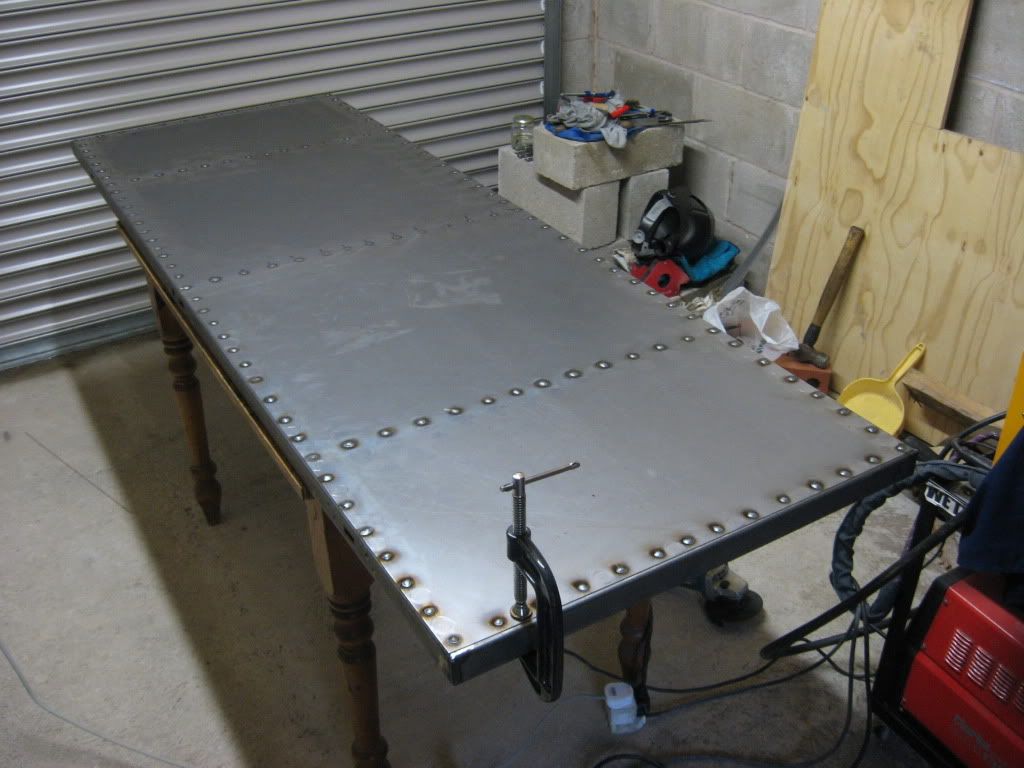

A couple from the back..
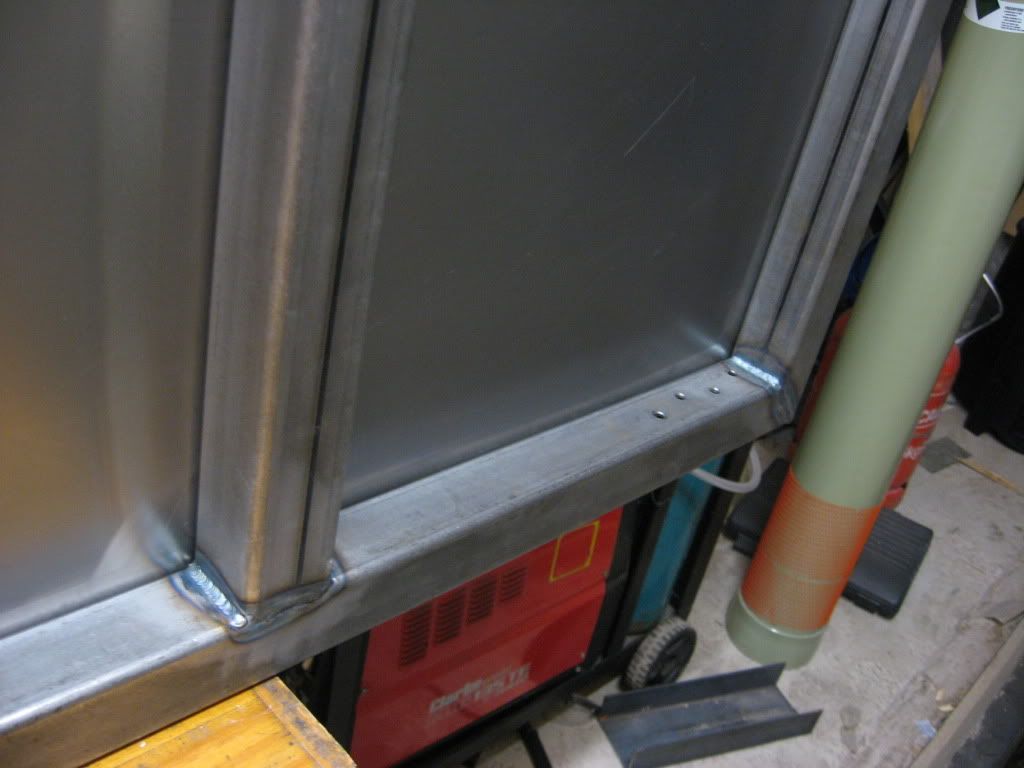
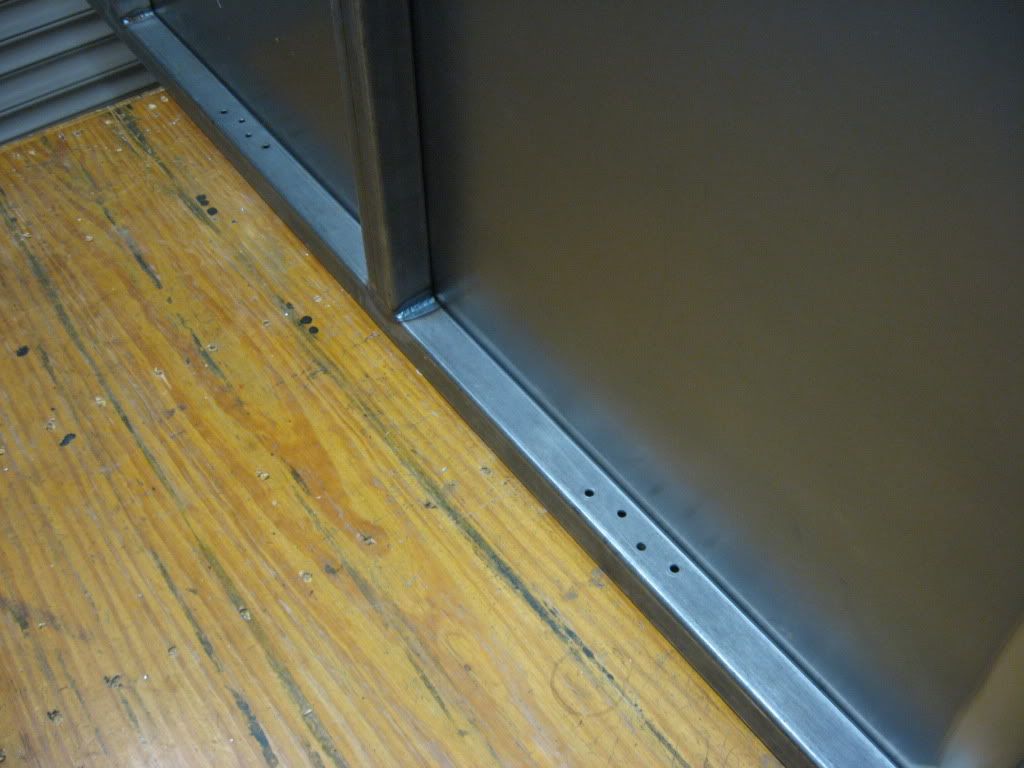
