shenion
Tool Pack Rat
- Messages
- 7,586
- Location
- Stone Mountain, GA USA
The before:
0.030 (0.8mm) wire, argon gas, 0.9mm tip, 1/8" Al.
Real issues with feed and overheating the wire. If the welder had a 20-amp setting, it would have worked better.
Still, the wire feed was difficult. The wire would stutter causing the blobs. Tension screw as almost all the way out. If you hit a rough spot and the the wire hit the metal a good amount of time, I would end up with a birdsnest.
Still, I could do only about 1" then the tip would overheat and the wire would stick. I found one big help was increasing the gas to about 16L/m. That kept the wire cooler and it did not tend to melt back to the tip. But, that caused the welds to be tall.
The after:
Top piece is 1/8" bottom is 18GA (1.5mm)
Much better. The top was my first try (done right to left). The blob 1/3 way through was actually me seeing how hard it is blow through from the back.
Bottom is pull (center) then 2 push with various wire feed settings.
Ok, so the difference?
First installed a nylon liner. Really that did not make a big difference. Most of the drag was in the gun. The roller would make the soft wire kinda triangle shaped, these sharp edges would bind on the gun/tip. The wire fed easily until it hit the gun.
The big change is the wire. I picked up some 0.8 (0.030) 4043 Al wire; that is all you can get at the home supply/tool supply places here.
I ordered some 0.035 (0.9mm) 5356 wire. There are 2 significant differences:
1. thicker wire can handle the minimum 30A setting of the Clarke 130.
2. The wire is much stiffer and harder. So it is not deformed by the rollers, feeds easily.
Actually the Al wire feels almost as stiff as my 0.30 steel wire.
To summarize (could be added to tutorial):
1. Forget 0.030 (0.76mm) 4043 wire unless you have a spool gun.
2. 5365 wire will feed easier as it is harder and will not deform.
3. 0.035 (0.9mm) wire is needed on MIGs that do not have low amp settings
4. 0.9mm wire will feed better.
5. Some tuning of the heat can be done with the gas flow. This is significant if the wire tends to melt back to the tip.
6. Use larger tip than the wire.
7. Al welding is fast, all the welds shown were probably less than 8-10 seconds.
There are other Al wires. I chose the 5365 as the supplier quoted it is "the easiest to feed and one of the strongest".
I was surprised on the thin Al that it still worked with the 0.035 wire. Just takes careful movement to keep from blowing through.
Ok, so looks like I'm up to speed
Thanks all for the advice.
Oh, if you forget to turn on the gas with Al, you will have yourself a sloppy plasma cutter.
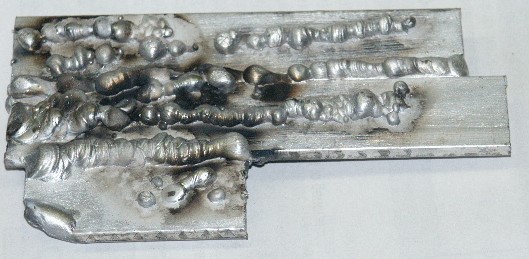
0.030 (0.8mm) wire, argon gas, 0.9mm tip, 1/8" Al.
Real issues with feed and overheating the wire. If the welder had a 20-amp setting, it would have worked better.
Still, the wire feed was difficult. The wire would stutter causing the blobs. Tension screw as almost all the way out. If you hit a rough spot and the the wire hit the metal a good amount of time, I would end up with a birdsnest.
Still, I could do only about 1" then the tip would overheat and the wire would stick. I found one big help was increasing the gas to about 16L/m. That kept the wire cooler and it did not tend to melt back to the tip. But, that caused the welds to be tall.
The after:

Top piece is 1/8" bottom is 18GA (1.5mm)
Much better. The top was my first try (done right to left). The blob 1/3 way through was actually me seeing how hard it is blow through from the back.
Bottom is pull (center) then 2 push with various wire feed settings.
Ok, so the difference?
First installed a nylon liner. Really that did not make a big difference. Most of the drag was in the gun. The roller would make the soft wire kinda triangle shaped, these sharp edges would bind on the gun/tip. The wire fed easily until it hit the gun.
The big change is the wire. I picked up some 0.8 (0.030) 4043 Al wire; that is all you can get at the home supply/tool supply places here.
I ordered some 0.035 (0.9mm) 5356 wire. There are 2 significant differences:
1. thicker wire can handle the minimum 30A setting of the Clarke 130.
2. The wire is much stiffer and harder. So it is not deformed by the rollers, feeds easily.
Actually the Al wire feels almost as stiff as my 0.30 steel wire.
To summarize (could be added to tutorial):
1. Forget 0.030 (0.76mm) 4043 wire unless you have a spool gun.
2. 5365 wire will feed easier as it is harder and will not deform.
3. 0.035 (0.9mm) wire is needed on MIGs that do not have low amp settings
4. 0.9mm wire will feed better.
5. Some tuning of the heat can be done with the gas flow. This is significant if the wire tends to melt back to the tip.
6. Use larger tip than the wire.
7. Al welding is fast, all the welds shown were probably less than 8-10 seconds.
There are other Al wires. I chose the 5365 as the supplier quoted it is "the easiest to feed and one of the strongest".
I was surprised on the thin Al that it still worked with the 0.035 wire. Just takes careful movement to keep from blowing through.
Ok, so looks like I'm up to speed

Thanks all for the advice.
Oh, if you forget to turn on the gas with Al, you will have yourself a sloppy plasma cutter.
