so i thank you all for my help choosing my regulator , heres how my story goes since :P feel free to laugh
i watch the vid to learn what to do, so as a check list for myself lol
1. as instructions say and i dont think they should ''sniff the gas bottle before attach regulator''
so as i put my nose on the... NO lol i didnt tho i see some idiots might lol (TURN THE GAS ON AND OFF BRIEFLY to disslodge anything in passage to bottle, , done
2. attach regulator tighten the nut,
3. put my pipe on the plastic gas pipe, and clip to my regulator,
4. turn slightly til needle moves, then open all the way! (standing back ready to run a mile)
5. press the gun and adjust to 10lpm (i think ive just answered what ima bout to ask !!) 6. my welder wire was already set up previously and checked over 0.8mm wire
now! settings.... i see on here there is a guide
''The settings are as followed
Push the middle rocker switch up then for the settings starting at low - high
1 Low Min
2 Low Med
3 Low Max
Push the middle rocker switch up then for the settings starting at high
4 High Min
5 High Med
6 High Max
Work on each of these setting for every 1mm thickness as a guide but remember that at the highest setting your welder will only work for a short time before cutting out on thermals.''
so these setting are done using 3 switches, ....im playing with them form what i THINK is min, going up a setting to try make it start better on the metal (thicknes)
i start layin the beads down! i wil get my pics for ya at the end, now i had a few pop pop stick pop stick while i got the hang of the gas and mig being totaly different from stickwelding,
now i lay down some lines, albeit slightly messy /wobbly due to my steady hand ( i was bent over on the seat as i havent made a table yet which didnt help i found the angle being straigh down better than holding it like a stick,
i am so confused with the settings i think im getting it,
it was stickign to the nozzle, so i increased line speed ...seemed to help some stoped it spitting but occasionaly shot out line if i missed disstance, (im clipping it off with pliers when it does that is there a more practical way of saving it without goind inside?)
NOW!!! confident i can lay lines down where i like with penetration visible on the otherwise
i am SO IMPRESSED how tidy it is and slag free compared to stick like OMG wow, its not a big fat lump its tidy ..ish the holes was whiel i was playing with movement speed
its thin? this due to the wire thickness i guess,
so MIG is EASY AS HELL!!! but at the same time HARD as BALLS! im confused lol
so i take 2 sheets and im going to join them,
i blast the paint off with my grinder set them up, and away i go!!! NOPE!! why?? AWAY I GO!!!...nope ya dont ... 10 times over playign with the settings i was sure i understood and worked on my other 2mm sheet metal, now im using 3mm it must need more power settings? same on every setting wtf?? just makign dots allover the metal on this ?
now as i said i think ive answered it? did i need to adjust the gas regulator to more gas pm ? is it about the gas regulation?
sorry the pics are dark, i havent wired them off bit black from gas i think .
so critisize my work or im not gona get better, this was a quick first time blast on the mig it was cool,
my main questions,
1.MIGMATE TURBO 105 setting switches? if u got 1 please explain lol im googling and playing 2moro
2.i was making lines changed to a sheet 1mm more, and setting switches didnt help... do i need to adjust the gas? - again im googling this cause i cant stop learning, i just want to be active here and learn
and i love talking about what im doing .. my friends not interested in metal unfortunatly lol
3Does the nozzle being old and slightly dirty and the middle copper piece that feeds wires slightly worn be a problem in the sticking or weld?
4.ANY tips advice welcome
i watch the vid to learn what to do, so as a check list for myself lol
1. as instructions say and i dont think they should ''sniff the gas bottle before attach regulator''
so as i put my nose on the... NO lol i didnt tho i see some idiots might lol (TURN THE GAS ON AND OFF BRIEFLY to disslodge anything in passage to bottle, , done
2. attach regulator tighten the nut,
3. put my pipe on the plastic gas pipe, and clip to my regulator,
4. turn slightly til needle moves, then open all the way! (standing back ready to run a mile)
5. press the gun and adjust to 10lpm (i think ive just answered what ima bout to ask !!) 6. my welder wire was already set up previously and checked over 0.8mm wire
now! settings.... i see on here there is a guide
''The settings are as followed
Push the middle rocker switch up then for the settings starting at low - high
1 Low Min
2 Low Med
3 Low Max
Push the middle rocker switch up then for the settings starting at high
4 High Min
5 High Med
6 High Max
Work on each of these setting for every 1mm thickness as a guide but remember that at the highest setting your welder will only work for a short time before cutting out on thermals.''
so these setting are done using 3 switches, ....im playing with them form what i THINK is min, going up a setting to try make it start better on the metal (thicknes)
i start layin the beads down! i wil get my pics for ya at the end, now i had a few pop pop stick pop stick while i got the hang of the gas and mig being totaly different from stickwelding,
now i lay down some lines, albeit slightly messy /wobbly due to my steady hand ( i was bent over on the seat as i havent made a table yet which didnt help i found the angle being straigh down better than holding it like a stick,
i am so confused with the settings i think im getting it,
it was stickign to the nozzle, so i increased line speed ...seemed to help some stoped it spitting but occasionaly shot out line if i missed disstance, (im clipping it off with pliers when it does that is there a more practical way of saving it without goind inside?)
NOW!!! confident i can lay lines down where i like with penetration visible on the otherwise
i am SO IMPRESSED how tidy it is and slag free compared to stick like OMG wow, its not a big fat lump its tidy ..ish the holes was whiel i was playing with movement speed
its thin? this due to the wire thickness i guess,
so MIG is EASY AS HELL!!! but at the same time HARD as BALLS! im confused lol
so i take 2 sheets and im going to join them,
i blast the paint off with my grinder set them up, and away i go!!! NOPE!! why?? AWAY I GO!!!...nope ya dont ... 10 times over playign with the settings i was sure i understood and worked on my other 2mm sheet metal, now im using 3mm it must need more power settings? same on every setting wtf?? just makign dots allover the metal on this ?
now as i said i think ive answered it? did i need to adjust the gas regulator to more gas pm ? is it about the gas regulation?
sorry the pics are dark, i havent wired them off bit black from gas i think .
so critisize my work or im not gona get better, this was a quick first time blast on the mig it was cool,
my main questions,
1.MIGMATE TURBO 105 setting switches? if u got 1 please explain lol im googling and playing 2moro
2.i was making lines changed to a sheet 1mm more, and setting switches didnt help... do i need to adjust the gas? - again im googling this cause i cant stop learning, i just want to be active here and learn

3Does the nozzle being old and slightly dirty and the middle copper piece that feeds wires slightly worn be a problem in the sticking or weld?
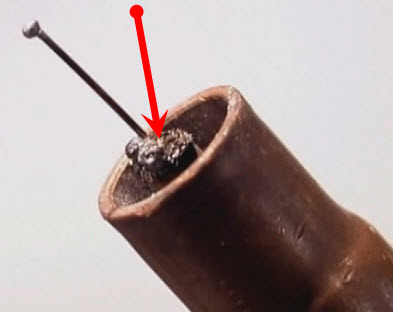
4.ANY tips advice welcome