The recesses for the mortice locks were cut much earlier (chain drilled and filed), but like I said I only thought to do pictures yesterday lol

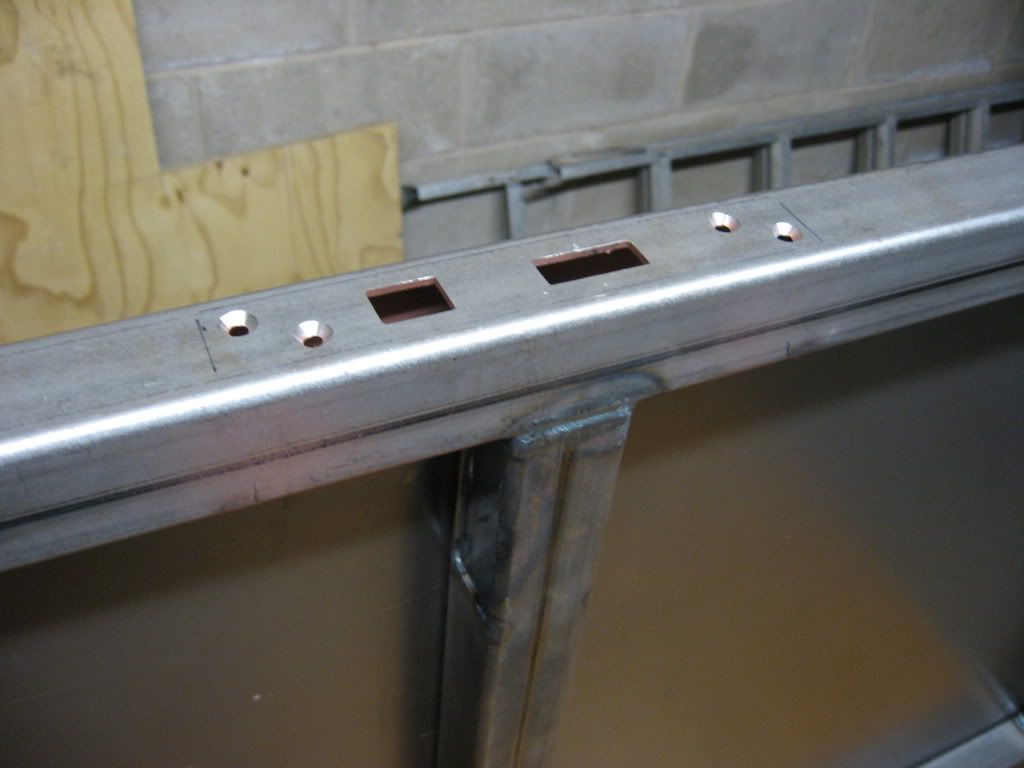
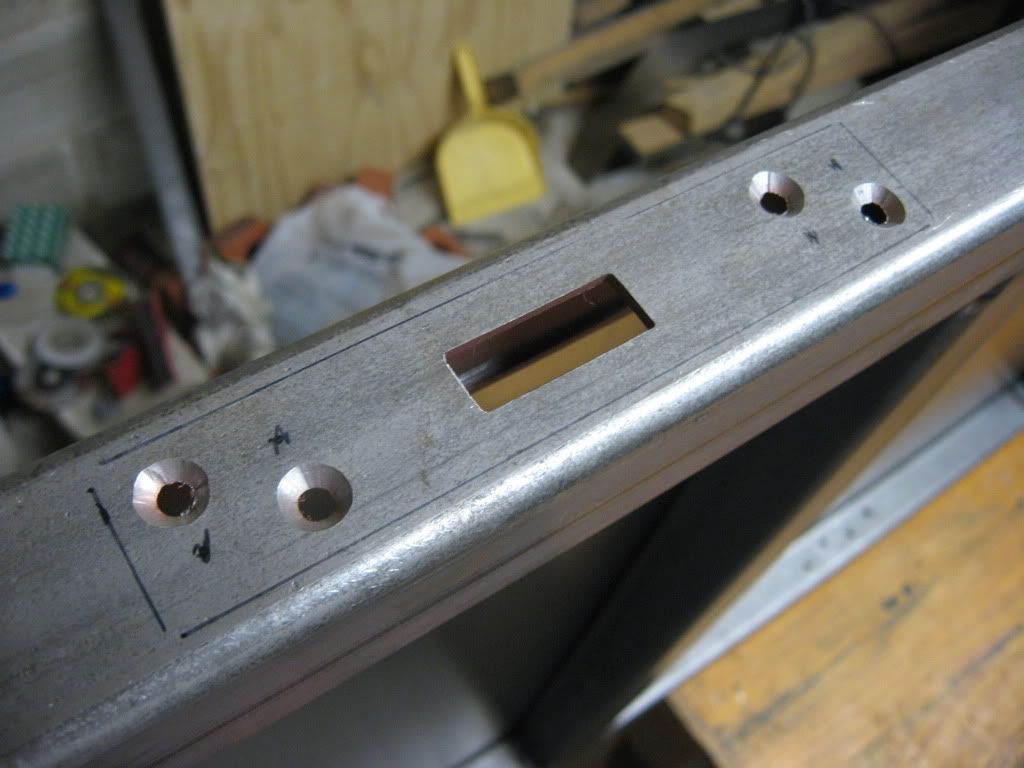
And that's where I'm upto now, door half skinned, waiting for welds to be ground off and to be trial fitted to the frame

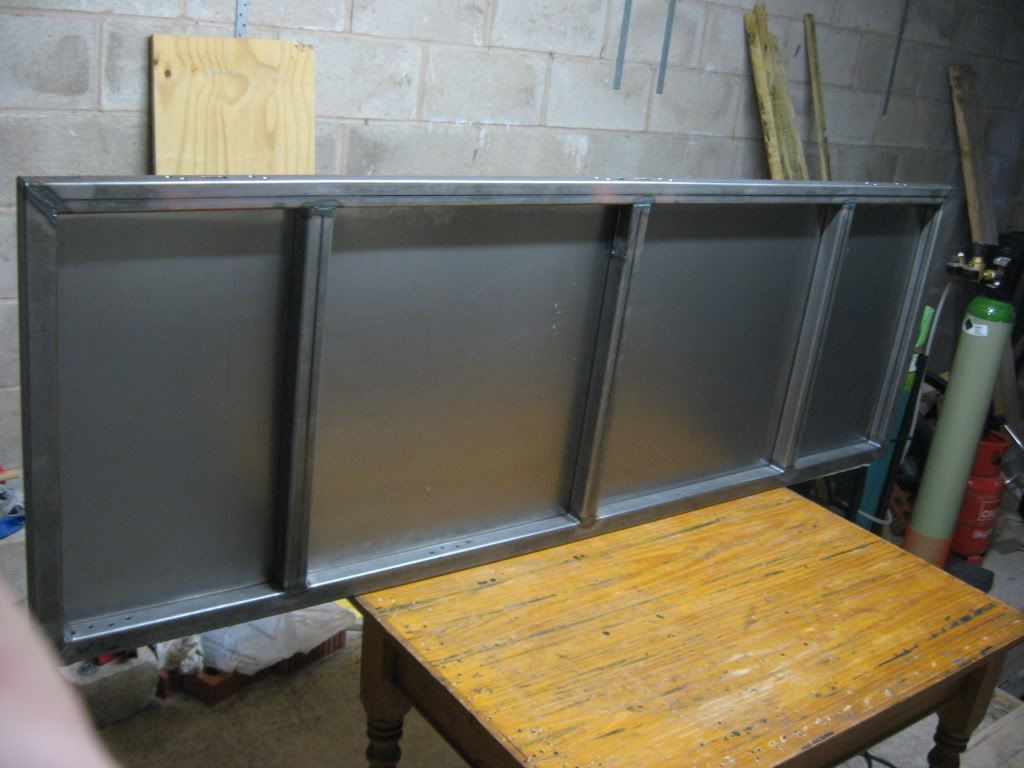
Will keep the updates coming

cheers
Greg